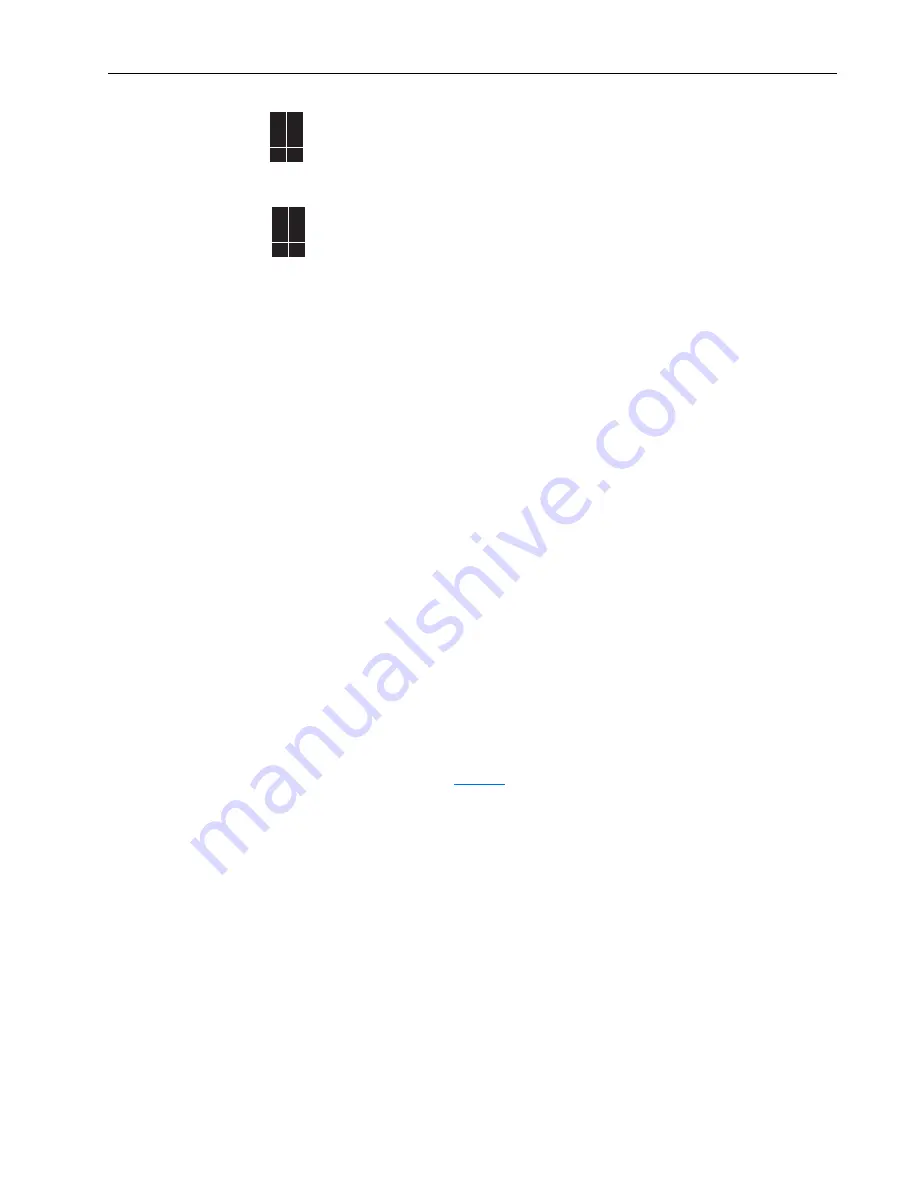
DriveGuard
39
DriveGuard
Refer to “
DriveGuard Safe-Off User Manual”
publication PFLEX-UM001.
Drive Overload
The drive overload function has two separate protection schemes, an inverse time
protection based on current, and thermal manager based on measured power
module temperature and operating conditions. The drive may fold back current
limit when either of these methods detects a problem.
Any protection for the motor and associated wiring is provided by a Motor Thermal
Overload feature.
The drive will monitor the temperature of the power module based on a measured
temperature and a thermal model of the power module. As the temperature rises the
drive may lower the PWM frequency to decrease the switching losses in the power
module. If the temperature continues to rise, the drive may reduce current limit to
try to decrease the load on the drive. If the drive temperature becomes critical, the
drive will generate a fault.
If the drive is operated in a low ambient condition the drive may exceed rated levels
of current before the monitored temperature becomes critical. To guard against this
situation the drive thermal overload also includes an inverse time algorithm. When
this scheme detects operation beyond rated levels, current limit may be reduced or a
fault may be generated.
Normal Duty and Heavy Duty Operation
Applications require different amounts of overload current. Sizing a drive for
Normal Duty provides 110% for 60 seconds and 150% for 3 seconds. For a heavy
duty application, one larger rating of a drive is used (in comparison to the motor),
and therefore provides a larger amount of overload current in comparison to the
motor rating. Heavy duty sizing will provide at least 150% for 60 seconds and
200% for 3 seconds. These percentages are with respect to the connected motor
rating.
Inverse Time Protection
The lower curve in
Figure 2
shows the boundary of normal-duty operation, where
the drive is rated to produce 110% of rated current for 60 seconds, 150% of rated
current for three seconds, and 165% of rated current for 100 milliseconds. The
maximum value for current limit is 150% so the limit of 165% for 100 milliseconds
should never be crossed. If the load on the drive exceeds the level of current as
shown on the upper curve, current limit may fold back to 100% of the drive rating
until the 10/90 or 5/95 duty cycle has been achieved. For example, 60 seconds at
110% will be followed by 9 minutes at 100%, and 3 seconds at 150% will be
followed by 57 seconds at 100%. With the threshold for where to take action
slightly above the rated level the drive will only fold back when drive ratings are
exceeded.
If fold back of current limit is not enabled in [Drive OL Mode], the drive will
generate a F64 Drive Overload fault when operation exceeds the rated levels.
70EC
700VC
700H
✔
70EC
700VC
700H
✔ ✔