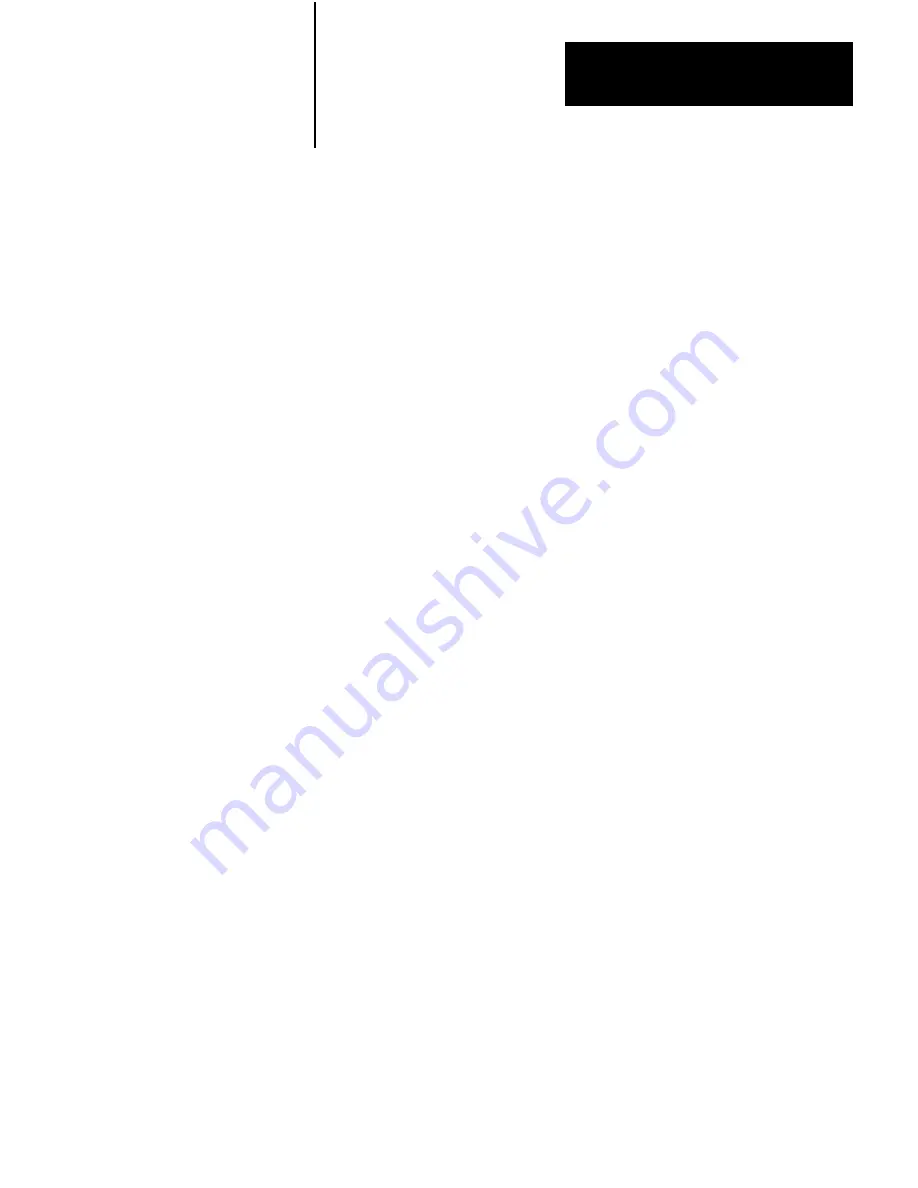
Controller Components
Chapter 2
211
INTERFACE Socket
The 15-pin socket labeled INTERFACE is used in connecting the Processor to
the Industrial Terminal (Cat. No. 1770-T3) for programming, report generation
or monitoring. This socket is also used to connect an external Battery Pack to
the Processor so the Processor can be removed from the I/o Chassis without loss
of memory. When programming an EPROM this INTERFACE socket is used
to connect the 25.5V Power Supply to the Processor.
EPROM Access Door
The EPROM Access Door on the side of the Processor covers a 28-pin EPROM
socket, which is used to house an optional 24-pin EPROM memory chip
(Erasable Programmable Read Only memory) (Cat. No. 1770-XP). The
EPROM provides the user with a 2K word non-volatile memory backup system.
Programmed EPROMs can be erased with an ultraviolet light as described in
Publication 1770-915, EPROM Programming.
Memory Write Protect
When a programmed EPROM is in place in the Processor, a Memory Write
Protect feature becomes active. This means values from word address 2008 to
the end of memory are protected and cannot be altered by programming.
The I/O Modules (Figure 2-6) contain the necessary circuitry to interface the
user’s I/O devices to the Mini-PLC-2/15 Processor.
Each I/O circuit has optical isolation to guard against high-voltage transients
that can damage the Mini-PLC-2/15 Controller’s logic circuitry. Optical
isolation is rated at 1500V RMS.
Many Input Modules have filtering circuitry to suppress contact bounce and to
guard against recognition of transients as data.
Most I/O modules have indicators that show the ON/OFF status of each input or
output device connected to it. These indicators are useful during start-up,
monitoring, and troubleshooting. Output modules with fuses also have an
additional indicator that illuminates if an output fuse in the module has blown.
I/O modules are available for devices with different voltage levels and
characteristics. A color-coded label on each I/O module identifies the general
type of module and voltage range. Table 1.A lists the general information on
each I/O Module and the Processor Module. The Product Data Sheets for the
I/O Modules include a detailed description, Module specifications, connection
diagrams and keying information.
Input/Output Modules
Artisan Technology Group - Quality Instrumentation ... Guaranteed | (888) 88-SOURCE | www.artisantg.com