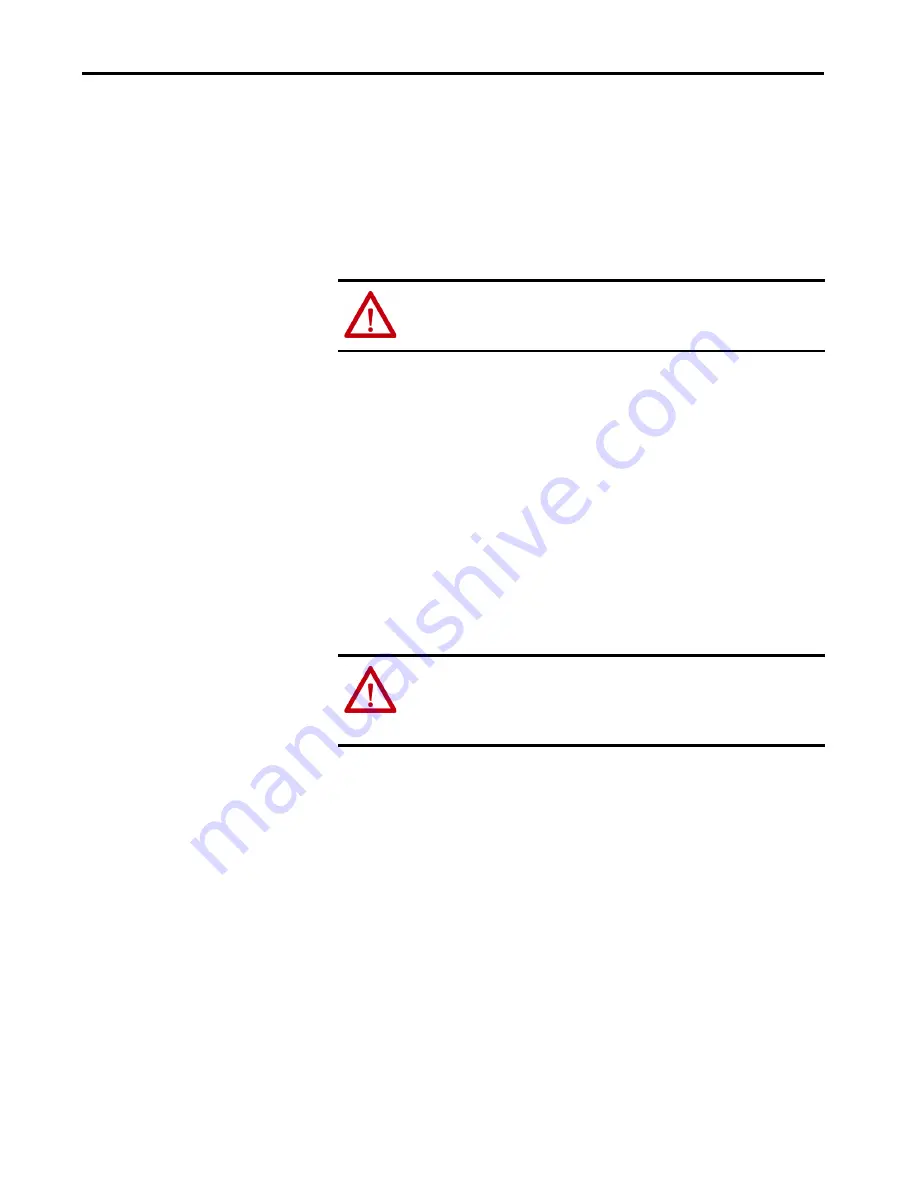
Rockwell Automation Publication ICSTT-RM446N-EN-P - April 2018
95
AADvance Functional Safety System Implementation
Chapter 4
for safety-related inputs and outputs should be implemented using the
application program instead.
The Force LED on the front of the T9110 Processor Module indicates when
one or more I/O points are forced. The application program can determine
how many points are currently forced; it is highly recommended that this
information be used to control an additional status display and/or for logging
purposes.
A list of the currently locked points is read back from the AADvance system
and made available within the AADvance Workbench.
Maintenance Overrides
Maintenance Overrides
set inputs or outputs to a defined state that can be
different from the real state during safety operation. It is used during
maintenance, usually to override input or output conditions in order to
perform a periodic test, calibration or repair of a module, sensor or actuator.
To correctly implement a maintenance override scheme within the AADvance
system, the override or 'bypass' logic shall be programmed within the
Application Program, with a separate set of safety-related input points or
variables enabling the bypass logic.
There are two basic methods to check safety-related peripherals connected to
the AADvance system:
• External hard-wired switches are connected to conventional system
inputs. These inputs are used to deactivate sensors and actuators during
maintenance. The maintenance condition is handled as part of the
system's application program.
• Sensors and actuators are electrically switched off during maintenance
and are checked manually.
In some installations, the maintenance console may be integrated with the
operator display, or maintenance may be covered by other strategies. In such
installations, the guidance given in section “Input and Output Forcing” is to be
followed. A checklist for the application of overrides is given in the Checklists
chapter.
ATTENTION:
If the forcing facility is used when the system is in-service, a
safety related input connected to an operator accessible switch shall be
implemented to initiate the removal of the force condition.
ATTENTION:
In order to accommodate maintenance overrides safely, TÜV
has documented a set of principles that shall be followed. These principles
are published in the document "Maintenance Override" by TÜV
Süddeutschland / TÜV Product Service GmbH and TÜV Rheinland.