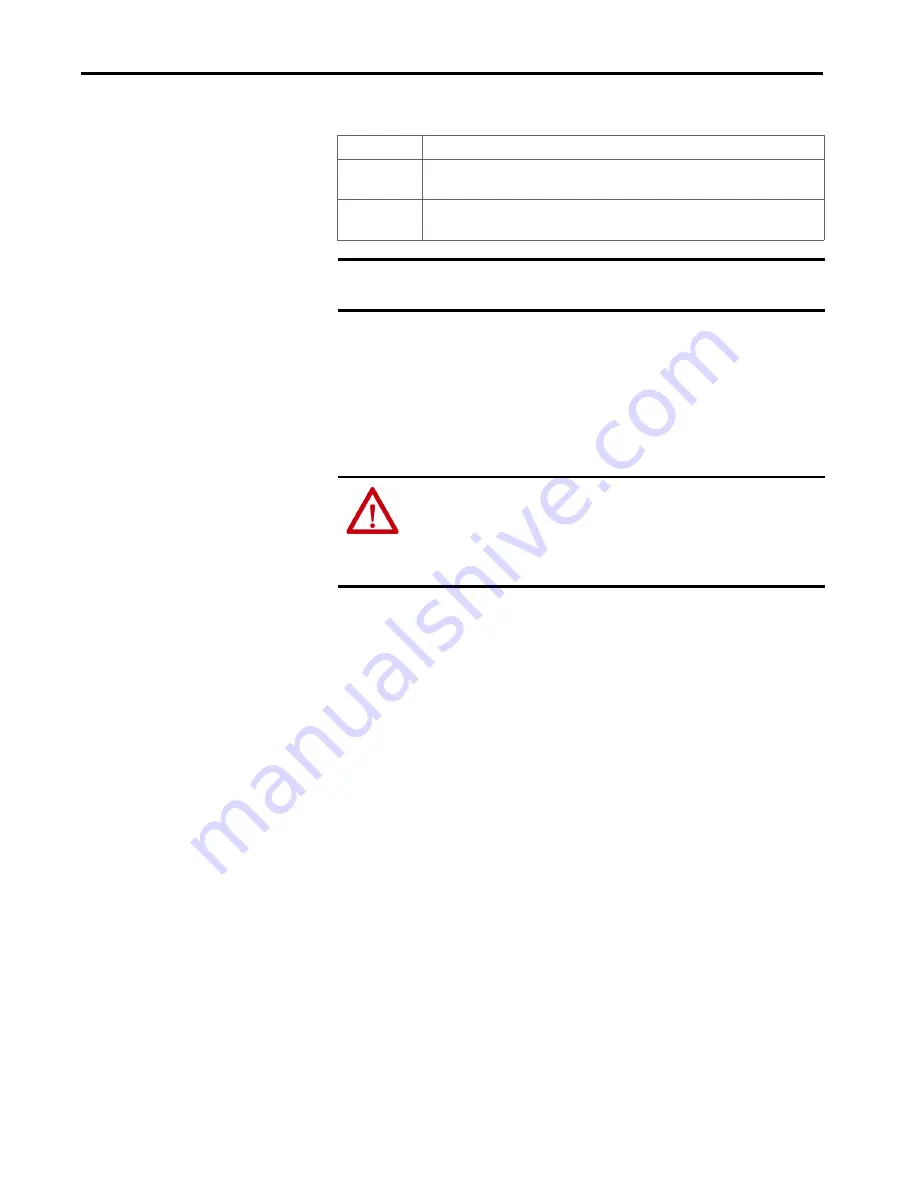
56
Rockwell Automation Publication ICSTT-RM446N-EN-P - April 2018
Chapter 3
AADvance System Architectures
Table 14 - Auxiliary Modules
Internal Diagnostics
The AADvance controller embodies sophisticated internal diagnostic systems
to identify faults that develop during operation and raise appropriate alarm and
status indications. The diagnostic systems run automatically and check for
system faults associated with the controller (processor and I/O modules), and
field faults associated with field I/O circuits.
The diagnostic systems report a serious problem immediately, but filter non-
essential safe failures to avoid spurious alarms. The diagnostic systems monitor
such non-essential items periodically, and need a number of occurrences of a
potential fault before reporting it as a problem.
The internal diagnostics detect and reveal both safe and dangerous failures. A
dual module arrangement, for example, diagnostics can address dangerous
failures and help redress the balance between failure to respond and spurious
responses. A dual system could therefore be 1oo2D reverting to 1oo1D on the
first detected fault and reverting to fail-safe when both modules have a fault. A
whole self-test cycle completes every 24 hours.
Modules
Conditions
Processor Base
T9100
Safety-related and can be used for safety critical applications in Fault tolerant/High demand SIL
2 applications with 2 modules fitted or SIL 3 applications with 2 or 3 modules fitted.
I/O Base
T9300 (3-way)
Safety-related and can be used for safety critical applications in SIL 3.
NOTE
Revisions of modules are subject to change. A list of the released versions
can be obtained from Rockwell Automation.
WARNING:
Safety wiring principles shall be employed for field loops if it is
necessary for the user to guard against short circuit faults between I/O
channels (e.g. to comply with NFPA 72 requirements). The AADvance
controller internal diagnostics do not detect external short circuits between
channels.