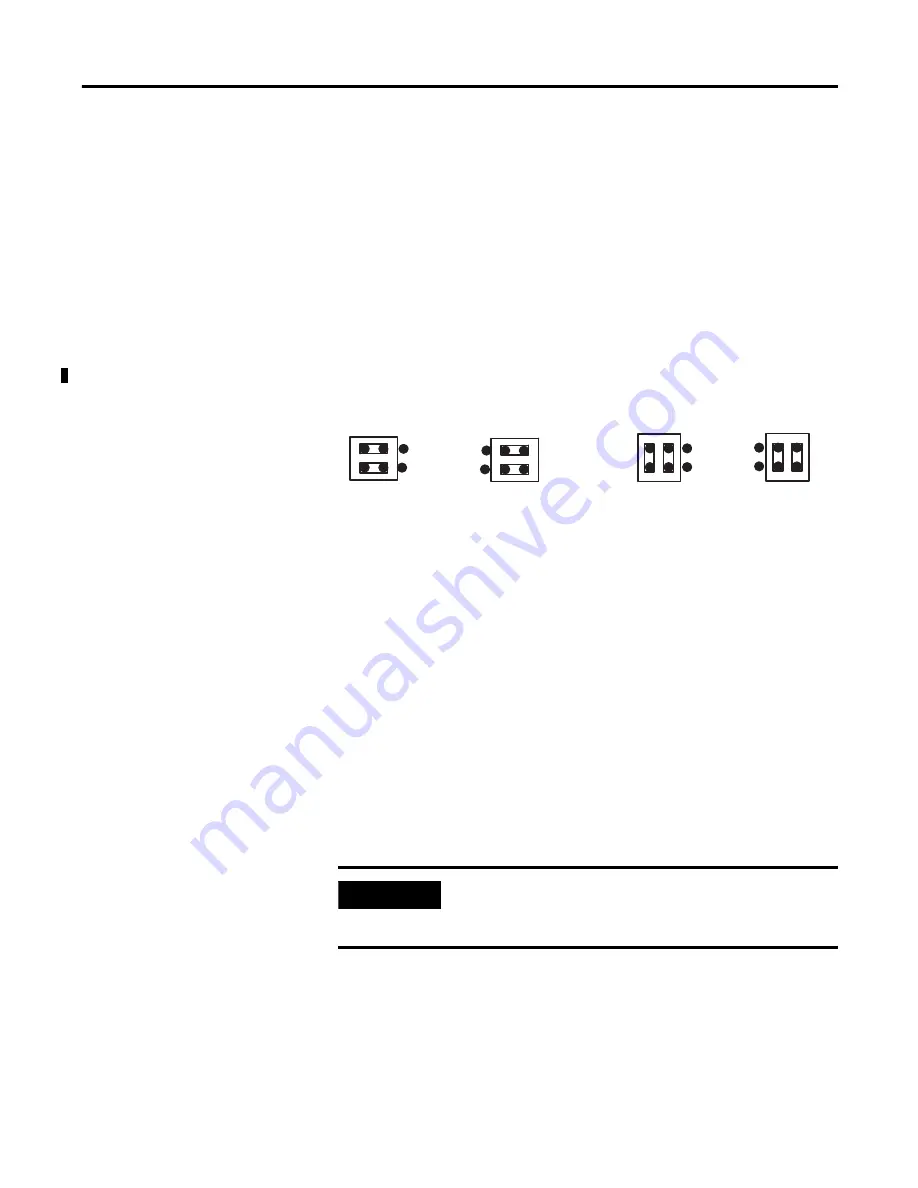
Publication 1747-UM005B-EN-P - March 2006
4-2
Installation and System Configuration
Choose the Module’s
Functionality
Your series B interface module has the ability to function as a series A
interface module. This feature may be important to you if you are
replacing a series A module with a series B module.
Refer to page 4-2 for more information.
The module’s functionality depends on the placement of the JW4
jumper. Horizontal placement of the jumper gives the module
functionality equivalent to a series A interface module, while vertical
placement of the jumper accesses the added functionality of a series B
interface module.
Module Functionality Settings
Add an Interface Module to Your System
If you are not replacing a series A module, you will want to access the
full functionality of the series B module. Therefore, as you work
through the remainder of this manual, follow the instructions for
series B functionality (vertical placement of the JW4 jumper).
Skip the next section and move on to Set the Module’s Mode.
Replace a Series A Interface Module in Your System
Series A Functionality
If you do
not want to alter the existing configuration in your user
program in any way, choose the series A functionality for your new
module. The horizontal placement of JW4 gives the series B module a
Series A Functionality
(mod. config. ID=4209)
Series B Functionality
(mod. config. ID=3509)
Horizontal
Configuration
Mode
Horizontal Run
Mode
Vertical Run
Mode
Vertical
Configuration
Mode
IMPORTANT
Choosing series B functionality requires you to
change the module configuration ID assigned in
your processor.
Summary of Contents for 1747-KE
Page 1: ...DH 485 RS 232C Interface Module Catalog Number 1747 KE User Manual AB Parts ...
Page 4: ...Publication 1747 UM005B EN P March 2006 2 Summary of Changes Notes ...
Page 12: ...Publication 1747 UM005B EN P March 2006 4 Preface ...
Page 26: ...Publication 1747 UM005B EN P March 2006 2 4 Quick Start ...
Page 88: ...Publication 1747 UM005B EN P March 2006 7 4 Interpret the LED Indicators ...
Page 116: ...Publication 1747 UM005B EN P March 2006 8 28 Application Examples ...
Page 120: ...Publication 1747 UM005B EN P March 2006 A 4 Specifications ...
Page 130: ...Publication 1747 UM005B EN P March 2006 C 6 Lithium Battery Replacement Handling and Disposal ...
Page 134: ...Publication 1747 UM005B EN P March 2006 D 4 Interface Module Configuration Worksheets ...
Page 138: ......