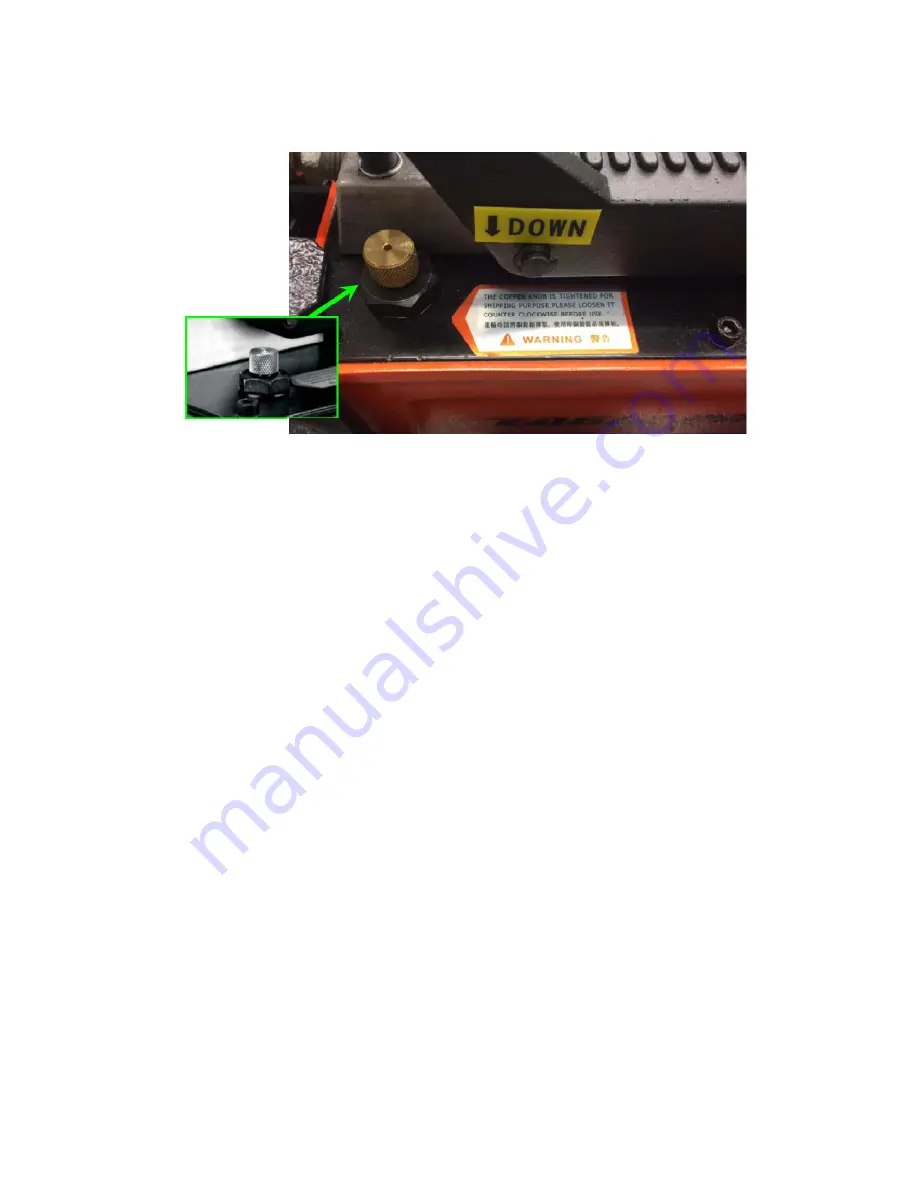
9 of 19
10.
Remove the plug with vent breather on top of reservoir to check the hydraulic oil level and fill
as need, then replace the plug.
11. Loosen metal knob on the pump by turning counterclockwise before use. See Figure 7.
Figure 7- Copper knob on pump
12. Repeat the above process for other Jackbeam.
13. Restore compressed air supply to the lift and check for leaks.
14. Prior to placing vehicle on lift, raise and lower the Jackbeam multiple times without any load
and Do following final checks. See sections “
5.0 Operation Instructions
”
Final Check the followings:
Check proper function of mechanical safety locks
Check for air and hydraulic leaks
Check hydraulic oil level
Lubrication of moving components
All screws, bolts, and pins secured
Surrounding area clean
Operation, maintenance and Safety Manual on site.
AN APPROPRIATE AIR LINE REGULATOR, WATER SEPARATOR AND LUBRICATOR
SHOULD BE INSTALLED ON THE AIR SUPPLY LINE. THE ABSENCE OF THESE ITEMS
WILL VOID THE WARRANTY ON PNEUMATIC COMPONENTS.
5.0 Operating Instructions
Raising the Jackbeam
1. Position the vehicle on the lift and raise the lift to the desired working height following the
operating instructions noted in the lift operating manual. Always ensure that the lift is securely
positioned on the mechanical safety locks prior to raising the vehicle off the runways.