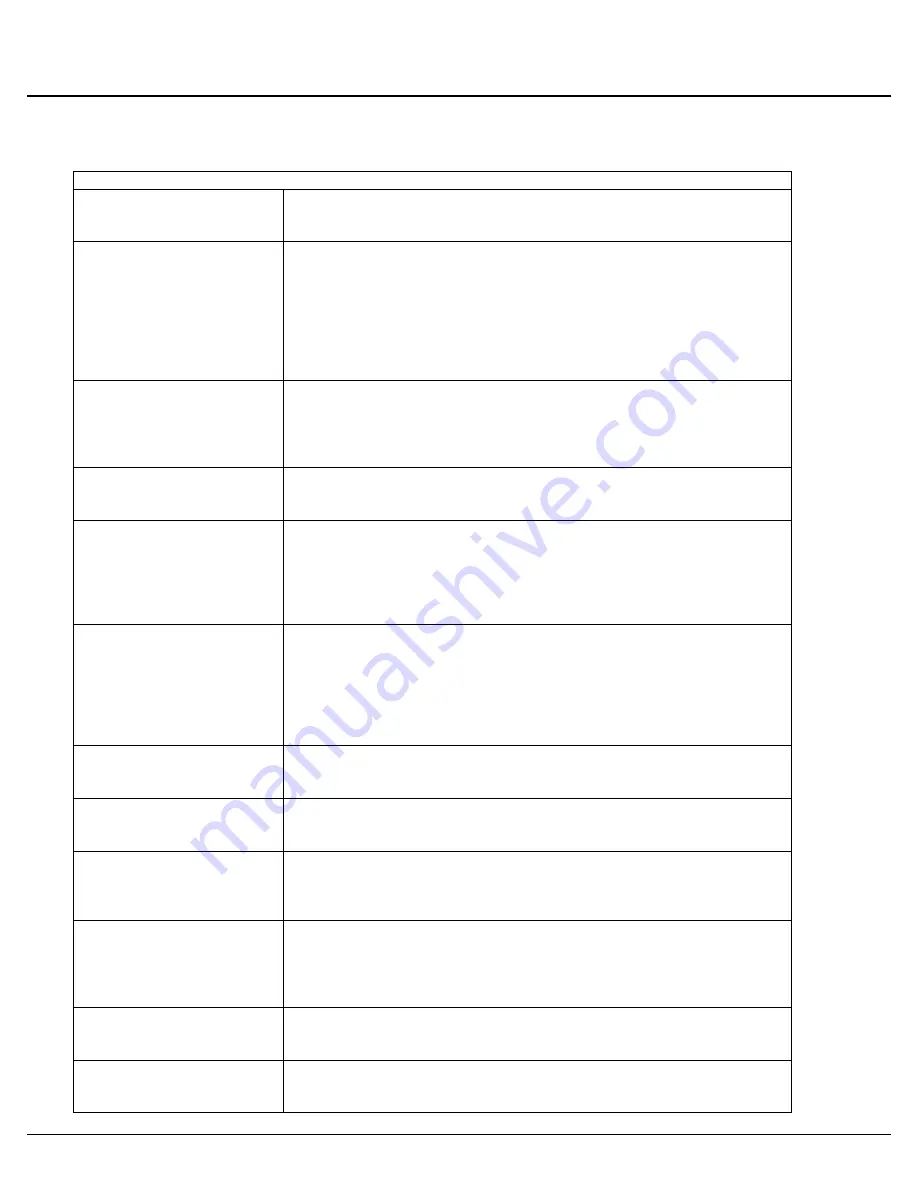
Maintenance
4-18
Algas-SDI Operation and Maintenance Manual
– P/N - 52642
Table 6
– Annual Maintenance Requirements
Annual Maintenance Items
Strainer
Remove the plug and clean the screen. Replace screen if tears or holes
are present (40
– 80 Mesh). If oils or contaminants are present, it may be
necessary to use a cleaner to remove all of the contaminants.
Thermostat
Check thermostat for proper operation per the
Start-up procedure
.
Establish pilot and turn the thermostat dial counterclockwise to high,
burners should cycle on. Turn the dial clockwise to the OFF
” position,
main burner and pilot should both extinguish in a short period of time.
Replace the thermostat if not operating properly (thermostat cannot be
serviced). NOTE: Before replacing the thermostat, be sure the
thermocouple is delivering the proper voltage to the thermostat (see
below).
Thermocouple
Check electrical output of the thermocouple with a multimeter. The
thermocouple output (when hot) should be 13 - 30 mV DC. Lower than
13 mV DC reading indicates the thermocouple should be replaced.
NOTE: Be careful not to over tighten the thermocouple! First, hand
tighten and then turn 1/8
th
turn with wrench.
Pilot Assembly
Inspect pilot flame to ensure flame is
enveloping 3/8” to ½” (9-13 mm) of
the thermocouple tip. Clean pilot orifice. If pilot assembly is corroded or
significantly deteriorated, replace complete pilot assembly.
Main Burner Assembly
Inspect burner tips to ensure each tip has proper flame. For easy access
to clean the burner tips, disconnect burner supply line and remove the
burner from the unit. With compressed air (if possible), blow out main
burner ring prior to cleaning the burner tips. Check orifices and air supply
openings for debris, insects and/or dirt. Clean any plugged or obstructed
orifices.
Pilot Flame Guide / Flame
Spreader Bar
Upon initial installation and during periodic maintenance inspections,
check for corrosion on the ends of the pilot flame guide. If flame
diverter(s)
are corroded more than 1/8” replace flame guide.
Additionally on 80/40H and 120/60H, check flame spreader bar position to
ensure both burners light simultaneously and smoothly. Straighten
spreader bar if it is positioned at an angle or not positioned on top of the
pilot properly.
Liquid Inlet Valve
Use repair kit to replace internal components of the liquid inlet valve. See
detailed
Liquid Inlet Valve Maintenance Instructions
for further
information.
Capacity Control Valve
Use repair kit to replace internal components of the capacity control valve.
See detailed
Capacity Control Valve Maintenance Instructions
for further
information.
Vaporizer Tubing
Inspect all tubing for pitting or flaking - run hands along the underside of
each of the tubes to check for signs of corrosion. Replace tubes if
corroded. Disconnect all tubing and blow tubes free of debris. Re-install
tubing to the vaporizer and check and tighten all fittings.
Relief Valves
Inspect all relief valves on the vaporizer, liquid, and vapor lines for signs
of corrosion and damaged or missing rain caps. Replace rain cap if it is
damaged or missing. Replace relief valves per manufacturer’s
recommended replacement period. Also replace relief valve if it shows
significant corrosion on the outlet or has relieved.
Burner Regulator
Check regulator delivery pressure at the drip leg and at the burner
pressure port to ensure proper pressure is delivered to the thermostat and
burners. See page 1-3 for burner pressure specifications.
Heat Exchanger
1. Check heat exchanger flue for holes or excessive scale.
2. Remove debris, soot build-up and any obstructions from the
outside surface of the heat exchanger between the fins and in the
Summary of Contents for Direct Fired 120/60H
Page 4: ...This page left intentionally blank...
Page 6: ...This page left intentionally blank...
Page 9: ...This page left intentionally blank...
Page 42: ...APPENDIX A TECHNICAL INFORMATION...
Page 43: ...Figure 13 40 40H Vaporizer Replacement Parts 1 2 3 4 5 6 10 8 9 11 12 13 14 15 16 24...
Page 55: ......