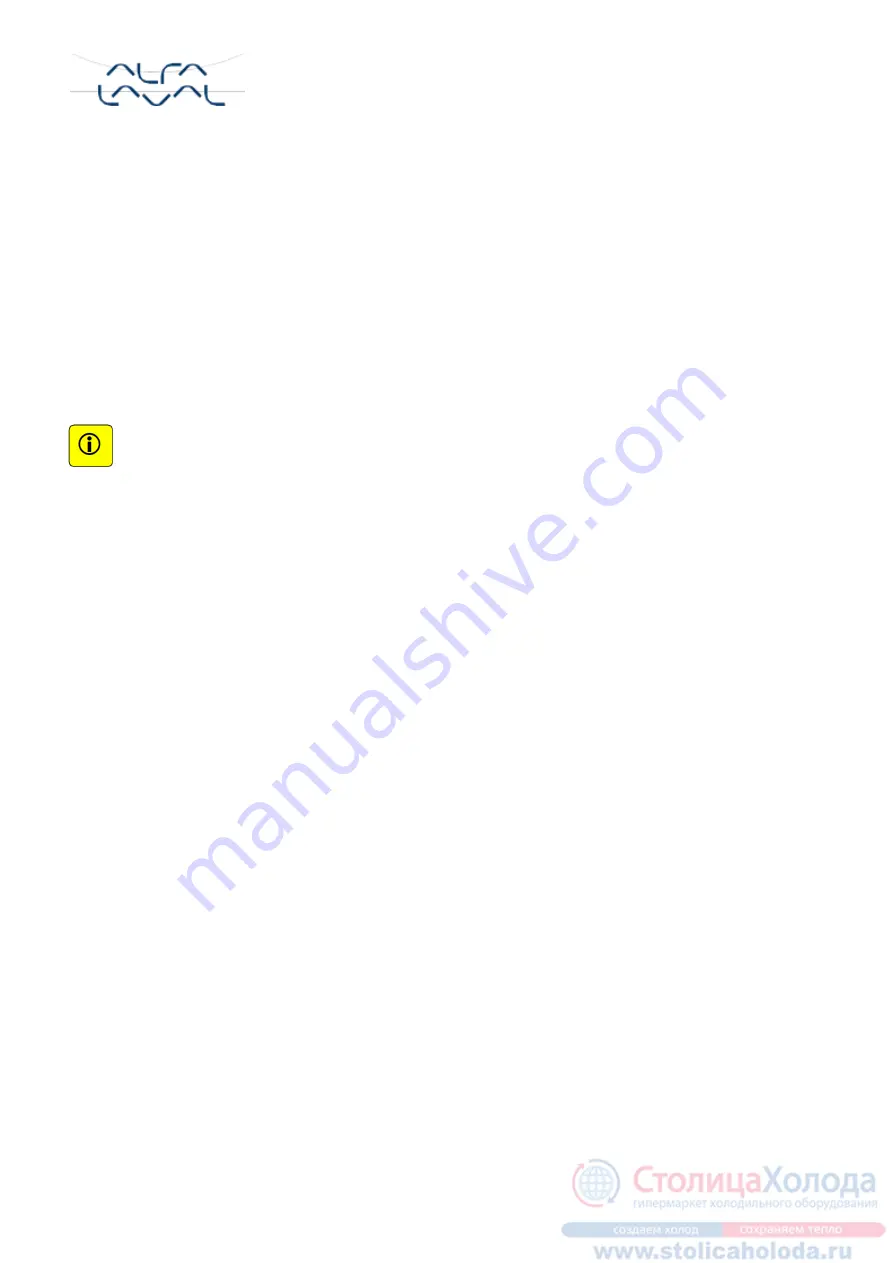
© Alfa Laval
IM100536
Rev 01
4
Piping connections
Direct Expansion units
Pipe sizes must be established according to good engineering design practices. Prior to charging the system with
refrigerant, the entire system must be pressure-tested to ensure there are no leaks, and evacuated to remove
moisture. Piping must be designed and supported independently from the evaporator to minimize the transmission
of vibrations, to permit expansion and contraction, and so as not to subject the evaporator connections to stress
.
Suction pipe
Connect the pipe observing the coil joint diameter. The suction pipe should allow the oil return from the evaporator
toward the compressor by continuous gravity (minimum gradient1cm/mt). If this is not possible, it will be
necessary to create a suction siphon for each coil joint.
To weld two copper pipes, an overlapped welding is suggested, for the double purpose of guaranteeing its
strength and reducing the risk of breakages in the welded area, generated by induced vibrations. The external
piping should be well aligned.
Do NOT bend the connections!
Bulb position in the suction pipe
The position of the bulb of the thermostatic valve varies according to the diameter of the suction pipe, to which it is
securely fixed by means of the corresponding metallic clamps, which transmit the thermal flow from the pipe to the
bulb. It is advisable to place it in the horizontal section of the suction line, far away from all sources of heat or
thermal masses.
Water connections for Brine units
Vent the system, bleed off all air, and check for water hammer.
Verify the feed solenoid valve or mixing valve function.
Important:
•
The size of the pipe must be in accordance with the IN and OUT connection diameter of the coil.
•
ON-OFF valves must be installed near the unit to permit normal maintenance.
•
Use vibration-damping joints.
•
All threads should be covered with TEFLON to ensure air tightness.
Condensate drain line
The drain line for each unit should be connected to the male gas joint, located in the center of the drip tray and
must be piped to an independent trap to prevent the migration of warm air through the drain lines. The minimum
slope must not be less than 20%. Drain pan connections and any drain lines and traps that are located in freezing
temperatures must be heat traced and insulated to prevent freezing. Heating elements should be continuously
energized. All piping should be adequately supported, independently of the unit so no weight is exerted on the
pan connection.
Defrost System General
The ambient moisture in the cold room and the water vapor coming from the dehydratation of the stored material
condenses and becomes ice when it comes in contact with the coil fins. This restricts the airflow area and,
consequently, decreases the heat exchanging and the performance of the unit. To avoid this problem, the coil
must be periodically defrosted, following one of the procedures described below. Setting of the defrost is set by
the operator in order to suit specific site requirements and complete cleaning the unit surface from ice.
End defrost probe
This must be located on the evaporator in such a way that it is not in contact with hot air, which could affect its
correct operation. The defrost cycle ends when the probe measures a temperature of the finned coil that
corresponds to the set value. The defrost cycle is stopped and cooling restarts, while the fans start again only
after a suitable dripping time.
Summary of Contents for Optigo CC
Page 21: ... Alfa Laval IM100536 Rev 01 20 ...
Page 29: ... Alfa Laval IM100536 Rev 01 28 ...
Page 37: ... Alfa Laval IM100536 Rev 01 36 ...
Page 52: ... Alfa Laval IM100536 Rev 01 51 DELIVERY ...
Page 54: ... Alfa Laval IM100536 Rev 01 53 INSTALLATION CC400 CC500 CC250 CC350 CC400 CC500 ...
Page 55: ... Alfa Laval IM100536 Rev 01 54 INSTALLATION ...
Page 56: ... Alfa Laval IM100536 Rev 01 55 LAYOUT ...
Page 57: ... Alfa Laval IM100536 Rev 01 56 LAYOUT Loading Unloading PIPING CONNECTION IN IN ...
Page 58: ... Alfa Laval IM100536 Rev 01 57 PIPINGCONNECTION DEFROST SYSTEM ...
Page 59: ... Alfa Laval IM100536 Rev 01 58 AIR DEFROST ELECTRIC DEFROST ...
Page 60: ... Alfa Laval IM100536 Rev 01 59 HOT GAS DEFROST ...
Page 61: ... Alfa Laval IM100536 Rev 01 60 FAN DEFROST STARTUP AFTER DEFROST ...
Page 62: ... Alfa Laval IM100536 Rev 01 61 ELECTRIC INSTALLATION ...
Page 63: ... Alfa Laval IM100536 Rev 01 62 ELECTRIC INSTALLATION ...
Page 64: ... Alfa Laval IM100536 Rev 01 63 ELECTRIC INSTALLATION ...
Page 67: ... Alfa Laval IM100536 Rev 01 66 ELECTRIC INSTALLATION ...
Page 68: ... Alfa Laval IM100536 Rev 01 67 MAINTENANCE Cleaning Tools for Maintenance ...
Page 69: ... Alfa Laval IM100536 Rev 01 68 MAINTENANCE Replacing electric resistors Coil ...
Page 70: ... Alfa Laval IM100536 Rev 01 69 MAINTENANCE Replacing electric resistors Driptray ...
Page 71: ... Alfa Laval IM100536 Rev 01 70 MAINTENANCE Replacing fan motor ...