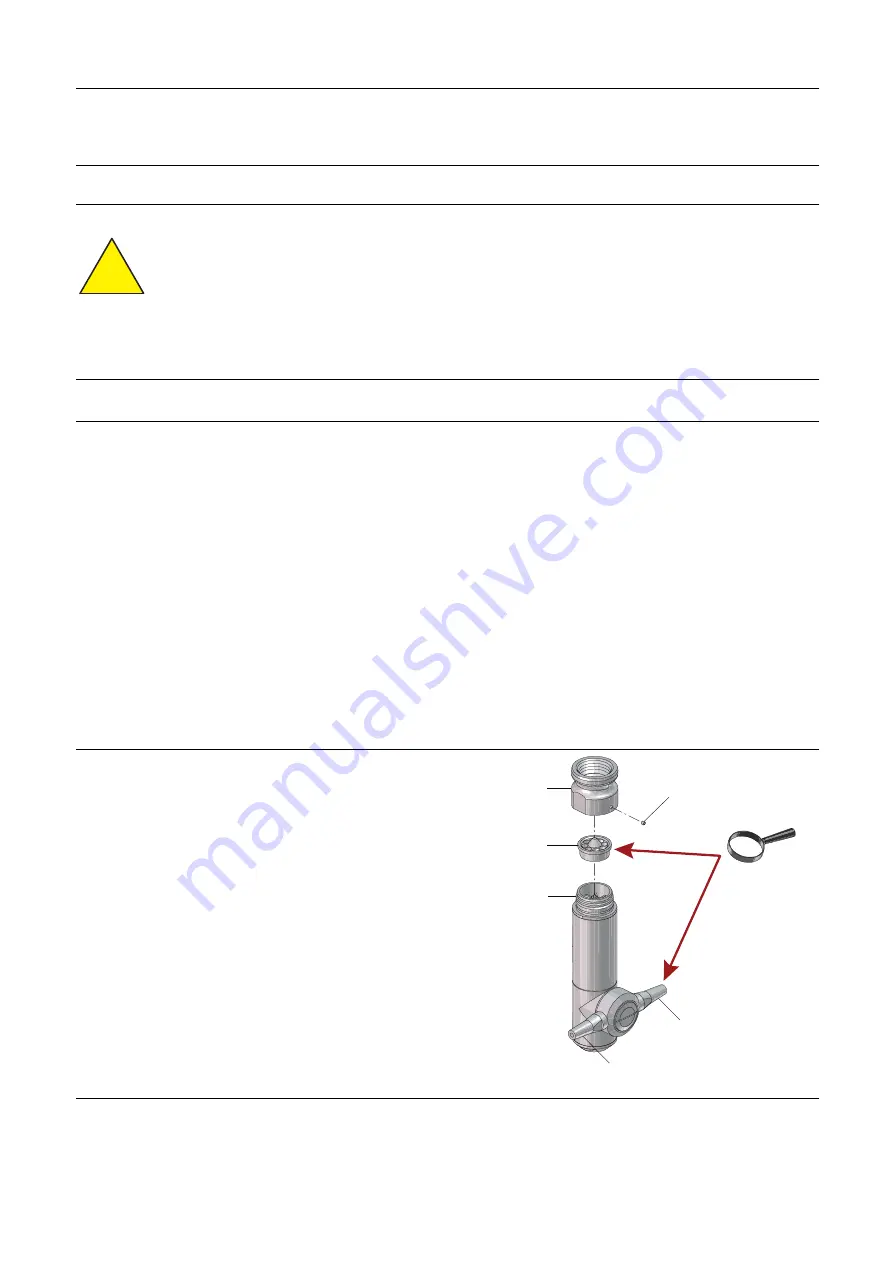
6 Maintenance
Maintain the tank cleaning machine with care.
Read the instructions carefully and pay special attention to the warnings!
Always keep minor spare parts kit in stock.
6.1
General maintenance
Step 1
!
Always read the technical data thoroughly, see section 7 Technical data.
Recommended spare parts: Order service kits from the service kits list, see section 8 Parts list and service kits
Ordering spare parts: Contact your local Alfa Laval sales company.
6.2
General dismantling set up
NOTE
A rigorously implemented preventative maintenance program will significantly reduce repair costs over the life of the Alfa Laval
GJ.The foundation of such a program is regularly scheduled inspections to discover and replace worn or damaged parts before
they can cause the failure of other, more costly, components. The inspection intervals required will depend on the severity of the
application, but a complete internal inspection at 100 hours of operation is recommended initially.
Step 1
STORAGE
The Alfa Laval GJ should be washed out with clean water after
each use to remove any foreign material or soft substances left in
the machine that may harden during storage and cause the Alfa
Laval GJ to seize or lock up. A clean water rinse through the Alfa
Laval GJ will also wash out any residues of chemical cleaners or
recirculated wash water that could adversely affect the seals and
O-rings during prolonged contact in storage. The best position to
store the Alfa Laval GJ is to stand it up with the inlet connection
facing down.
Step 2
EXTERNAL INSPECTION INTERVALS
Before every shift, the stator (12) and the nozzles (16) should be
inspected for debris. Examine the stator (12) by loosening the
collar set screw (30), while holding on the flats of the cap (6) and
remove the main section of the machine from the collar (11). Look
into each nozzle for signs of debris or build-up
12
30
11
4125-0010
16
16
6
21
Summary of Contents for GJ PF
Page 2: ......
Page 43: ... 43 ...