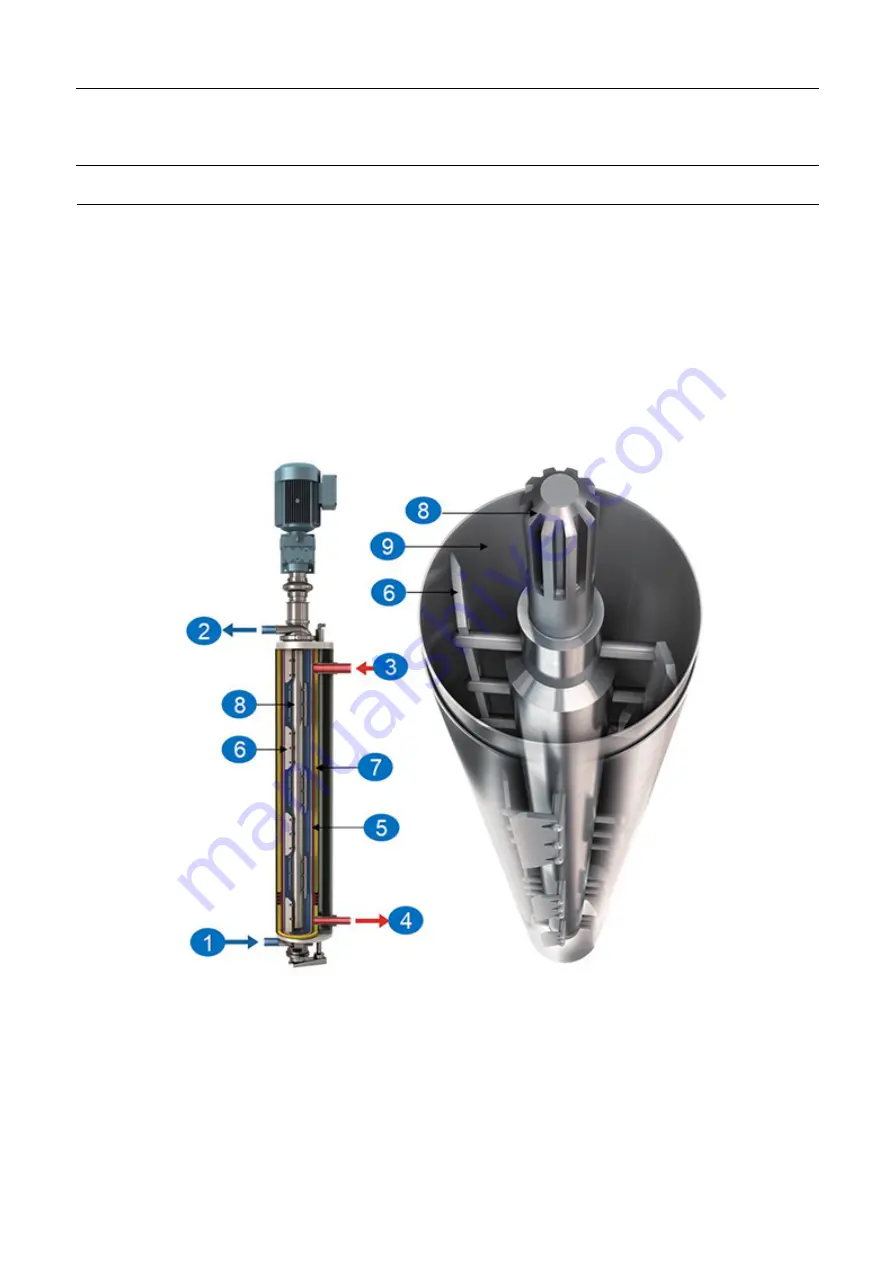
4 Portfolio Description & Equipment Limitations
4.1
General Description
NOTE: This section describes the Contherm
™
in a general sense and information in this section may or may not be
applicable to your order. Please refer to Chapter 1 for specific information corresponding to your Contherm
™
order.
Working Principle and Use Limits
Product enters the (7) insulated Contherm
™
cylinder through the lower product head (1) and flows upwards through the cylinder.
At the same time, the heating/cooling media (3) enters the Contherm
™
and travels in a counter-current flow through the
narrow annular channel (5) before exiting (4).
Rotating blades (6) attached to the Contherm
™
rotor (8) continuously remove product from the cylinder wall (9) to ensure
uniform transfer of heat from the media to the product. An optional coil in the annulus (5) increases media velocity, adding to
the heat transfer efficiency
Product exits the cylinder through the upper tangential port (2). Product flow and rotor speed can be varied to suit the properties
of the product flowing through the cylinder.
Figure 4.1 Contherm
™
General Description
Tailored to specific needs
With a wide selection of components, now also including the low shear rotor for large particulates, numerous Contherm
™
configurations are available.
Trained, knowledgeable Alfa Laval staff can customize each Contherm
™
unit by selecting the appropriate materials, features
and options to meet each customer’s exact requirements.
13
Summary of Contents for Contherm 6X11
Page 2: ......
Page 66: ...8 Inspection Maintenance Figure 8 2 Component List Figure 8 2 66...
Page 88: ...8 Inspection Maintenance Figure 8 13 Upper Bearings Direct Coupled Electric Drive Motor 88...
Page 99: ...8 Inspection Maintenance Figure 8 18B CONTHERM Hydraulic Lift Assembly With Hold Down 99...
Page 117: ...10 Appendix A Additional Installation Drawings 117...
Page 123: ...123...