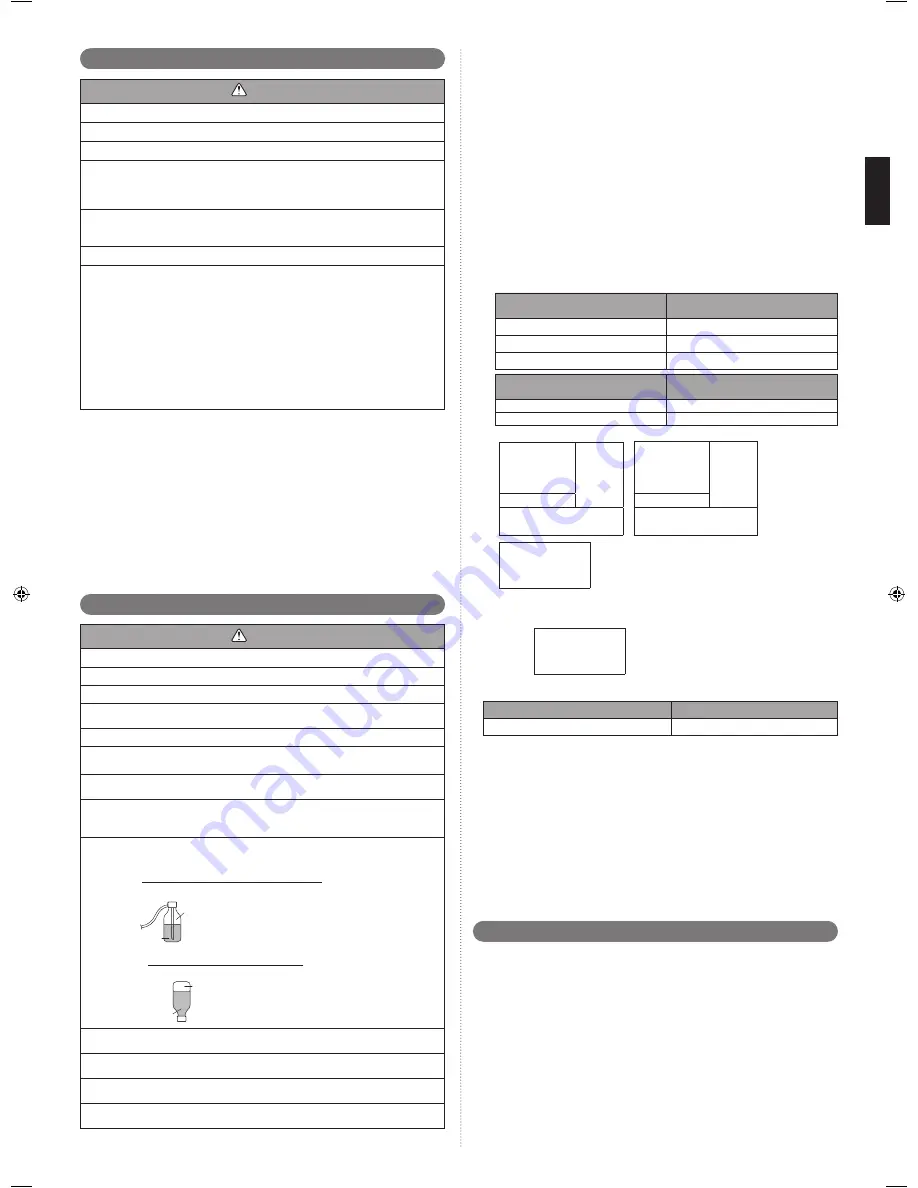
En-18
8. 2. Vacuum process
CAUTION
Do not turn on the power unless all operations are complete.
If the system is not evacuated suf
fi
ciently, its performance will drop.
Be sure to evacuate the refrigerant system using a vacuum pump.
The refrigerant pressure may sometimes not rise when a closed valve is opened after
the system is evacuated using a vacuum pump. This is caused by the closure of the
refrigerant system of the outdoor unit by the electronic expansion valve. This will not
affect the operation of the unit.
Use a clean gauge manifold and charging hose that were designed speci
fi
cally for
use with R410A. Using the same vacuum equipment for different refrigerants may
damage the vacuum pump or the unit.
Do not purge the air with refrigerants, but use a vacuum pump to evacuate the system.
• If moisture might enter the piping, follow below. (i.e., if doing work during the rainy
season, if the actual work takes long enough that condensation may form on the
inside of the pipes, if rain might enter the pipes during work, etc.)
• After operating the vacuum pump for 2 hours, pressurize to 0.05 MPa (i.e., vacuum
breakdown) with nitrogen gas, then depressurize down to -100.7kPa (-755mmHg)
for an hour using the vacuum pump (vacuum process).
• If the pressure does not reach -100.7kPa (-755mmHg) even after depressurizing
for at least 2 hours, repeat the vacuum breakdown - vacuum process.
After vacuum process, maintain the vacuum for an hour and make sure the pressure
does not rise by monitoring with a vacuum gauge.
Evacuation procedure
(1) Remove the blank caps of the gas pipe and liquid pipe and check that the valves
are closed.
(2) Remove the charging port cap.
(3) Connect a vacuum pump and a pressure gauge to a charging hose and connect it
to the charging port.
(4) Activate the vacuum pump and vacuum the indoor unit and connection piping until
the pressure gauge becomes -100.7kPa (-755mmHg).
Evacuate from both the gas pipe and the liquid pipe.
(5) Continue
evacuating
the
system
for
1 hour after the pressure gauge reads
-100.7kPa (-755mmHg).
(6) Remove
the
charging
hose
and
reinstall the charging port cap.
8. 3. Additional charging
CAUTION
Do not turn on the power unless all operations are complete.
After evacuating the system, add refrigerant.
Do not charge the system with a refrigerant other than R410A.
Always keep to the limit on the total amount of refrigerant. Exceeding the limit on the
total amount of refrigerant will lead to malfunction during charging of refrigerant.
Do not reuse recovered refrigerant.
Use an electronic scale to measure the charging amount of refrigerant.
Adding more refrigerant than the speci
fi
ed amount will cause a malfunction.
Charge refrigerant using the liquid pipe.
Adding refrigerant through the gas pipe will cause a malfunction.
Add refrigerant by charging the system with the refrigerant in the liquid state. If the
refrigerant cylinder is equipped with a siphon, it is not necessary to place the cylinder
upright.
Check if the steel cylinder has a siphon installed or not before
fi
lling. (There is an
indication “with siphon for
fi
lling liquid” on the steel cylinder.)
Filling method for cylinder with siphon
Set the cylinder vertical and
fi
ll with the
liquid.
(Liquid can be
fi
lled without turning bot-
tom up with the siphon inside.)
Liquid
Gas
R410A
Filling method for other cylinders
Turn bottom up and
fi
ll with liquid.
(Be careful to avoid turning over the
cylinder.)
Liquid
Gas
R410A
Be sure to use the special tools for R410A for pressure resistance and to avoid mixing
of impure substances.
If the units are further apart than the maximum pipe length, correct operation can not
be guaranteed.
Make sure to back closing valve after refrigerant charging. Otherwise, the compressor
may fail.
Minimize refrigerant release to the air. Excessive release is prohibited under the
Freon Collection and Destruction Law.
8. 3. 1. Procedure for charging the system with refrigerant
(1) Remove
the
charging
port
cap from the liquid pipe.
(2) Attach a charging hose to the refrigerant cylinder, and connect it to the charging port.
(3) Add
refrigerant
by
calculating
the
additional refrigerant volume in accordance with
the calculation formula indicated below.
(4) Remove
the
charging
hose
and install the charging port cap.
(5) Remove the blank caps (gas pipe and liquid pipe) and open the valves.
(6) Close
the
blank
caps.
(7) After adding refrigerant, indicate the added charging volume on the unit.
* Tighten the blank caps and charging port caps to the torque values speci
fi
ed in the
Table A.
To open and close the valves,
Use an M4 hexagon wrench.
8. 3. 2. Checking total amount of refrigerant and calculating
the amount of refrigerant charge to be added
• The amount of refrigerant charge to be added is the total value of the basic refriger-
ant charge amount and the value calculated from the length of the liquid pipe.
• Round up the value to 2 decimal places.
Model
B
Factory charged amount (kg)
AJY040LCLAH
4.0
AJY045LCLAH
4.0
AJY054LCLAH
4.0
Diameter of liquid pipe (mm)
a
Additional amount for pipe length (kg/m)
Ø6.35
0.021
Ø9.52
0.058
(1) Calculation of additional amount for pipe length
A =
Total length of
ø9.52 mm liquid
pipe
a
× 0.058
(kg/m)
m
kg
+
Total length of
ø6.35 mm liquid
pipe
a
× 0.021
(kg/m)
m
kg
=
Total
kg
(Round up A to 2 decimal place)
(2) Calculation
of
total
refrigerant
amount
C = A + B =
kg
(B : Factory charged amount)
Note: Check the total refrigerant amount under the following conditions
Condition
Computational formula
Total amount of refrigerant
C
≤
6.83kg
<Calculation>
Outdoor unit: AJY054LCLAH
(1) Calculation of additional amount for outdoor unit
If liquid pipe piping length is the following
Φ
9.52 : 20m ,
Φ
6.35 : 10m
Additional charge volume:
A = 20 (m) × 0.058 (kg/m) + 10 (m) × 0.021 (kg/m)
=
1.37
kg
(2) Check the total amount of refrigerant
C = A + B = 1.37 kg + 4.0 kg = 5.37 kg
≤
6.83 kg
→
No problem if the above condition is satis
fi
ed
8. 4. Installing insulation
• Install insulation material after conducting the “8.1 Sealing Test”.
• To
prevent
condensation
and
water
droplets,
install insulation material on the refriger-
ant pipe.
• Refer to the table to determine the thickness of the insulation material.
• If the outdoor unit is installed at a level that is higher than the indoor unit, the water that
has condensed in the 3-way valve of the outdoor unit could travel to the indoor unit.
Therefore, use putty in the space between the pipe and the insulation to prevent the
entry of water.
Table. Selection of insulation
(for using an insulation material with equal heat transmission rate or below 0.040W/(m·k))
9380545057_IM.indb 18
9380545057_IM.indb 18
2014/9/15 11:27:06
2014/9/15 11:27:06