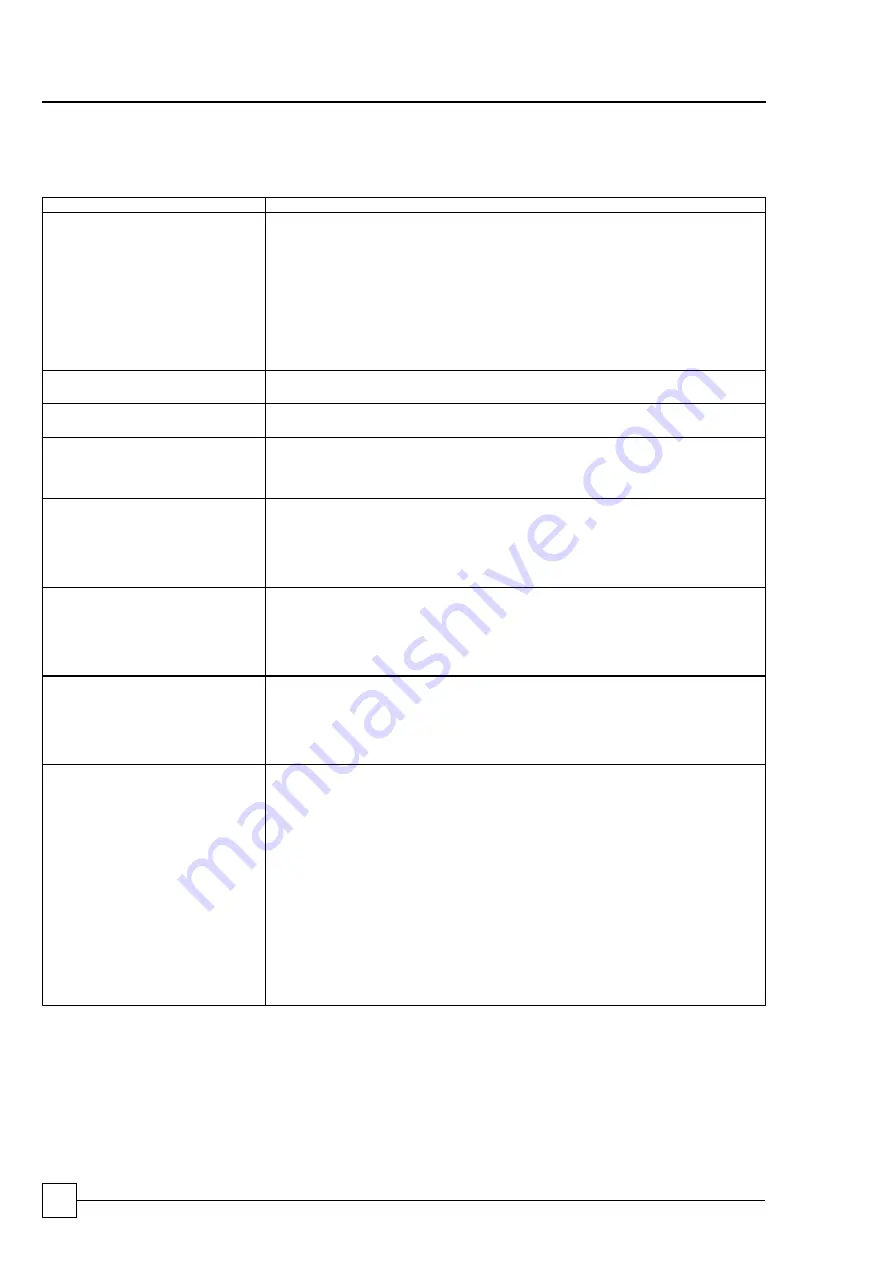
ULTIMA FREECOOL
Chillers
Chillers
20
Installation & Maintenance Manual : 903-125 IM E 05/04/A
Installation Data
ELECTRICAL DATA
Model
UFC200D-8 UFC225D-8
UFC250D-8
UFC275D-8 UFC300D-8
Unit Data
(1)
Nominal Run Amps
(2) A
141
154
167
174
183
Maximum Start Amps
A
289
335
348
356
336
Permanent Supply
VAC
230V 1PH 50Hz
Mains Supply
VAC
400V 3PH 50Hz
Rec Permanent Fuse Size
A
16
16
16
16
16
Rec Mains Fuse Size
A
200
200
250
250
250
Max Permanent Incoming Cable
Size
mm² 4mm²
Terminal
Max Mains Incoming Cable Size mm²
Direct to Bus Bar
Control Circuit
VAC
24V / 230VAC
Evaporator
Trace Heater Rating
W
200
200
200
200
250
External Trace Heating
Available (fitted by others)
W
500
500
500
500
500
Condenser Fan - Per Fan
Full Load Amps
A
2.60
2.60
2.60
2.60
2.60
Locked Rotor Amps
A
15.00
15.00
15.00
15.00
15.00
Motor
Rating
kW
1.70 1.70
1.70
1.70 1.70
Compressor - Per Compressor
Motor Rating
kW
33 + 33
41 + 33
41 + 41
48 + 41
48 + 48
Nominal Run Amps
(2) A
60 + 60
73 + 60
73 + 73
81 + 73
81 + 81
Crankcase Heater Rating
W
150
150
150
150
150
Start Amps
(3)
208 + 208
254 + 208
254 + 254
234 + 254
234 + 234
Type Of Start
Star / Delta
QUIET DQ
UFC200DQ-8
UFC225DQ-8
UFC250DQ-8
UFC275DQ-8
UFC300DQ-10
All data as above except:
Condenser Fan - Per Fan
Full Load Amps
A
1.75
1.75
1.75
1.75
1.75
Locked Rotor Amps
A
6.20
6.20
6.20
6.20
6.20
Motor
Rating
kW
0.98 0.98
0.98
0.98 0.98
SUPER QUIET DSQ
UFC200DSQ-8
UFC225DSQ-8
UFC250DSQ-8 UFC275DSQ-10
UFC300DSQ-10
All data as above except:
Condenser Fan - Per Fan
Full Load Amps
A
1.15
1.15
1.15
1.15
1.15
Locked Rotor Amps
A
2.10
2.10
2.10
2.10
2.10
Motor
Rating
kW
0.70 0.70
0.70
0.70 0.70
OPTIONAL EXTRAS -
Fitted to standard D models - for data on DQ & DSQ please refer to Airedale.
Power Factor Correction
Nominal Run Amps
(2) A
129
140
151
158
165
Maximum Start Amps
(3) A
289
335
348
356
336
Recommended Mains
Fuse
A
160 200
200
250 250
Compressor Nominal
Run Amps - Per
Compressor
A
54 + 54
65 + 54
65 + 65
72 + 65
72 + 72
Closed Transition
Nominal Run Amps
(2) A
141
154
167
174
183
Maximum Start Amps
A
289
335
348
356
336
Recommended Mains
Fuse
A
200 200
250
250 250
Compressor Nominal
Run Amps - Per
Compressor
A
60 + 60
73 + 60
73 + 73
81 + 73
81 + 81
(1)
Refers to standard speed fans.
(2)
Based at 12/7°C water and 30°C ambient
(3)
Starting amps refers to the Star connection only.