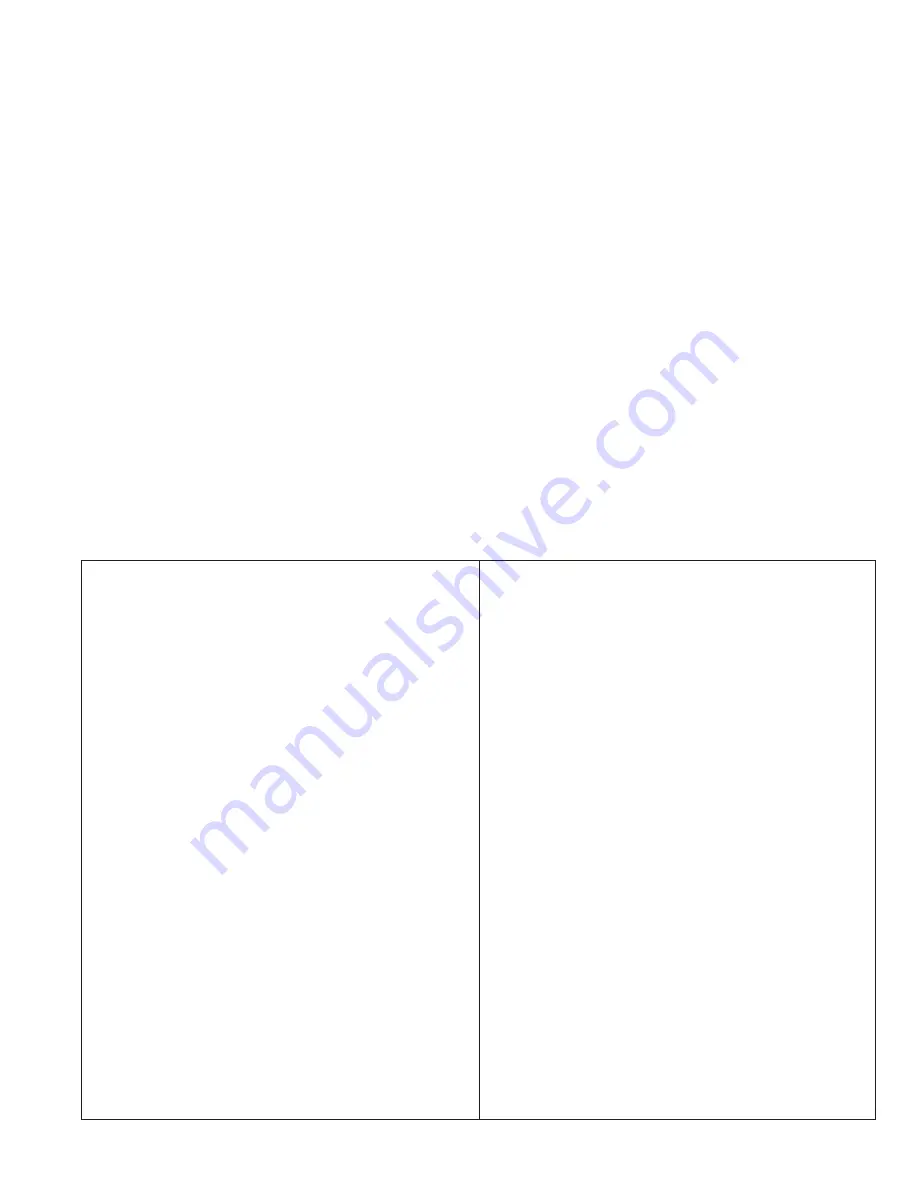
AIR 1-550.30
15
SERVICE / TROUBLESHOOTING
Fails to Maintain Temperature
1. Undersized unit heater, boiler, pump or piping.
2. Unit heater operating at low speed when sized for high speed.
3. Unit heater mounted too high — heated air not delivered to floor.
4. Thermostat — improper location or setting, or not functioning.
5. Dirty or clogged coil.
Unit Blows Cold Air
1. Manual shut-off valve closed.
2. Insufficient steam pressure of lack of hot water.
3. Aquastat not functioning.
4. Improper venting.
5. Steam trap not functioning.
6. Drip leg too short (steam system).
7. Return line plugged (steam system).
8. Pump undersized or not operating (hot water system).
Does Not Operate When Heat Needed
1. Defective motor or electrical connections.
2. Thermostat, aquastat or pressure limit control not functioning.
Fails to Deliver Heat to Floor
1. Units mounted too high.
2. Operating on low speed.
3. Final air temperature too high.
4. Louvers not adjusted properly.
5. Wrong type of diffuser (on verticals).
6. Undersized unit heater (insufficient air delivery).
7. Wrong type of unit (may require vertical delivery).
8. Cross ventilation or drafts.
9. Obstructions to air flow.
Noisy Unit
1. Loose bolts or screws.
2. Fan blade bent, out of balance.
3. Dirt accumulation on fan blades.
4. Fan hub or blade rivets loose.
5. Motor shaft bearing worn.
6. Motor mounting bent, fan not positioned properly in venturi.
7. Conduit too rigid, transmits vibration noise.
8. BX cable touching unit heater, chatters as casing vibrates.
Employees Complain of Hot Blast
1. Air stream aimed directly at employees.
2. Louvers not adjusted properly.
3. Wrong type of diffuser (on verticals).
4. Excessive final air temperature.
Unit Operates Too Long
1. Thermostat installed on cold wall or other improper location.
2. Aquastat or pressure limit control not functioning properly.
3. Unit is undersized.
Frequent Motor Failure
1. Voltage fluctuations too high or too low.
2. Excessive or insufficient lubrication.
3. Wiring to motor undersized.
4. Improper electrical connections.
5. Motor operating in too high air temperature.
6. Restricted air flow due to clogged coil or closed louvers.
7. Fan out of balance.
8. Unbalanced voltage on 3
φ
power.
Coil Failure/Unit Leaks
1. Severe internal corrosion from feedwater.
2. Type of boiler treatment.
3. Entrained air causing water hammer.
4. Continuous operation above 150 PSI (375°F)(steam systems).
5. Loose connection.
Table 15.1 - Troubleshooting
Replacement Parts
When requesting parts please contact your local representative.
Please have full model and serial number available. See
Figure 15.1.
2. For thorough cleaning of coil, remove motor and fan and
spray a mild alkaline cleaning solution over the coil. After a
few minutes, follow by a hot water rinse. (A steam gun can be
used for spraying cleaning solution and hot water.)
3. Coils subjected to corrosive fumes should be checked and
cleaned frequently.
4. Provide controlled water treatment — don’t use excess of
boiler compounds. Contact your boiler compound supplier for
proper usage or the services of a water treatment laboratory.
5. Periodic internal flushing of the coils is recommended in
areas where water supply is suspected of causing scale. Use
an alkaline-chelant solution and introduce it at the main pump
of the hydronic system. Flush thoroughly.
WARNING:
USING INORGANIC OR MINERAL ACIDS SUCH
AS MURIATIC (HYDROCHLORIC) ACID, EVEN THOUGH
INHIBITED, MAY LEAD TO SEVERE DAMAGE, INCLUDING
CORROSION AND LEAKAGE.
6. De-aerate boiler feed-water (particularly if large amount of
new water is used).
7. Insure rapid continuous and adequate condensate drainage
by properly sized and installed traps and piping. Check traps
for sticking. Clean strainers ahead of traps. (When traps
don’t work, condensate accumulates in unit heater coil; water
hammer results.)
8. Adequately vent each unit.
9. Use low pressure steam when possible.
Casings
1.
Periodic cleaning of casings is recommended to remove
dirt, grease and corrosive substances that may injure finish.
Rusted or corroded spots should be cleaned and repainted.
2.
Tighten fan guard and motor bracket. Check fan for proper
clearance, free rotation and firm connection to shaft.
When servicing is complete, tag unit to indicate date of
inspection, lubrication and cleaning.