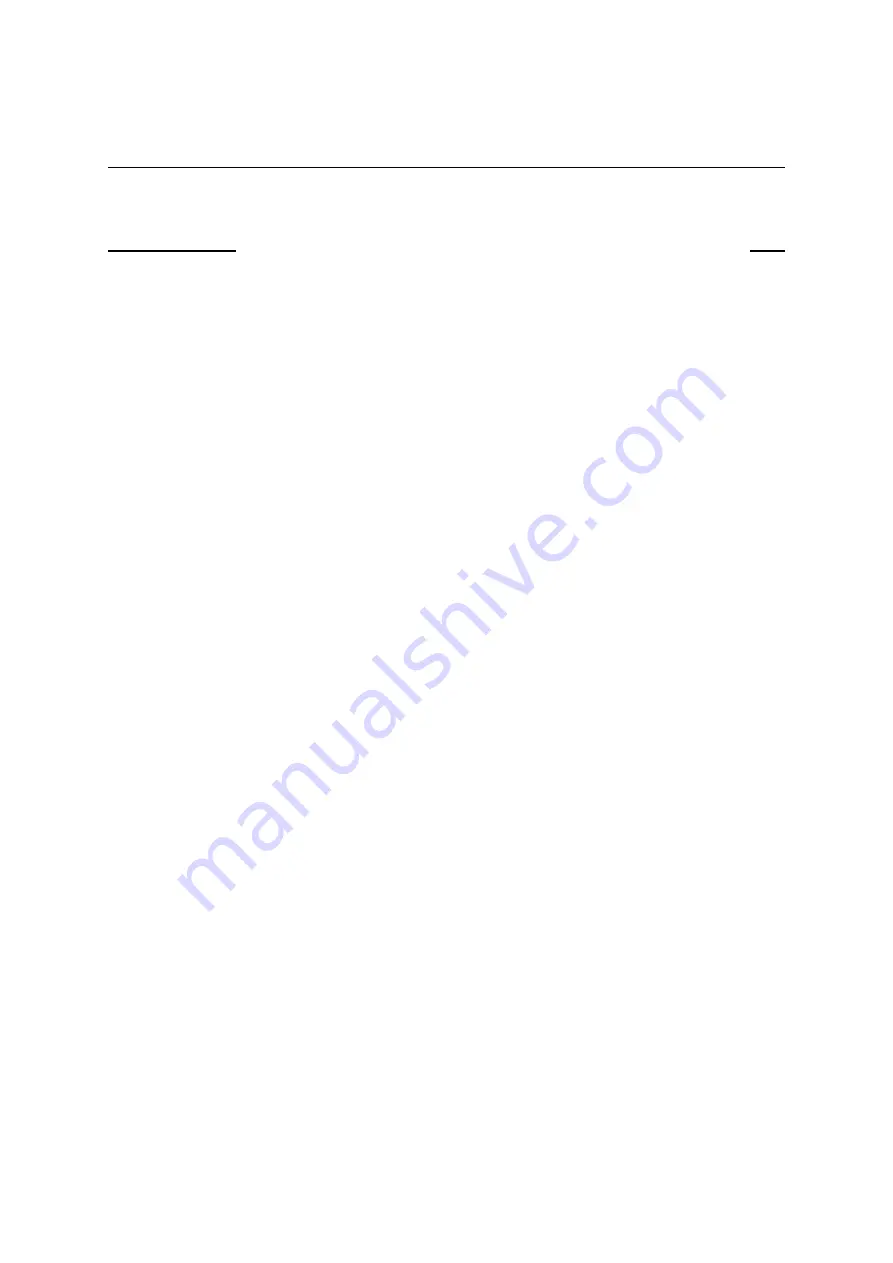
USER MANUAL
VACUUM BLASTING MACHINE 1070 PNE
AB
Revision 1 January 2012
page 0.0
Table of contents
page
1.
Introduction
1.1
2.
Responsibilities of owner and personnel
2.1
3.
Safety
3.1
3.1
Safety precautions
3.1
3.2
Safety provisions
3.4
3.3
Warning/ caution Information
3.5
4.
Technical data
4.1
5.
Parts list
5.1
6.
Transport
6.1
7.
Machine function
7.1
8.
Setting up for operation
8.1
8.1
Installation instructions
8.1
8.2
Operation instructions
8.2
8.3
Adjustment
8.2
8.3.1 Setting the pressure
8.2
8.3.2 Adjustment of the abrasive control valve
8.3
9.
Operation of the machine
9.1
9.1
Inspection procedure before starting up
9.1
9.2
Operation instructions
9.1
9.3
Taking the machine out of operation
9.3
10.
Maintenance
10.1
11.
Trouble shooting
11.1
12.
Parts
12.1
13.
Pneumatic diagram
13.1
Summary of Contents for 1070 PNE
Page 1: ...OPERATOR S MANUAL AIRBLAST 1070 PNE VACUUM BLASTING MACHINE ...
Page 15: ......
Page 21: ......
Page 33: ...USER MANUAL VACUUM BLASTING MACHINE 1070 PNE AIRBLAST Revision 1 January 2012 page 12 5 ...
Page 34: ...USER MANUAL VACUUM BLASTING MACHINE 1070 PNE AIRBLAST Revision 1 January 2012 page 12 6 ...
Page 35: ...USER MANUAL VACUUM BLASTING MACHINE 1070 PNE AIRBLAST Revision 1 January 2012 page 12 7 ...
Page 36: ...USER MANUAL VACUUM BLASTING MACHINE 1070 PNE AIRBLAST Revision 1 January 2012 page 12 8 ...
Page 37: ...USER MANUAL VACUUM BLASTING MACHINE 1070 PNE AIRBLAST Revision 1 January 2012 page 12 9 ...
Page 38: ...USER MANUAL VACUUM BLASTING MACHINE 1070 PNE AIRBLAST Revision 1 January 2012 page 12 10 ...
Page 39: ...USER MANUAL VACUUM BLASTING MACHINE 1070 PNE AIRBLAST Revision 1 January 2012 page 12 11 ...
Page 40: ...USER MANUAL VACUUM BLASTING MACHINE 1070 PNE AIRBLAST Revision 1 January 2012 page 12 11 ...
Page 41: ...USER MANUAL VACUUM BLASTING MACHINE 1070 PNE AIRBLAST Revision 1 January 2012 page 12 11 ...