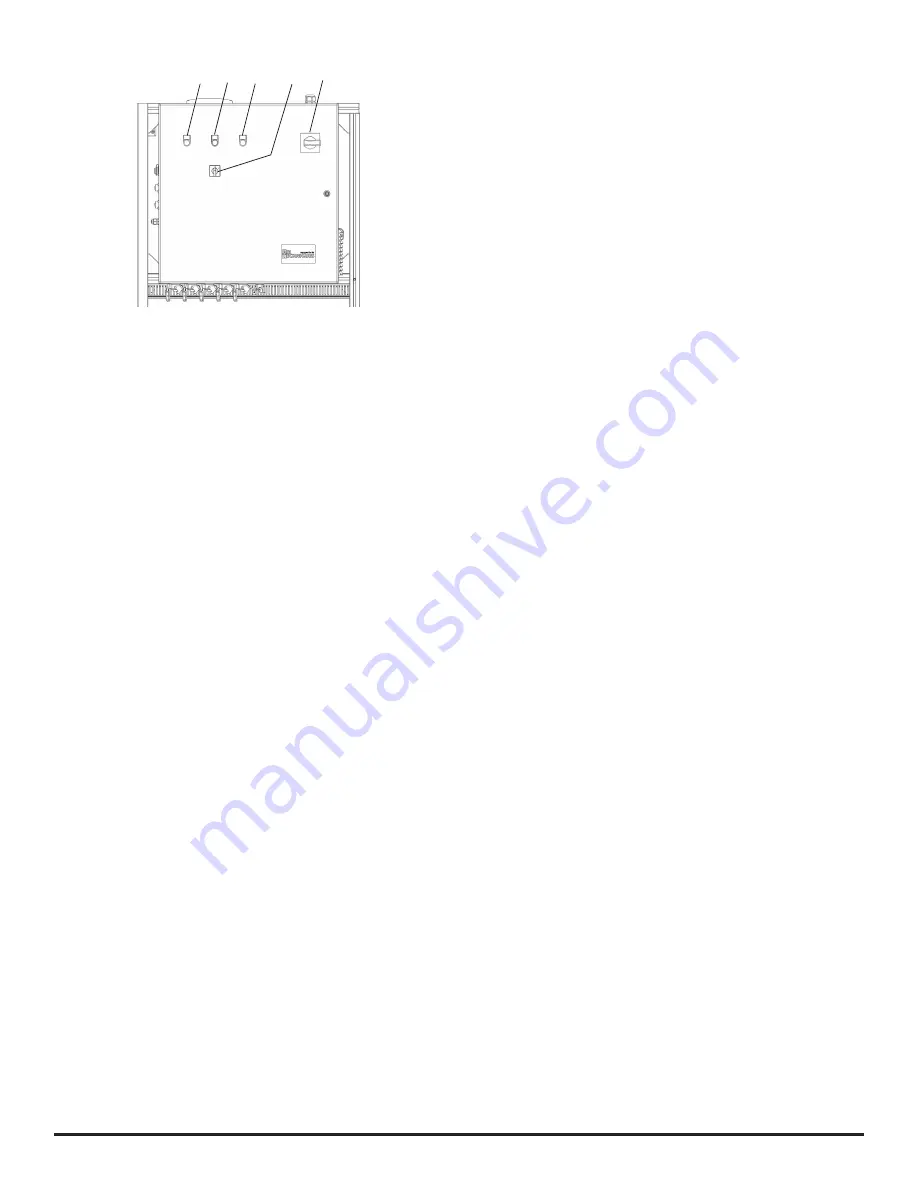
Page 11
Air Techniques, Inc.
While the compressor aggregate is in operation the accumu-
lating condensate is separated by being conveyed through
the cyclone separator and, in a second step, through a
refrigerant dryer and then separated to the waste water
system� This process is carried out automatically using a
valve in the cyclone separator and the refrigerant dryer
controller, depending on the level present�
A special load controller monitors the compressor aggregate
operation and implements an alternation of compressor
operation on a rolling system� The alternation is carried
out according to the number of operating hours each
individual compressor aggregate has performed�
The pressure in the tank can be read off using a pressure
gauge and also at the display panel�
Auxiliary operation
Depending on the amount of compressed air required and
the particular set up of the compressed air network it may
be necessary for two (or more) compressed air stations
to work together on one network� In this particular set up
one compressed air station operates in main operation,
the other(s) in auxiliary operation�
The settings for auxiliary operation are carried out on
initial set up and configuration of the complete unit using
the display panel� In auxiliary operation the control range
for cutting in and cutting off pressure for the compressed
air station is lowered by 1�5 psi (0�1 bar)� In this way the
compressed air station aggregates switch in main and
auxiliary operation alternately on and off�
5�3 Emergency mode
Emergency mode can only be used for short periods in
order to maintain an emergency supply of compressed
air in the cases of a possible defect in the system�
Turning the switch (4) to the Emergency mode setting "1"
switches on the first compressor aggregate and it starts
up in pressure free state�
After approximately 3 seconds the switch (4) can be rotated to
position "2"� The solenoid valve opens the pressure line and
the compressor aggregate begins to supply the pressure tank�
The compressor aggregate then runs in continuous operation�
The alternation of aggregates no longer takes place�
When no air is taken from the tank, the pressure in the tank
increases to 145 psi (10 bar) and will be maintained at this
level by the opening of the safety valve� The safety valve
produces a loud venting noise when it is in the open position�
Fig� 5: Control unit
1 Red LED "Fault"
2 Blue button "Reset"
3 Green LED “Run”
4 Emergency mode switch
5 Main power switch
5�1 Start operation
After switching on at the main power switch of the control
unit the refrigerant type dryer is switched on and cools
the heat exchanger to its normal operating temperature�
Depending on the actual ambient temperature this cooling
can take up to 3 minutes (see the temperature display on the
refrigerant dryer)� After approx� 60 seconds the controller
switches on the first compressor aggregate� At about 3
seconds the next compressor aggregate will be switched
on� A sensor monitors the pressure inside the tank, which
is shown by the display� Upon reaching the set pressure in
the controller (see section Technical Data) the aggregates
will be turned off sequentially�
5�2 Normal operation
A sensor monitors the pressure in the tank vessel� When
compressed air is taken from the pressure tank, the pressure
within the tank falls� At 109 psi (7�5 bar) the first compressor
aggregate switches on� If the pressure within the tank continues
to fall, then further compressor aggregate are switched on
consecutively according to the switch-on pressures set (see
4 Technical data)�
Each compressor aggregate starts up in a pressure free
state� After approximately 3 seconds the solenoid relief
valve opens the pressure line and the aggregate begins
to supply the pressure tank�
When the pressure within the tank rises, the compressor
aggregates are switched off one after the other as soon
as the preset cut off pressure of 116 psi (8 bar) has been
reached (see 4 Technical data)�
When more compressed air is taken from the tank the pressure
falls and the next aggregate switches on automatically� When
the tank pressure falls below 15 psi (1 bar), the compressed
air station switches over to emergency mode (one compressor
aggregate remains in continuous operation)�
1
3
2
5
4
Summary of Contents for AirStar AS120
Page 2: ......