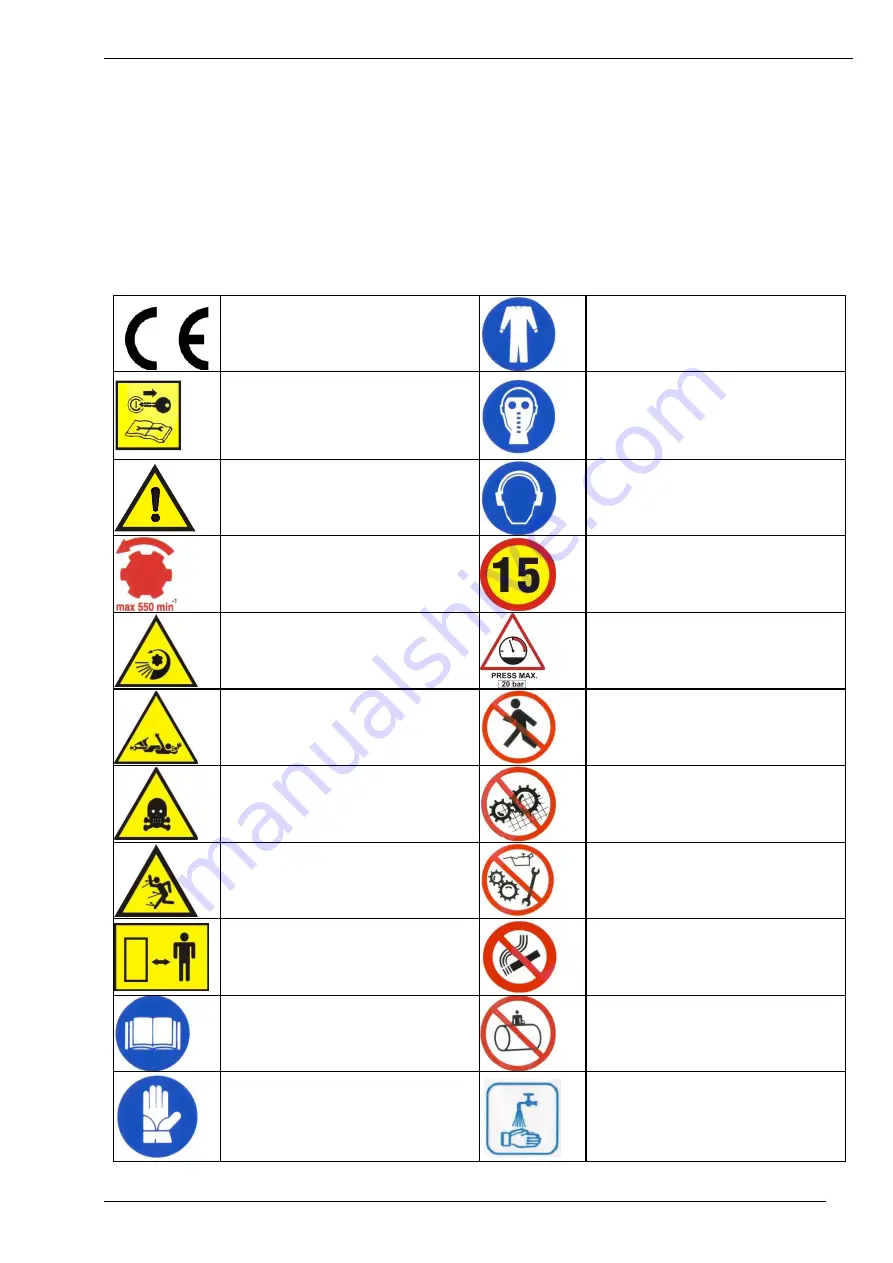
USER MANUAL
15
03/2017
4 SAFETY WARNING LABELS ON THE MACHINE AND IN THE
MANUAL
You can find certain safety and warning signs in this instruction manual that are also attached to the
machine. Take a closer look at them in order to work safely. Follow the instructions and advice
concerning precautions listed below. Make sure that the labels on the machine are in good condition
and can be well seen. After repairing the machine or replacement of any spare part make sure that all
of the labels are fitted on the appliance. Spare labels are available at your authorized seller of the
appliances.
Product conforms with the safety
requirements or standards
Use protection overalls while
working.
Warning: read the instruction
manual before connecting the
appliance to the tractor for the first
time!
If the cabin of the tractor is not
constructed in an appropriate way,
use your gas mask while working.
Warning: sign that indicates the
possibility of personal injuries or
damages of the machine!
Use ear protectors while working.
Rotating direction and number of
revolutions of power take-off
(PTO)
Speed limit
Warning: maximal rpm and the
direction of the driven shaft!
Warning: maximal allowed
pressure in the sprinkling appliance
(20 bar)!
Warning: keep away from rotating
drive shafts!
Entrance forbidden area – machine
in operation
Warning: presence of poisonous
chemical agents!
It is not allowed to remove any of
the safety devices from the
machine!
Flying parts hazard!
It is not allowed to clean, grease or
maintain the appliance as long as it
is running!
Danger!
Keep safety distance!
It is not allowed to smoke while
operating the appliance!
Follow the instructions for use!
It is not allowed to enter the
reservoir!
Use protective gloves while
working.
Water for washing of hands.
Warning: this water is not
drinkable!
Summary of Contents for AGP 1000 EN
Page 2: ......
Page 59: ...NOTES ...