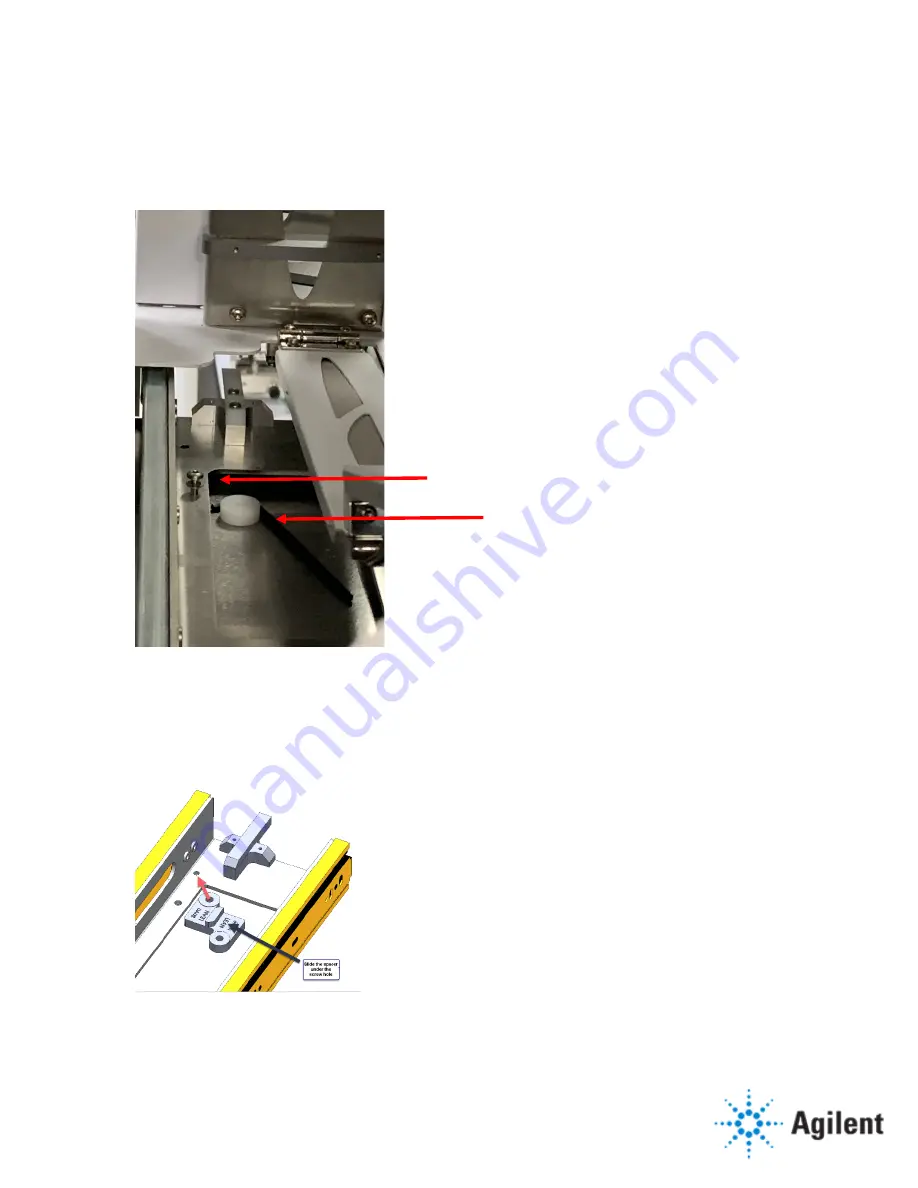
Instrument Installation Checklist
Revision:
A.00
, Issued:
January
17
, 20
21
Document part number:
D0007550
Page ____ of ____
© Agilent Technologies, Inc. 20
21
d
To increase the gap by 3-mm, turn the adjuster screw (
1
) three turns (six turns for a 6-mm
gap) and remove the existing O-ring and O-ring cup by corralling the cup with the L of a
hex wrench (
2
).
Figure 5 Adjuster screw and O-ring cup on the front-right side, viewed from the rear
e
Slide the lean correction spacer under the mounting plate, ensuring that the 3-mm (or
6-mm, if using) correction side is under the mounting plate. When the tab on the spacer is
biased against the cutout on the mounting plate, the spacer hole and the mounting plate
hole will be aligned.
Figure 6 Positioning correction spacer under the mounting plate
1
2