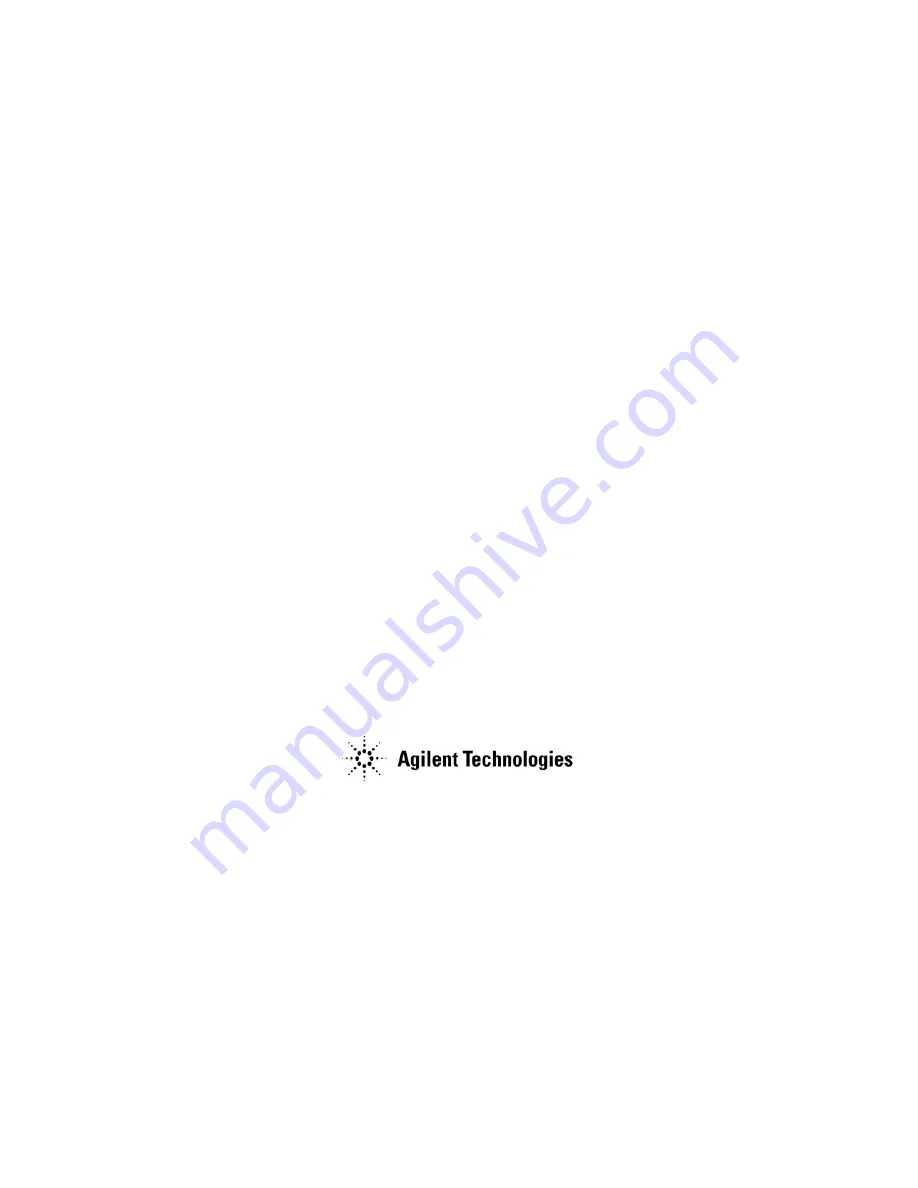
User’s and Service Guide
Agilent Technologies 11644A
X, P, and K
Waveguide Calibration Kits
This manual applies to 11644A series calibration kits with
serial number prefix 3032A.
Agilent Part Number: 11644-90371
Printed in USA
Print Date: June 2006
Supersedes: October 2002
© Copyright 1994, 1996, 1997, 2001–2002, 2006 Agilent Technologies, Inc. All rights reserved.
Summary of Contents for 11644A Series
Page 5: ...X P and K 11644A 1 1 1 General Information ...
Page 10: ...1 6 X P and K 11644A General Information Preventive Maintenance ...
Page 11: ...X P and K 11644A 2 1 2 Specifications ...
Page 17: ...X P and K 11644A 3 1 3 User Information ...
Page 24: ...3 8 X P and K 11644A User Information Changing the Wavelength Shim Calibration Definition ...
Page 25: ...X P and K 11644A 4 1 4 Use Maintenance and Care of the Devices ...
Page 34: ...4 10 X P and K 11644A Use Maintenance and Care of the Devices Handling and Storage ...
Page 35: ...X P and K 11644A 5 1 5 Performance Verification ...
Page 50: ...5 16 X P and K 11644A Performance Verification System Operation Checks ...
Page 51: ...X P and K 11644A 6 1 6 Troubleshooting ...
Page 55: ...X P and K 11644A 7 1 7 Replaceable Parts ...
Page 56: ...7 2 X P and K 11644A Replaceable Parts ...