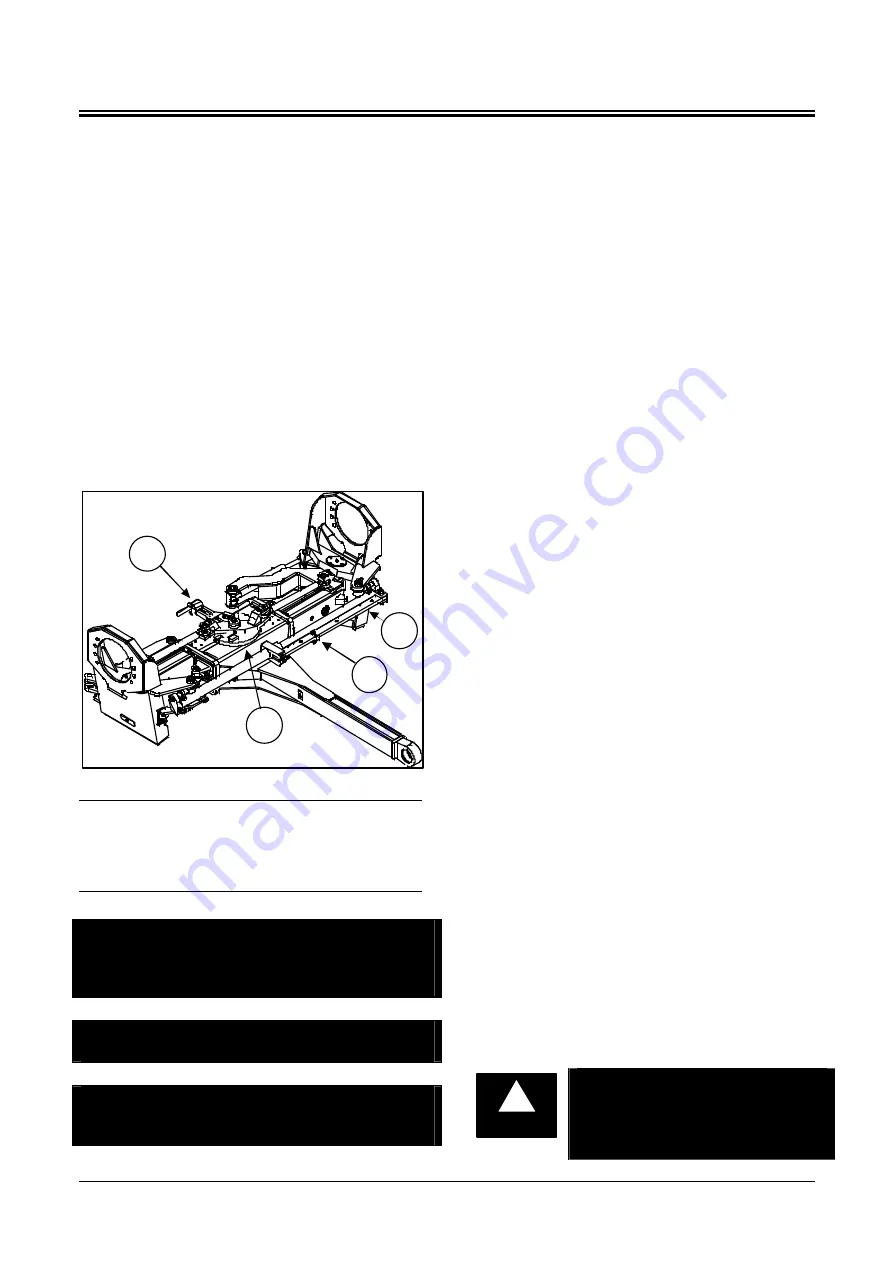
OPERATION
05.6
Operation
11-04
RoGator 418
Automatic Adjustment of the
Track Width (Option)
When adjusting the track width hydraulically it is
possible to slide between two different tracks. With
out repositioning the track lock disc and adjusting
the pins in the adjustment bar.
When the track lock disc is turned into another po-
sition and the pins in the adjustment bar are put into
another hole, other track widths can be set. This
results in the following track widths:
1.
1.50 m and 2.00 m
2.
1.80 m and 2.25 m
3.
2.00 m and 2.25 m
Track widths can be different if the track lock disc is
customer built.
Track width 1.50 m is only available on tires 300/95
R46.
Adjustable (Front) Axle
1.
Locking pin
2.
Track Lock Disc
3.
Adjustment bar
4.
Pin
NOTE: In order to be able to set the track width,
the traction control lever must be moved out of
neutral, field mode must be selected and the lock
switch must be on.
NOTE: Track width 1.50 m is only available on
tires 300/95 R46.
NOTE: Track lock disc and adjustment bar need
to be changed when other tires or rims are
mounted.
Sliding the Axle
If the track lock disc and the adjustment bar are
fixed in either position one, two or three the axle
can be sledded as following:
1. Depress the switch for the track width lock, and
put the field / road switch in the field position.
2. To change the track width of the rear axle, move
the traction control lever slightly forward so that
the machine drives forward slowly. Then press
the switch for changing the rear axle track
width. Hold the button depressed until the bar
on the track lock disc is pressed against the
stop and the pin in the adjustment bar is
pressed against the stop.
3. To change the front axle track width, move the
traction control lever back so that the machine
reverses slowly. Then press the switch for
changing the front axle track width. Hold the
button depressed until the bar on the track lock
disc is pressed against the stop and the pin in
the adjustment bar is pressed against the stop.
4. Unlock the switch for track width lock.
Setting the Track Width
The axle can slide between two different tracks de-
fined by the position of the track lock disc and the
pins in the adjustment bar. Other tracks can be
chosen by putting the track lock discs and the pins
in the adjustment bar in another position. The tracks
can be set as following:
1. Slide the axle a little bit in or out so that there is
no tension on the locking pin in the track lock
disc and the pins in the adjustment bar.
2. Pull the locking pin back. The track lock disc
can be turned now. Put the locking pin in the
bore hole corresponding to the track widths you
need. See pictures on page 5.6 and 5.7. Slide
the axle a bit in or out when the stops on the
track lock disc hit the bar and prevent the disc
from turning.
3. Take out the pins in the adjustment bar. Put the
pins on the right place into the adjustment bar
corresponding to pictures on page 5.6 and 5.7.
All the pins are marked. Every track width has
its own pin. The pins are marked with either “F”,
Front axle or “R”, Rear axle and the track width.
On track width 2.25 m no pin is used. Don’t
swap pins. This will result in a wrong toe-in ad-
justment.
WARNING
!
Caution: Don’t swap pins on the
adjustment bar. This can result in
a wrong toe-in adjustment. On
track width 2.25 m no pin is used.
1
2
3
4