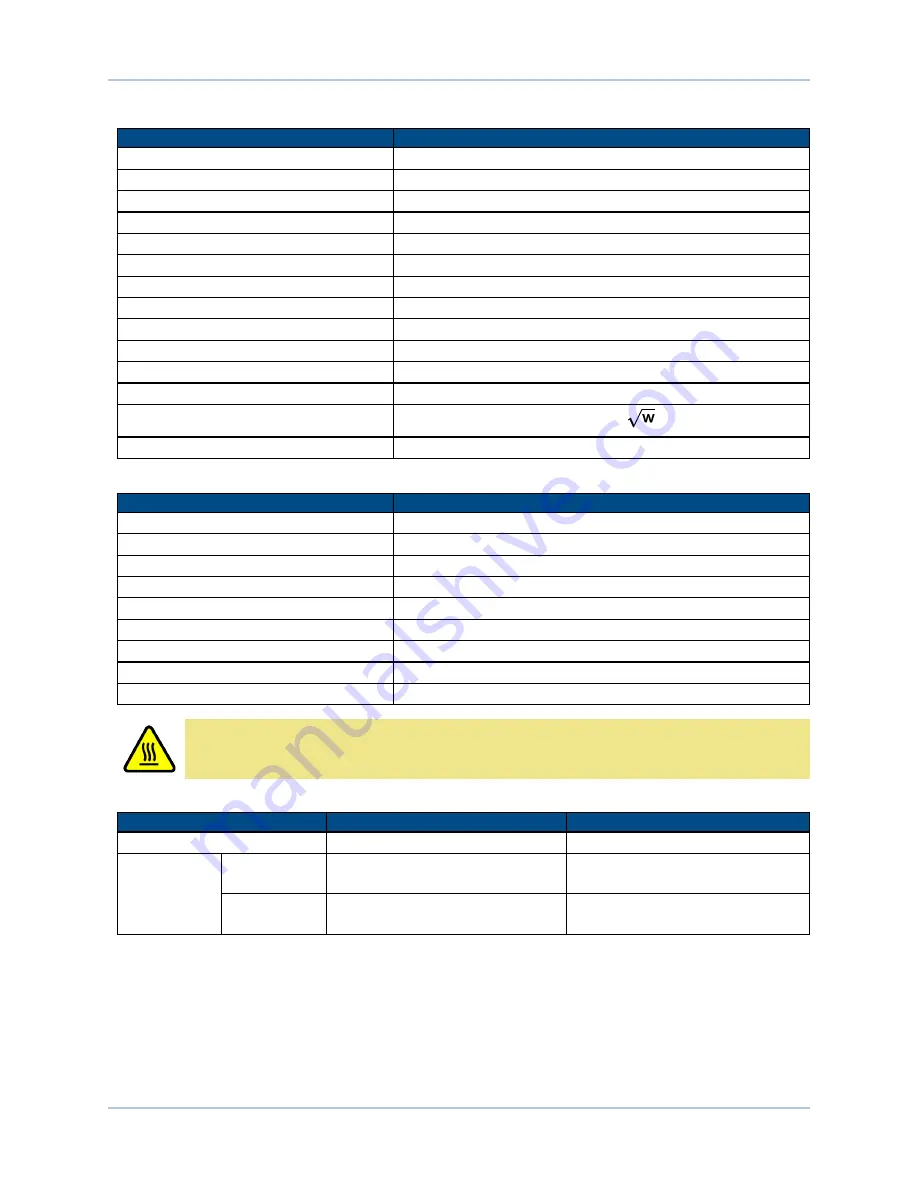
Electrical Specifications and Installation
MPS50SV Hardware Manual
Table 3-8:
DC Motor Specifications
DC Motor (-M1)
Stall Torque, Continuous
0.0045 N·m
Peak Torque
0.0095 N·m
Maximum Speed
4200 rpm
Peak Current, Stall
0.40 A
Continuous Stall Current
0.19 A
Torque Constant
0.0263 N·m/A
Terminal Resistance
54.6 Ohm
BEMF Constant
2.76 V/krpm
Inductance
0.0012 H
Rotor Moment of Inertia
1.00E-07 kg·m
2
Recommended Bus Voltage
24 V
Maximum Terminal Voltage
48 V
Motor Constant
0.0036 N·m/
Gear Ratio
676:49
Table 3-9:
Stepper Motor Specifications
Stepper Motor (-M2)
Stall Torque
0.0036 N·m
Rated Phase Current
0.15 A
Recommended Bus Voltage
24 V
Rotor Inertia
4.50E-08 kg·m
2
Full Step Angle
15°
Phase Resistance
35 Ohm
Phase Inductance
0.0165 H
Maximum Speed
2600 rpm
Gear Ratio
2704:63
W A R N I N G : The motor case temperature may exceed 75°C.
Table 3-10:
Encoder Specifications
DC Motor (and -HV)
Stepper Motor (and -HV)
Feedback
512 lines/rev Rotary Encoder
N/A
Electronic
Resolution
1.0 mm/rev
Ball Screw
0.0051 µm
0.0071 µm @ 480 steps/rev Motor
Resolution
0.5 mm/rev
Lead Screw
0.0026 µm
0.0035 µm @ 480 steps/rev Motor
Resolution
30
Chapter 3
www.aerotech.com