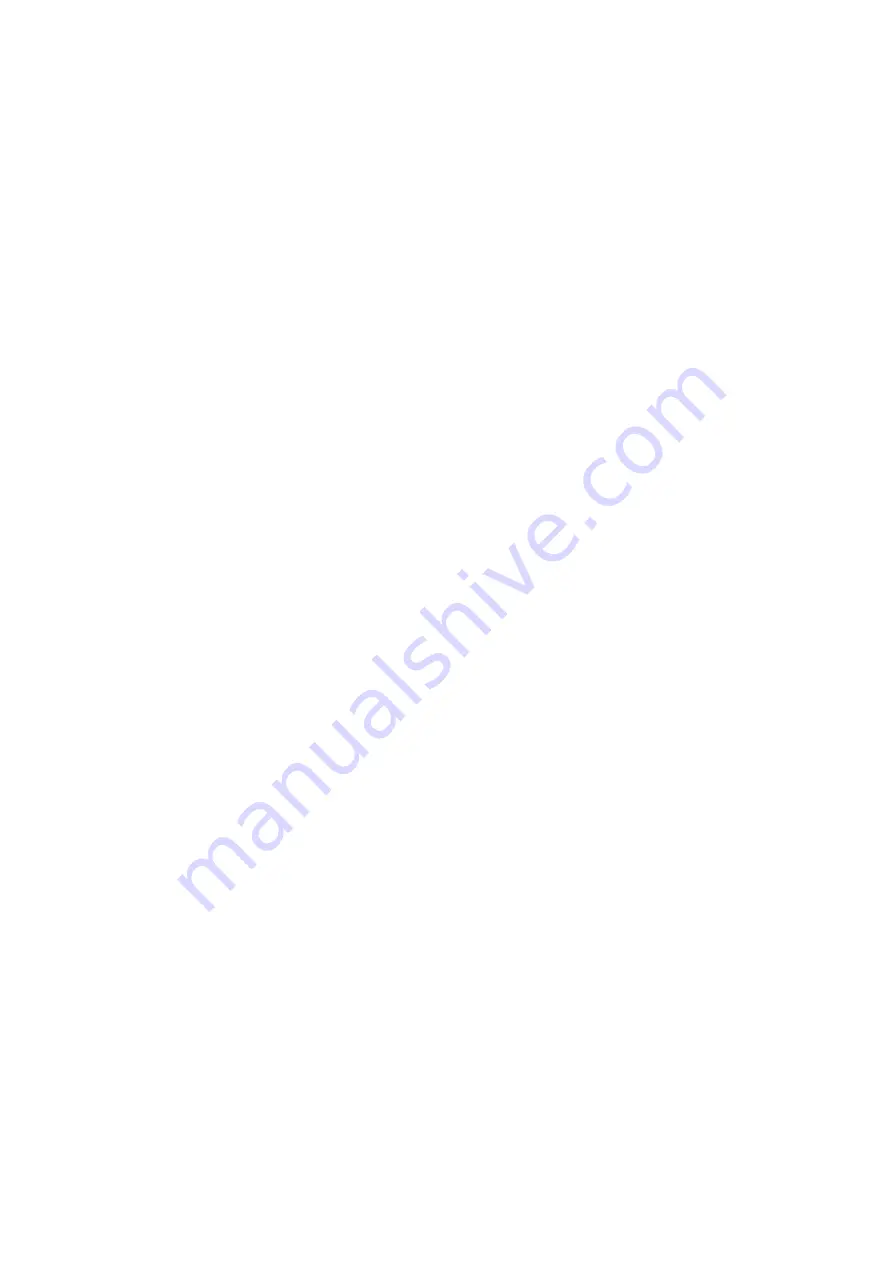
connectors.
Check for proper functioning by applying the muzzle of the fastener driving tool to a piece of wood or wooden material
and actuating the trigger once or twice.
4.3Filling the magazine
Only those fasteners specified under TECHNICAL DATA (see 1.1) may be used
When filling the magazine, hold the tool so that the muzzle is not pointing towards the operator or any other person or
animals.
4.4 Handling the tool
Pay attention to
2-Special Reference-
of these operating instructions.
Having checked that the fastener driving tool is functioning correctly, apply the tool to a work piece and actuate the
trigger.
Check whether the fastener has been driven into the work piece in accordance with the requirements.
- if the fastener is protruding, increase the air pressure in increments of 0.5 bar, checking the result after each new
adjustment;
- if the fastener is driven into an excessive depth reduce the air pressure I increments of 0.5 bar until the result is
satisfactory.
You should endeavor in any event to work with the lowest possible air pressure. This will give you three significant
advantages;
1. Energy will be saved, 2. Less noise will be produced, 3. A reduction in fastener driving tool wear will be achieved.
Avoid triggering the fastener driving tool if the magazine is empty.
Any defective or improperly functioning fastener driving tool must immediately be disconnected from the compressed air
supply and passed to a specialist for inspection.
In the event of longer breaks in work or at the end of the working shift, disconnect the tool from the compressed air supply
and it is recommended to empty the magazine.
The compressed air connectors of the fastener driving tool and the hoses should be protected against contamination, the
ingress of coarse dust chips, sand etc, will result in leaks and damage to the fastener driving tool and the couplings.
5. Maintenance
Disconnect the tool from the compressor before adjusting, clearing jams, servicing &maintenance, relocating and during
non operation.
Regular lubrication, if your tool without using the in-liner automatic oilier, place 2 or 6 drops of pneumatic tool oil into
the air inlet before each work day or after 2 hours of continuous use depending in the characteristic of work piece or type
of fasteners.
Air-operated tools must be inspected periodically, and worn or broken parts must be replaced to keep the tool
operating safely and efficiently. Check and change all worn or damaged O-ring, Seals, etc. Tighten all the screws and
caps to avoid personal injury. This should be done by an expert.
Make regular inspection for free movement of trigger, spring and safety mechanism to assure safe system is complete
and functional: no loose and missing parts, no building or stocking parts.
Keep magazine and nose of tool clean and free of any dirt lint or abrasive particles.
When temperatures are below freezing, tools should be kept warm by any convenient, safe method.