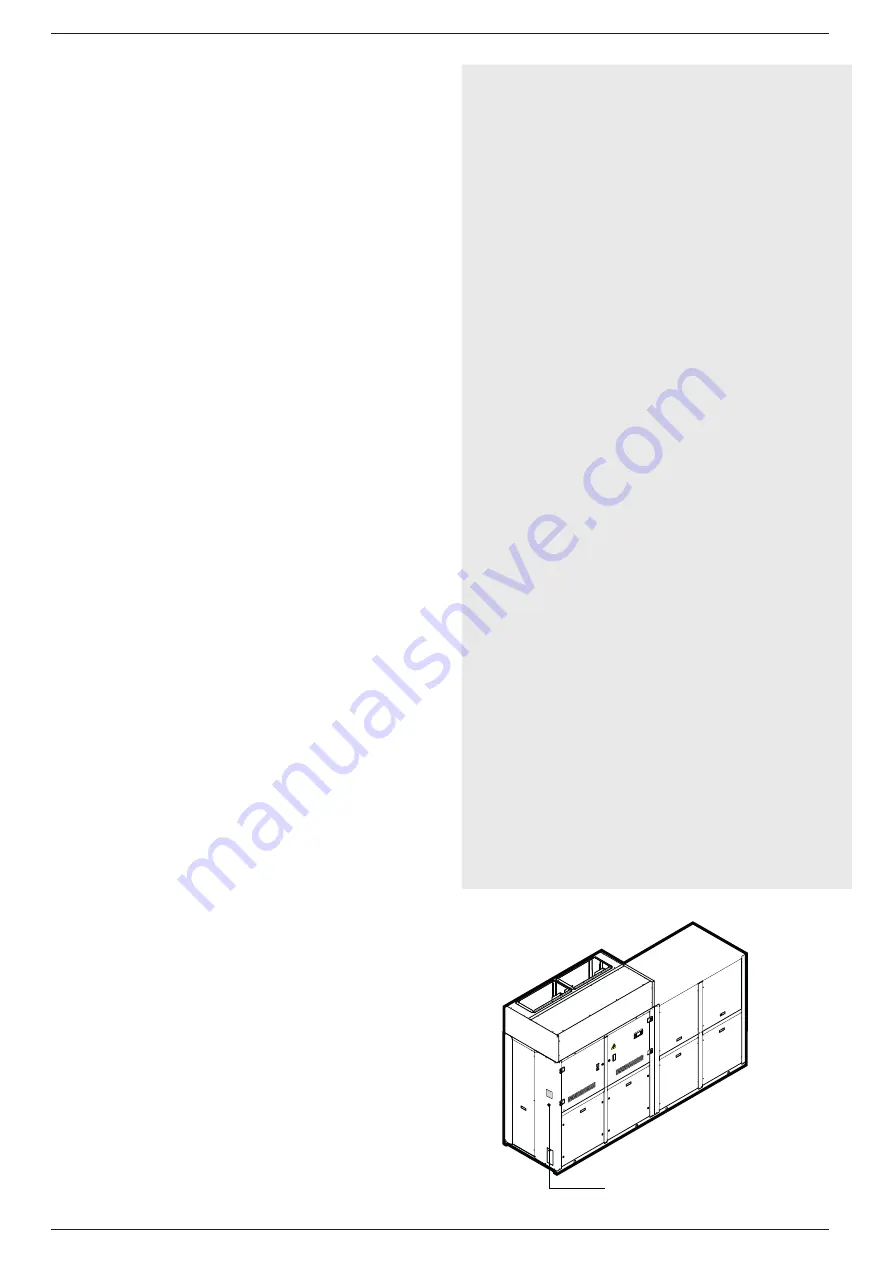
4 - EN
EN
NLC_A cod: 1606.4037360_00
1.
GENERAL WARNINGS FOR THE INSTALLER
The NLC AERMEC units are constructed according to the recognised
technical standards and safety regulations. They have been designed for
air conditioning and must be used for this purpose in accordance with
their technical features. The company shall not be contractually or non-
contractually liable for any damage to people, animals or objects, for
failures caused by errors during installation, adjustment and maintenance
or incorrect use. All the uses not expressly indicated in this manual are not
allowed.
PRESERVATION OF THE DOCUMENTATION
Deliver the following instructions plus all the complementary documentation
to the system user, who shall be responsible for keeping the instructions so
that they are always available when needed.
Read carefully this chapter; all the procedures must be carried out by
qualified personnel according to the regulations in force in the various
countries.
The warranty of the device does not in any case cover costs incurred as a
result of motorised ladders, scaffolding or any other lifting systems made
necessary to carry out the operations under warranty.
Do not modify or tamper with the appliance as dangerous situations may
be created and the manufacturer will not be liable for any damage caused.
The warranty shall not be valid if the indications mentioned above are not
observed.
SAFETY PRECAUTIONS AND INSTALLATION REGULATIONS
The appliance must be installed by an authorised and qualified technician,
in compliance with the national legislation in force in the country of
destination.
Aermec shall not be held responsible for any damage whatsoever resulting
from the non-compliance with these instructions.
Before starting any kind of work, it is necessary TO READ CAREFULLY THE
INSTRUCTIONS, AND TO PERFORM THE SAFETY CHECKS TO REDUCE ALL
HAZARDS TO A MINIMUM. All the personnel in charge must be aware of
the operations and the risks that may arise when all the unit installation
operations begin.
WARRANTY
The warranty of the device does not cover costs incurred as a result of
ladders, scaffolding or any other lifting systems made necessary to carry out
operations under warranty.
Do not modify or tamper with the chiller as this may cause dangerous
situations and the manufacturer will not be liable for any damage caused.
The warranty shall not be valid if the indications mentioned above are not
observed.
SAFETY PRECAUTIONS AND INSTALLATION REGULATIONS
The unit must be installed by an authorised and qualified technician, in
compliance with the national legislation in force in the country of destination
(MD 329/2004). AERMEC shall not be held responsible for any damage
whatsoever resulting from the non-compliance with these instructions.
Before starting any work, it is necessary TO READ CAREFULLY THE
INSTRUCTIONS, AND TO PERFORM THE SAFETY CHECKS TO AVOID ANY
RISKS.
All the personnel in charge must be aware of the operations and the risks
that may arise when all the unit installation operations begin.
PRODUCT IDENTIFICATION
The units can be identified using:
PACKAGING LABEL
- that includes the product identification data
TECHNICAL LABEL
REGULATIONS RESPECTED
IN DESIGNING AND CONSTRUCTING
THE UNIT
Standards and Directives respected on
designing and constructing the unit:
PROTECTION RATING
IP 20
ACOUSTIC PART:
1. ISO DIS 9614/2
(INTENSIMETRIC METHOD))
2. SOUND POWER (EN ISO 9614-2)
3. SOUND PRESSURE (EN ISO 3744)
REFRIGERANT GAS:
This unit contains fluoride gases with
greenhouse effect covered by the
Kyoto Protocol. Maintenance and
disposal must only be performed by
qualified staff.
STANDARD:
UL 1995
Heating and cooling equipment.
ANSI/NFPA
Standard 70 National Electrical code
(N.E.C.).
CSA C.22.1.- C.22.2
Safety Standard Electrical Installation.
REFRIGERANT GAS
This unit contains fluorinated greenhouse gases covered by the Kyoto
Protocol. Maintenance and disposal operations must be only carried out by
qualified personnel in compliance with the standards in force.
WARNING
The refrigerant circuit is pressurised. Work on the appliance can be carried
out only by an authorised ATS technician or by a qualified technician.
GAS R410A
The chiller is delivered with the necessary amount of R410A refrigerant
for its operation. It is a chlorine-free refrigerant that does not damage
the ozone layer. R410A is not flammable. However, all the maintenance
operations must only be carried out by a specialised technician with the
suitable protection equipment
RISK OF ELECTRIC DISCHARGE!
Before opening the chiller, the unit must be completely disconnected from
the mains power supply.
Technical Label