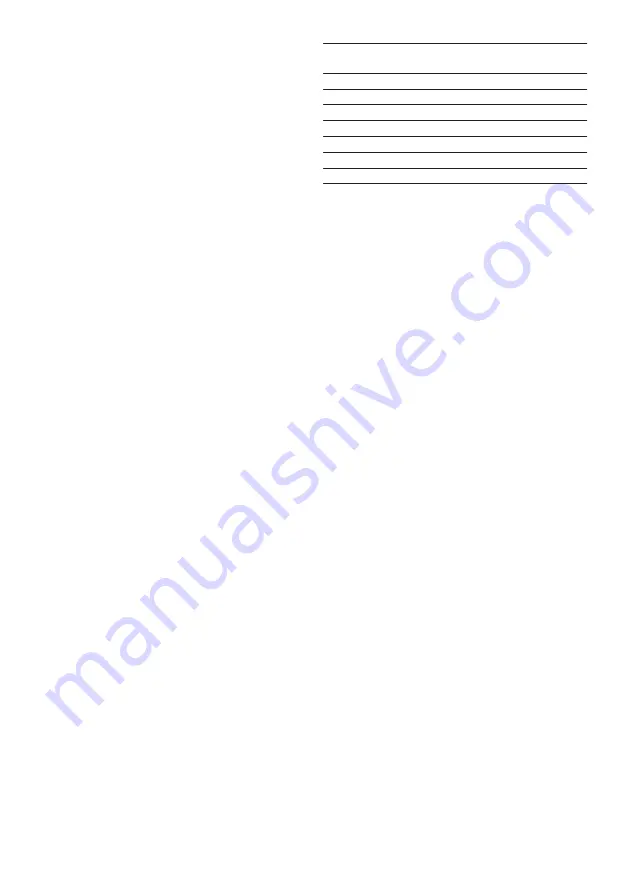
1. FITTING THE REFRIGERANT LINES
To prepare the copper pipes, proceed as follows:
1. Measure the inner and outer pipe precisely.
2. Use a pipe which is slightly longer than the
measurement taken.
3. Cut the copper pipes to measure using the pipe
cutter and smooth the ends with a pipe reamer
(Fig. A);
4. Insulate the pipes and fit conical nuts before fitting
collars to the ends of the pipes (Fig. B);
5. To fit the conical collars at 45° use a bevel edging
tool (Fig. C);
6. Deburr the inside of the refrigerant pipe.
7. During reaming, the end of the pipe must be above
the reamer to prevent the ingress of dust into the
pipe.
8. Ensure that the inside of the pipe is clean and free
of any swarf.
9. Check the conical surface is in line with the pipe,
and that it is smooth, without fractures and of
uniform thickness (Fig. D).
To make the cooling connections, proceed as
follows:
1. Feed the lines, the condensate discharge pipe and
the electric cables through the hole in the wall,
aligning the ends of the lines with the couplings on
the units (the lines are fitted on site, before feeding
them through the hole, seal the end with tape to
prevent the ingress of dirt).
2. Shape the refrigerant lines until they are aligned
with the couplings on the outdoor unit.
3. (You are advised to avoid bending the refrigerant
lines with a radius of less than 100mm, so as not to
crush the pipe section).
4. If the difference in height between the indoor unit
and the outdoor unit exceeds 3 metres (H1 - H2),
and the outdoor unit is positioned above the indoor
unit, it is recommended to provide a siphon or
a loop on the gas pipe to facilitate the return of
lubricating oil to the compressor.
5. Before connecting the pipes to the unit, check the
position is correct.
6. Remove the protection from the ends of the
refrigerant lines.
7. Clean the joint surfaces so the tightening surfaces
are in perfect contact.
8. Lubricate the connections inside and out with a thin
layer of engine oil.
9. Connect and tighten the pipes to the outdoor
unit; use a wrench and counter-wrench to avoid
subjecting the machine structure to torsion (Fig. F).
10. Connect and tighten the refrigerant lines on the
indoor unit; use a wrench and counter-wrench to
avoid subjecting the pipes to torsion (Fig. E).
11. Respect the tightening torque indicated in the
table.
External Pipe
Diameter
Pipe thickness
Tightening
Torque
inch (mm)
mm
Nm
1/4˝ (6,35)
0,5-1,0
15~20
3/8˝ (9,52)
0,5-1,0
30~40
1/2˝ (12,7)
0,5-1,0
45~55
5/8˝ (15,9)
0,5-1,0
60~65
3/4˝ (19,05)
0,5-1,0
70~75
7/8˝ (22,2)
0,5-1,0
80~85
The thickness of the pipe must withstand a
pressure of 6,0 MPa.
27
15. FITTING THE REFRIGERANT LINES