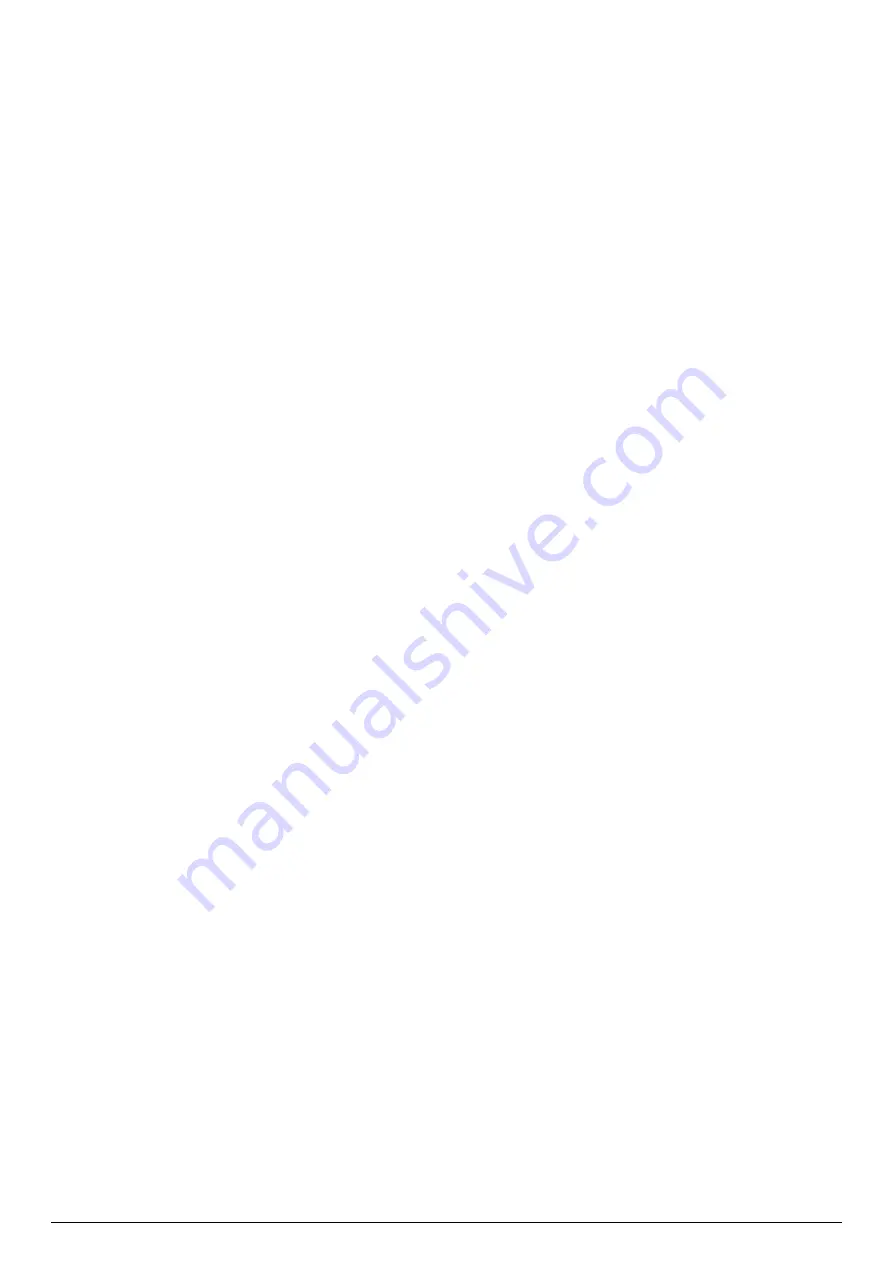
8
22.11 – 6755532_06
UNIT COMPONENTS DESCRIPTION
REFRIGERANT CIRCUIT
Scroll compressors
Compressori ermetici di tipo scroll ad alta efficienza (montati su supporti elastici
antivibranti), azionati da un motore elettrico a due poli con protezione termica in-
terna.
Crankcase heaters as standard, automatically activated when the unit stops, as long
as power is maintained to the unit.
System side heat exchanger
Brazed plate heat exchanger in stainless steel. It is externally insulated with closed
cell neoprene anti-condensation material.
Source side heat exchanger
Finned coil heat exchanger with copper tubes and aluminium louvers adequately
spaced to ensure high efficiencies.
Filter drier
Hermetic-mechanical made of hygroscopic material, able to withhold impurities
and any traces of humidity present in the cooling circuit.
One-way valve
They allow one-way flow of the refrigerant.
Thermostatic expansion valve
The mechanical type valve, with external equaliser located at the evaporator outlet,
modulates the flow of refrigerant into the evaporator based on the load and en-
sures the correct superheat of the suction gas.
Liquid sight glass with moisture indicator
Used to check for the presence of moisture in the refrigerant circuit.
HYDRAULIC COMPONENTS VERSION °
Water filter
Equipped with steel filtering mesh, it prevents the heat-exchanger from clogging
system side due to any impurity inside the circuit.
Flow switch
Checks that water is circulating in the heat exchanger, and stops the unit if this is
not the case.
Sur ANL °A 030
Differential pressure switch
Located between the inlet and outlet of the evaporator.
Checks that water is circulating in the heat exchanger, and stops the unit if this is
not the case.
Sur ANL° 030…050 - su ANL °P|° 030…050 - su ANL °A - ° 050
HYDRAULIC COMPONENTS VERSION A-P
Pump
They provide useful static pressure to the system, excluding the unit pressure drops.
Expansion vessel
Membrane type precharged with nitrogen.
Pressure relief valve
Calibrated at 6 Bar and drain pipe, it activates by discharging overpressure if abnor-
mal pressure occurs.
Air drain valve
Mounted at the highest level of the hydraulic system. The air vent is used for the
release of any air pockets from the hydraulic circuit.
System buffer tank
In steel to reduce heat gain and avoid the formation of condensation.
Insulated with polyurethane material of adequate thickness.
It reduces the number of compressor starts and stabilises the water temperature
delivered to the system.
Available only on request the tank in stainless steel AISI 304.
STRUCTURE AND FANS
Structure
Supporting structure for outdoor installation, in hot-dipped galvanized sheet steel,
with RAL 9003 polyester powder coating.
Designed to ensure the maximum access for service and maintenance.
Axial fans
External rotor axial fan with helicoidal blades
Housed in a casing, complete with protective grilles.
6 pole electric motor with thermal protection.
CONTROL AND SAFETY COMPONENTS
High pressure switch
With fixed calibration, placed on the high pressure side of the cooling circuit, it in-
hibits the operation of the compressor if abnormal work pressure occurs.
Manual reset
High pressure transducer
Placed on the high pressure side of the cooling circuit, signals the work pressure to
control board, generating a pre-warning in case abnormal pressure occurs.
ELECTRICAL CONTROL AND POWER PANEL
Electrical panel conforming to EN 60204-1/IEC 204-1, complete with:
— control circuit transformer
— door interlocked isolator
— circuit breakers and contactors for compressors and fans
— terminals for REMOTE PANEL
— spring type terminals for control circuit
— externally rated cabinet, with double panel and seals
— electronic controller
— evaporator pump and recovery pump control consent relay
— heat recovery (only for versions without pump assembly)
— All numbered cables
Door interlocked isolator
Access to the electrical panel is by operating the handle of the door interlocked
isolator which removes power to the unit.
To avoid accidentally powering up the unit during maintenance the isolator is fitted
with a locking mechanism.
Controller keypad
Allows complete control of the unit.
For further information refer to the user manual.
Electronic controller MODU CONTROL
Control of the leaving water temperature with a proportional-integral algorithm:
maintains the average leaving temperature to the desired valve
— Auto-adaptive differential starter timer: ensures the compressor minimum re-
quired running time for systems with low water content
— Intelligent defrost by decreasing pressure: determines when the coil is frosted
avoiding unnecessary defrost cycles
— External air temperature setpoint compensation (with external air temperature
sensor accessory): reduces electrical consumption
— Condensation check based on the pressure rather than on temperature for ab-
solute stability (with DCPX accessory)
— Inverse condensation check for the heat pump functioning mode also in sum-
mer (with DCPX accessory)
— Pre-alarms with automatic reset: in case of alarms a number of restarts are per-
mitted before a definitive lock out
— Alarm based on ΔT: to identify errors (reverse rotation) or reversing valve
blocked
— Compressor hour run counter
— Compressor number of starts counter
— Alarm history
— Automatic restart after power failure
— Local or remote control
Display of unit status
— Power on
— Compressor ON/OFF
— Operating mode (heating/cooling)
Summary of Contents for ANK 030
Page 2: ......