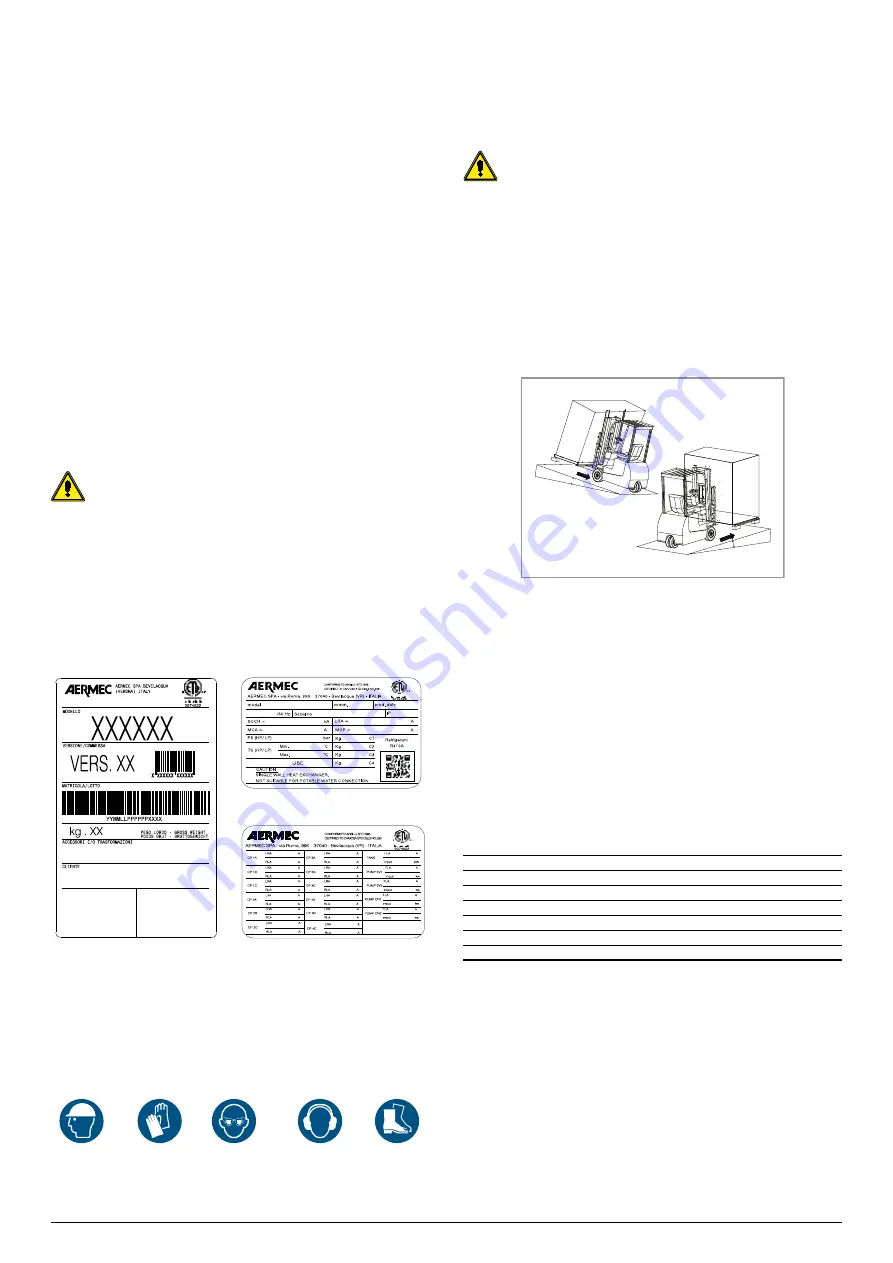
22.11 – 6755532_06
29
17 INSTALLATION
RECEIVING THE PRODUCT
Inspection upon receipt
To prevent damage during transport, the units are completely wrapped in packag-
ing and protected by plastic elements.
The machine is also wrapped in packaging. We recommend keeping this protection
during all transport and lifting operations and not remove the plastic elements until
commissioning.
There is a document envelope located inside the access panel to the electrical parts
that contains the following material:
— Instruction manual for the installer and the technical service, with the declara-
tion of conformity on the first pages
— Unit user manual
— Wiring diagrams
The instruction manual is an integral part of the unit and therefore it must be re-
covered, read and stored carefully. If lost, a copy can be found in the support area
online at www.aermec.com.
Upon receipt:
— Check that the exterior has not been damaged in any way;
— Check that the lifting and transport devices are appropriate to the type of
equipment and compliant with the transport and handling instructions at-
tached to this manual;
— Check that the accessories required for on-site installation have been delivered
and are operational;
— Check that the equipment supplied corresponds to the order and delivery note.
ATTENTION! If the product is damaged, send a registered letter with
the details of the problem to the shipping company within 48 work-
ing hours from delivery.
Product identification
Aermec products are identifiable by the
packaging label
that shows the product
identification data, and by the
rating plate
that shows the performance and iden-
tification technical data of the unit in your possession.
When the unit is positioned, make sure that the rating plate is well visible as the
information provided on it is essential for correct maintenance.
Packaging label
Technical plate
Compressor data plate
PACKAGING HANDLING AND REMOVAL
Before carrying out the packaging removal or transport operations, put on personal
protective equipment and use devices and instruments suitable for the dimensions
and weigh of the equipment.
All handling operations must be performed by qualified personnel in strict compli-
ance with all the applicable safety procedures.
The handling operations must be carried out carefully to prevent damage. The unit
may only be handled in a horizontal position and only from its base.
It is prohibited to dispose of the packaging material in the environ-
ment or leave it within reach of children:
as it may be a potential source
of danger. Therefore it must be disposed of according to what is defined
by current laws.
The unit may be handled in two ways, using:
— A forklift.
HANDLING WITH A FORKLIFT
The forks of the forklift must pass completely below the load. During descent, the
load must be lowered in reverse, with the pillar inclined to the rear, during ascent
the load must be lifted in forward gear, with the pillar inclined to the rear.
STORAGE
It is possible that the units may not be immediately installed upon receipt. If they
are stored for a medium-long period of time, the following procedures are recom-
mended:
— The units cannot be stacked;
— Check for any damage
— Make sure there is no water inside the hydraulic systems;
— Do not remove the protections from the heat exchanger;
— Do not remove the plastic protective films;
— Make sure that the electrical panels are closed;
— Before using the equipment, put all the supplied items in a dry and clean loca-
tion so that they can be used in the future.
The minimum and maximum unit storage temperature depends on the
type of refrigerant used, see the table. Above this limit, there is a risk of
refrigerant leaks through the pressure relief valves.
Maximum storage temperature
Refrigerant
Type
Class
Min temp. (°F) Max. temp. (°F)
R134a
HFC
A1
-4.0 °F
< 122.0 °F
R410A
HFC
A1
-4.0 °F
< 122.0 °F
R513A
HFC
A1
-4.0 °F
< 122.0 °F
R32
HFC
A2L
-4.0 °F
< 122.0 °F
R1234ze
HFO
A2L
-4.0 °F
< 122.0 °F
POSITIONING
The units must:
— They must be installed in an area that cannot be accessed by the public and/or
be protected against access by unauthorised persons, if necessary also install
fences;
— Be positioned on a levelled surface that is able to support the weight of the
unit with the refrigerant load and complete water, in addition to the occasional
presence of maintenance equipment;
— In locations exposed to frost, if the unit is installed on soil, the support base
must rest on concrete columns with a depth greater than the normal depth of
frost of the soil. It is always advisable to build a support base separate from the
main building to avoid the transmission of vibrations;
Summary of Contents for ANK 030
Page 2: ......