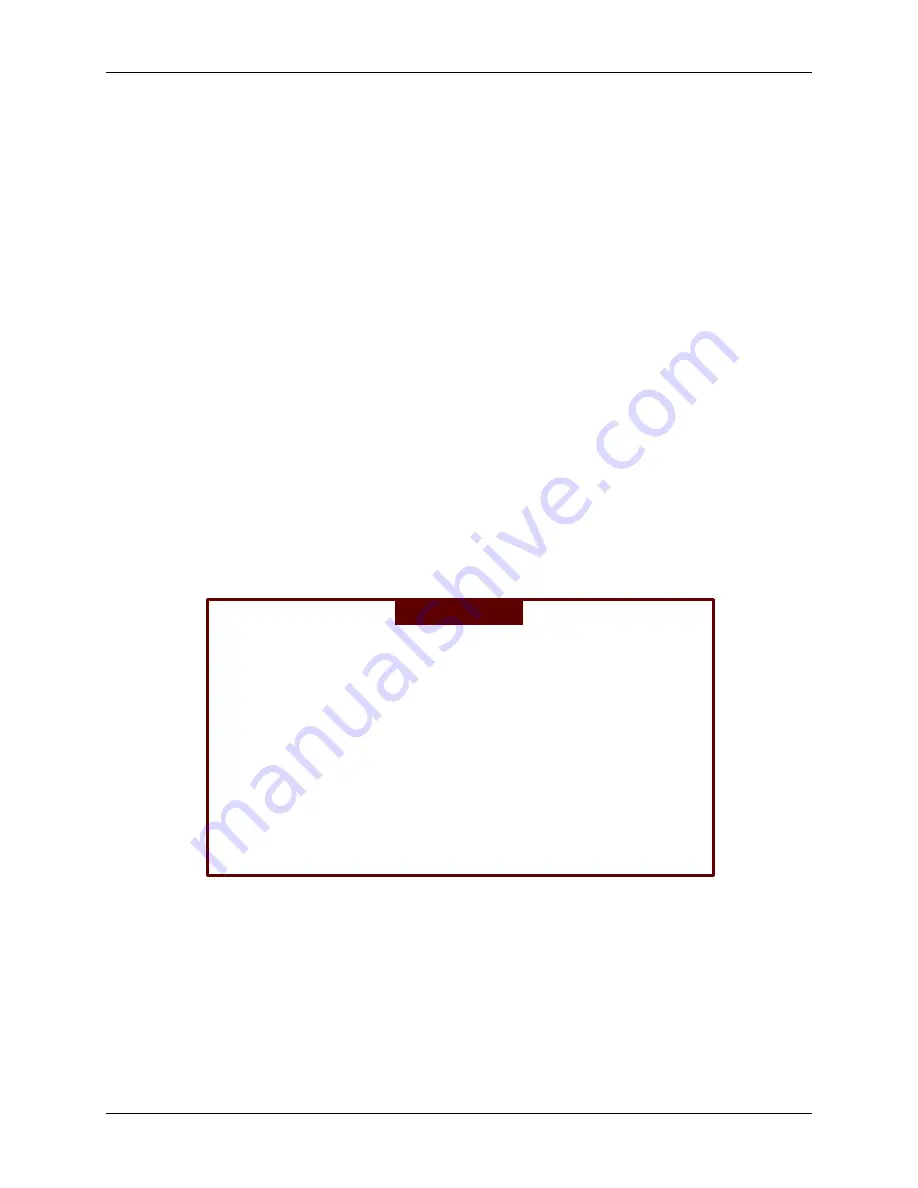
MODULEX EXT 321, 481, 641, 802, 962, 1123 BOILERS
Installation, Operation & Maintenance Manual
Page
38
of
146
AERCO International, Inc.
•
100 Oritani Dr.
•
Blauvelt, NY 10913
OMM-0087_0F
07/13/15
Phone: 800-526-0288
GF-143
A gas control valve must be installed adjacent to the boiler for isolation purposes.
3.9.2.3 Propane Gas Supply Pressure Requirements
Pressures required at gas valve inlet pressure port:
•
Nominal gas pressure – 11 inches W.C.
•
Maximum gas pressure – 13 inches W.C. with no flow (lockup) or with boiler running.
•
Minimum gas pressure – 8 inches W.C. with gas flowing (verify during boiler startup).
NOTE
Ensure that the high gas pressure regulator is installed at least 6 to
10 feet upstream of the boiler.
3.10 Flow And Return Pipe Connections
The cold and hot water flow and return circuits must be connected to the boiler via the
respective 2½” M and R connections as indicated in Table 2-1.
When determining the size of the cold/hot water circuit pipes it is essential to bear in mind the
pressure losses induced by any of the system’s components and by the configuration of the
system.
When planning the routing of the cold/hot water piping, take the necessary precautions to avoid
air traps and pockets and to facilitate the continuous purging of the system.
WARNING!
•
Before installing the boiler we recommend that the system is
flushed out with a suitable cleaning product in order to eliminate
any metallic tooling or welding residues, or oil and grime, which
could reach the boiler and affect the proper functioning of the
boiler.
•
Ensure that the system piping is NOT used for earth grounding
of electrical or telephone systems. Such grounding of system
piping is unsuitable and can cause serious damage to the
piping, boiler, and radiators.
•
It is absolutely forbidden to fit on-off valves in the piping before
the required saftey devices.
3.11 Pressure Relief Valve
The included pressure relief valve (Figure 3-15) must be fitted on the CSD-1 manifold, which is
installed on the flow pipe per instructions in the next section, 3.12, below. It complies with the
ANSI/ASME
ANSI Z21.13 / CSA 4.9
Boiler and Pressure Vessel Code,
Section IV
(‘’Heating
Boilers’’), and
CSA B51
, Boiler, Pressure vessel, and Pressure Piping Code, as applicable.
The boiler ships with an 80 psi pressure relief valve for installation into the CSD-1 manifold
header. Lower system pressures will require lower rated pressure relief valves (not supplied).