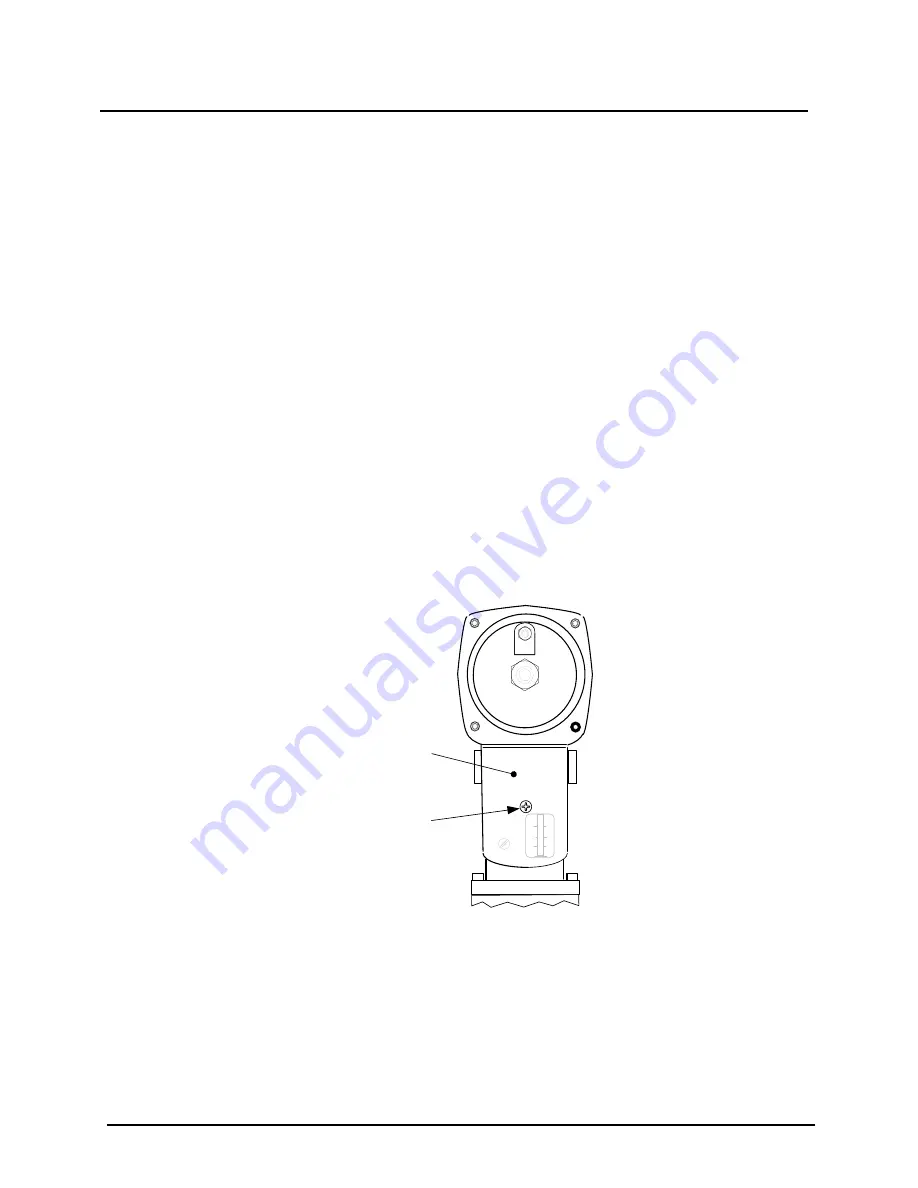
CHAPTER 6
SAFETY DEVICE TESTING
Page 76 of 166 AERCO International Inc.
•
100 Oritani Dr.
•
Blauvelt, NY 10913
•
Ph: 800-526-0288
PR1:10/18/12
Benchmark 1.5LN Low NOx Boiler
Installation, Operation and Maintenance Manual
GF-120
OMM-0041 0E
6.9 SSOV PROOF OF CLOSURE SWITCH
The SSOV shown in Figure 6-1 contains the proof of closure switch. The proof of closure switch
circuit is checked as follows:
Set the unit’s ON/OFF switch to the OFF position.
1.
Place the unit in Manual Mode and set the valve position between 25% and 30%.
2.
Refer to Figure 6-1 and locate the SSOV.
3.
Remove the cover from the SSOV by loosening the screw shown in Figure 6-4. Lift off
4.
the cover to access the terminal wiring connections.
Disconnect wire #148 from the SSOV to “open” the proof of closure switch circuit.
5.
The unit should fault and display
SSOV SWITCH OPEN.
6.
Replace wire #148 and press the
CLEAR
button.
7.
Set the
ON/OFF
switch to
ON
to start the unit.
8.
Remove the wire again when the unit reaches the purge cycle and
PURGING
is
9.
displayed.
The unit should shut down and display
SSOV FAULT DURING PURGE.
10.
Replace the wire on the SSOV and press the
CLEAR
button. The unit should restart.
11.
ACTUATOR
COVER
SCREW
SSOV
ACTUATOR
COVER
Figure 6-4: SSOV Actuator Cover Location
6.10 PURGE SWITCH OPEN DURING PURGE
The Purge Switch (and Ignition Switch) is located on the Air/Fuel Valve. To check the switch,
proceed as follows: