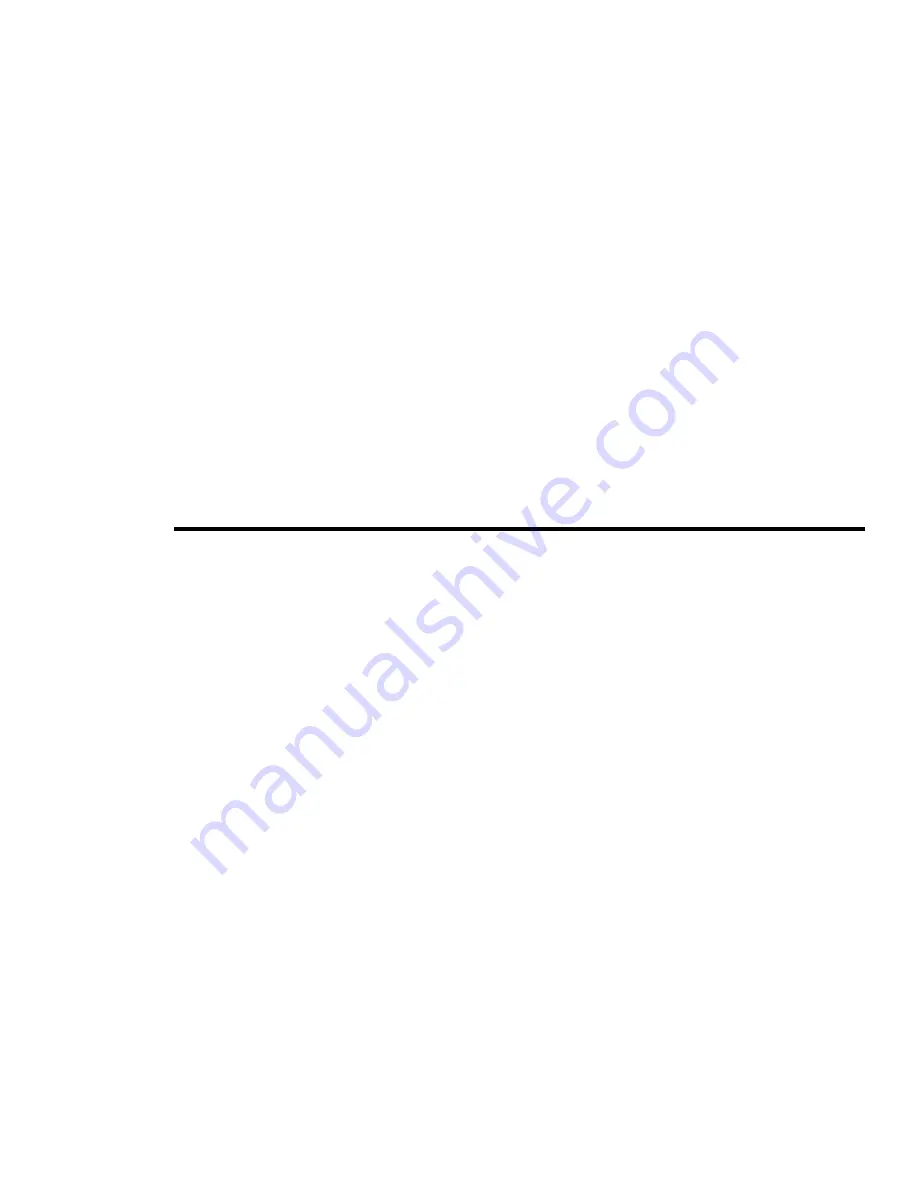
of 3 to 1, or by skipping three sizes, you
create a ratio of 4 to 1.
When selecting sieves from this series,
any number of sieves can be used for an
analysis. Care must be taken in selecting
each sieve between two points, every other
sieve, every fourth sieve, etc., to keep
within the mathematical progression of the
series.
After World War II, the International
Standards Organization (ISO) was formed
in an attempt to establish world standards.
Though the U.S. Sieve Series had proven
to be effective and was in use throughout
the world, members of the ISO would not
accept the U.S. Sieve Series as a world
standard. The ISO chose to adopt the
Preferred Number Series based on the
roots of ten. The Preferred Number Series
was suggested by Charles Renard of France
in 1879. His system is based on the tenth,
twentieth and fortieth roots of ten
(designated R-10, R-20 and R-40). See
Table 2.
A compromise was reached between the
ISO and the proponents of the U.S. Sieve
Series when it was discovered that every
third value in the R-40/3 table is in a step
ratio of 1.1885, sufficiently close to the
fourth root of two (1.1892) used in the
U.S. Sieve Series. In 1970, slight
adjustments were made in the U.S. Sieve
Series to align the series perfectly with the
ISO specifications.
Copies of these tables of specifications
can be found in Table 3.
CHAPTER 5
SIEVE CALIBRATION PROCEDURES
Quantifying
and
accounting
for
variations in test sieve results have
become two of the most important topics in
particle technology today. Once again, the
ubiquitous nature of stacks of test sieves in
powder labs around the world has
contributed to the scope of the dilemma in
sieve standardization and calibration. Kaye
states
"The
inaccuracies
and
the
uncertainties of characterization by sieve
fractionation arise from the experimental
problems of determining the sieve residues
and from the non-ideal nature of the
sieving surfaces." Further, "The presence of
a range of aperture sizes in any real
sieving surface is a source of error in sieve
based characterization studies since the
theoretical or nominal size of the sieve is
taken to be the boundary limit for the sieve
residue."
(5)
Not only is the test sieve user plagued
with variations in the weave of the cloth,
but also confronted with the effects of
particle shape on sieving results. Nearly
50 years ago, A.M. Gaudin wrote, "Powders
with identical size distributions, densities
and chemical composition may behave
quite differently as a result of variations in
particle shape between samples. For
example, powders consisting solely of
spherical particles are likely to have good
flow properties, while powders containing
needlelike particles will not." Further, "In
addition, it is impossible to isolate the
concepts of particle size and shape, since
the method of size measurement will
influence the particle size which is
determined.” (6)
Numerous approaches have been tried
to compensate for the effects of variations
in wire cloth and particle shape. The
methods have fallen into 3 basic
categories: 1) inspection of the mesh to
determine opening size, 2) material testing
of the sieves to determine if sieves fall
within performance specifications, and 3) a
Summary of Contents for VariSifter VS1000
Page 2: ......
Page 32: ......
Page 34: ...Table 2 ...
Page 35: ...Table 3 ...
Page 36: ...Table 3 cont d ...
Page 37: ...Table 4 ...
Page 38: ...Table 5 ...
Page 39: ...Table 6 ...
Page 46: ......