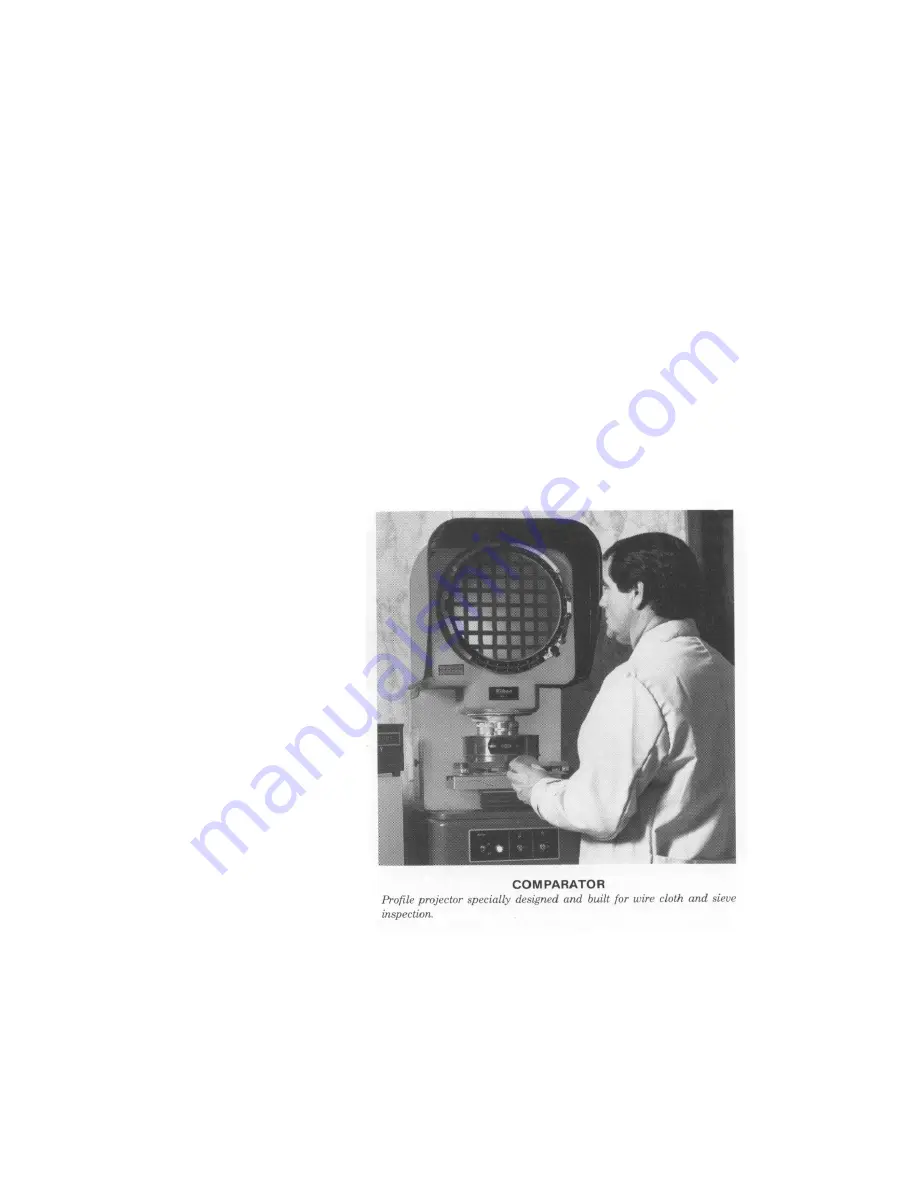
and the test is run for 30 minutes, the
probability of larger-than-nominal particles
finding those oversized openings is much
greater than if the test was run for only 15
minutes. Similarly, if the sample of powder
contains a large percentage of elongated or
needle like particles, a longer test interval
would provide a greater likelihood that the
elongated particles will orient themselves
‘on end’ and pass through the openings. If
the sieving cloth has a wide range of
opening sizes, the sieving of this type of
material has a compounded error.
Another
factor
which
must
be
considered is the reaction of the material to
ambient conditions. The most accurate
test sieve available would be of minimal
use if the relative humidity in the test lab
was 99%. Extremely dry conditions can
cause fine powders to adhere to the sieve
components and each other with strong
electrostatic charges. Additional types of
sieving problems are discussed in the
glossary section.
To minimize error caused by wire cloth
variation, steps must be taken at every
stage of fabrication that will assure the
uniformity of the woven mesh as well as
the compliance with the applicable
standards. Both the weaver and the test
sieve manufacturer must maintain a
constant monitoring program measuring
the actual opening sizes of the wire cloth
as well as the uniformity of those openings.
The loss to the manufacturers in rejected
out of specification sieve cloth is a gain to
the end-user in uniformity and compliance.
Summary of Contents for VariSifter VS1000
Page 2: ......
Page 32: ......
Page 34: ...Table 2 ...
Page 35: ...Table 3 ...
Page 36: ...Table 3 cont d ...
Page 37: ...Table 4 ...
Page 38: ...Table 5 ...
Page 39: ...Table 6 ...
Page 46: ......