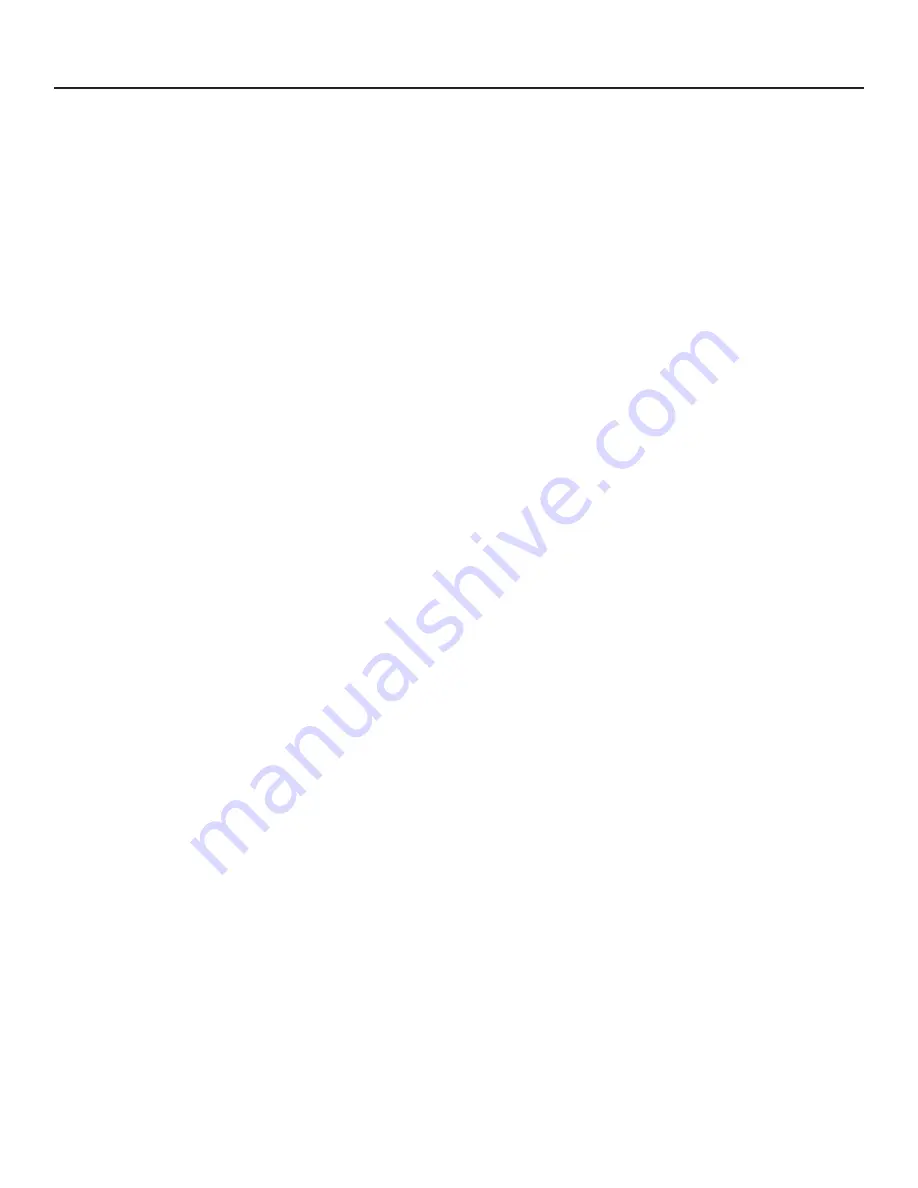
Removing the Impeller
(See Parts Diagram on page 13 of this manual for pump component locations.)
3. To prevent motor shaft from turning, carefully place a 7/16” open-end wrench over the two
(2) flats on the end of the shaft.
4. Remove the impeller (item #5) by rotating counterclockwise.
Removing the Ceramic Seat
(See Parts Diagram on page 13 of this manual for pump component locations.)
5. Remove the spring seal assembly (item #6) and seal plate (item #7) from the motor by
removing the four (4) 3/8” x 1” bolts that secure it to the motor, using a 9/16” wrench or
socket.
6. Press the ceramic seat with rubber cup out of the seal plate (item #7). If tight, use a small
screwdriver to tap seal out.
STOp
– Clean all recesses & parts to be reassembled. Inspect gaskets & replace if necessary.
Seal Installation
(See Parts Diagram on page 13 of this manual for pump component locations.)
7. Clean and lightly lubricate the motor shaft and seal recesses in the seal plate (item #7) with
a dilute solution of nongranulated liquid-type soap. Gently wipe the polished face of the
ceramic seal with a soft cotton cloth. Lubricate the rubber cup on the ceramic seat and press
it firmly into the recess of the seal plate (item #7), with the polished ceramic surface facing
out.
8. Reassemble the motor to the seal plate (item #7) using the four (4) 3/8” x I” bolts.
9. Gently wipe the black, polished surface of the spring seal assembly (item #6) with a soft
cotton cloth.
10. Press the spring seal assembly (item #6) onto the motor shaft, with the black polished surface
facing the ceramic seat.
Replacing the Impeller and Diffuser
(See Parts Diagram on page 13 of this manual for pump component locations.)
11. Screw the impeller (item #5) onto the motor shaft in a clockwise direction. Tighten snugly by
holding motor shaft with wrench as noted in step #3.
12
INSTALLATION INSTRUCTIONS