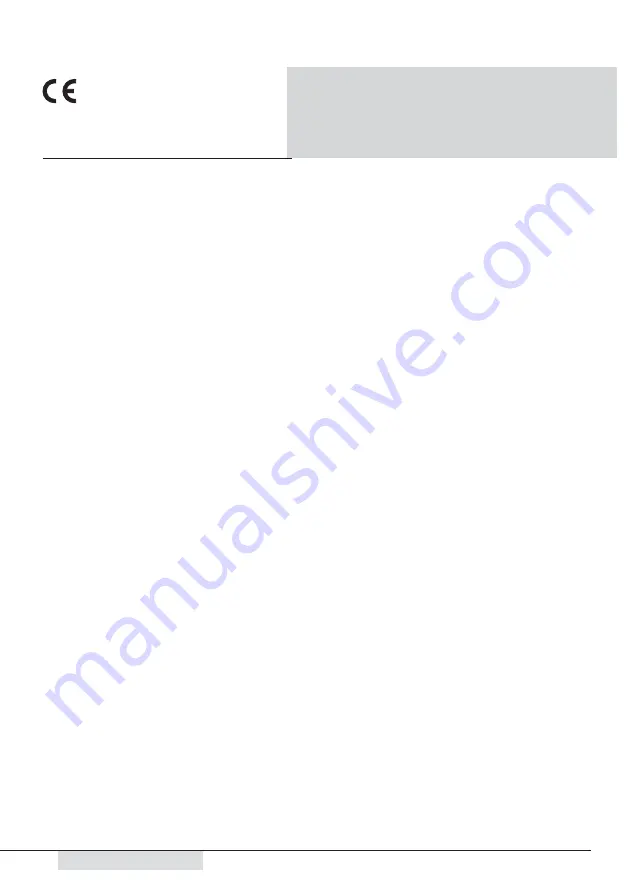
20/10/21 Rev:1.0.1
(LINGUA ORIGINALE)
3
• Type: Supply system for solid fuel fi replaces
• Model: FIREPOD universal
• Revision 1.0.1
System
FIREPOD universal
INSTRUCTION MANUAL
1 INTRODUCTION
4
1.1 Using the manual
4
2 WARNINGS
4
3
PRODUCT DIMENSIONS AND TECHNICAL DATA
5
3.1
Identifi cation plate
6
3.2 Safety symbols
6
4
KIT AND ACCESSORIES
7
5 INSTALLER’S RESPONSIBILITIES
8
6 INTENDED USE OF THE SYSTEM
8
6.1 Installation diagram
8-9
7
INSTALLATION of the basic components
10
7.1 Control panel
10
7.2 dispenser tank
10
7.3 Installation of the dispenser on tanks and compartments with controlled pressure
11
7.4
Motor
11
7.5 Suction inlet
12
7.6
Antistatic
fl exible piping Ø 45 mm
12
7.7 Flexible pipe with suction lance
13
7.8 electrical connection cables
14
8
ACCESSORIES - OPTIONAL
14
8.1 Minimum level sensor for tank
14
8.2 Air exhaust silencer
15
8.3 Dust separator fi lters
15
8.4
Antistatic
PU
fl exible pipe Ø 45 mm
15
8.5 Sleeve Ø 45 mm for joints
15
8.6 Adjustable shelf for rectangular dispenser tank
16
8.7 Electrical wiring extensions
16
9 PIPES
CONNECTIONS
16
10 ELECTRICAL WIRING
17
11 SUMMARY OF THE INSTALLATION PHASES
17
12 FIRST START-UP AND COMMISSIONING
17
13 CORRECT USE OF THE SYSTEM
18
14 MAINTENANCE AND END OF LIFE
19
14.1 End of life
19
15 TROUBLESHOOTING
20
16 WARRANTY
21
17 CERTIFICATION
22
INDEX