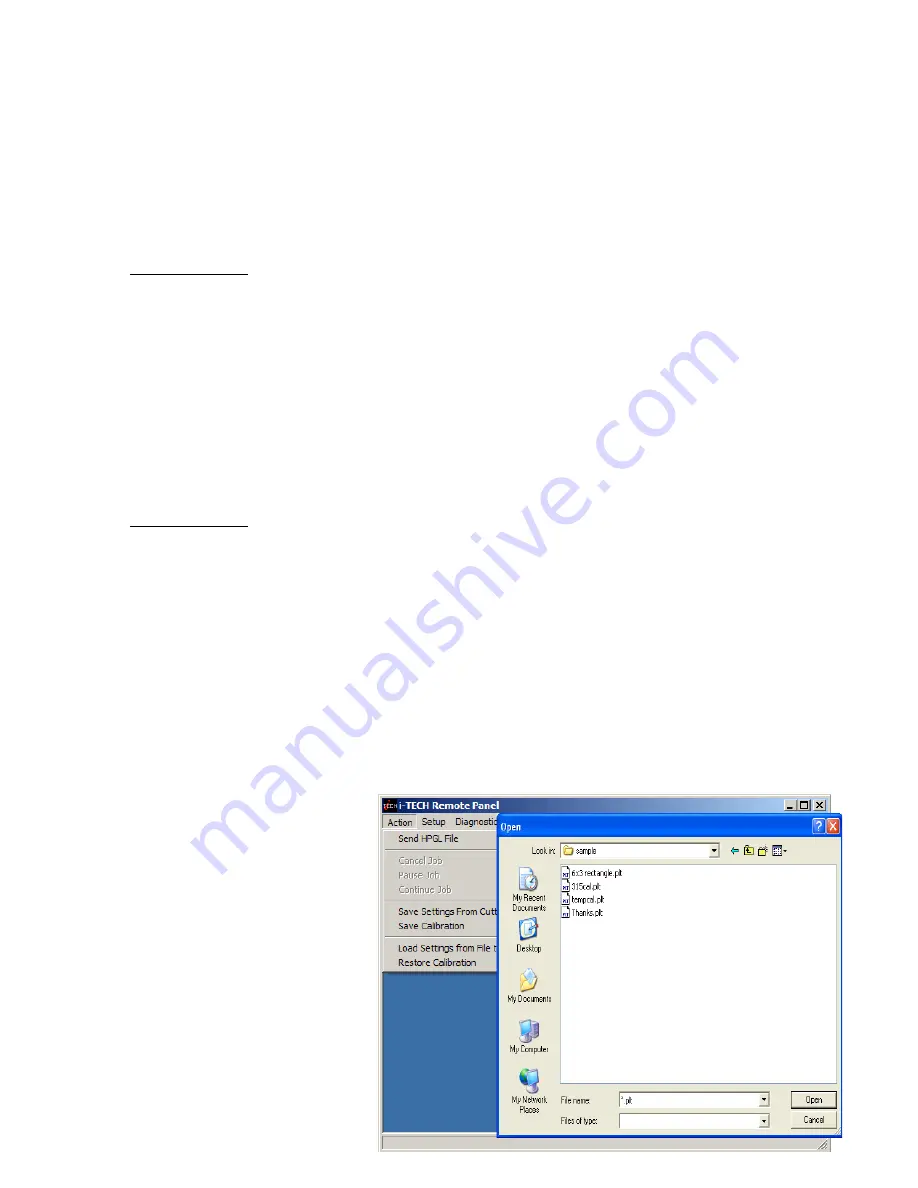
SEt
loads or saves a custom set-up or power up default. Press the select key to initiate the menu
function. Press the left or right arrow key to display
SEt
. Press the up or down key to scroll thru
(LOAd, Save), press select, press the up or down key to scroll thru the settings (1 – 6). Press the
select key to load or are save the setting. Setting #1 is loaded when the machine is powered up.
(see also factory and custom set-up section)
The
set
menu item has 2 sub-menus:
Load-
loads a setup.
To load a setting
:
Press select
Press left or right arrow until
SET
menu is displayed.
Press up or down arrow to display
Load
.
Press select
Press up or down arrow to display the number of the setting you want to
load (1-6)
Press select.
Save-
saves a customized setting.
To save a setting:
Adjust force, speed, acceleration as needed.
Press select
Press left or right arrow until SET menu is displayed.
Press up or down arrow to display Save.
Press select
Press up or down arrow to display the number of the setting you want to
customize (1-6) (# 1 is the setting that is loaded on power up.)
Press select.
The display will blink FFFF, and then return back to your setting.
Remote Panel
The Remote Panel program is used
to address all i-TECH CUTTER
functions. It is loaded onto the
computer that is directly connected
to the i-TECH CUTTER by the
installation cd. The installation
program places a shortcut on the
Windows Desktop so that you can
easily start the program when
needed. It can be run in the
background with most cad
programs.
14