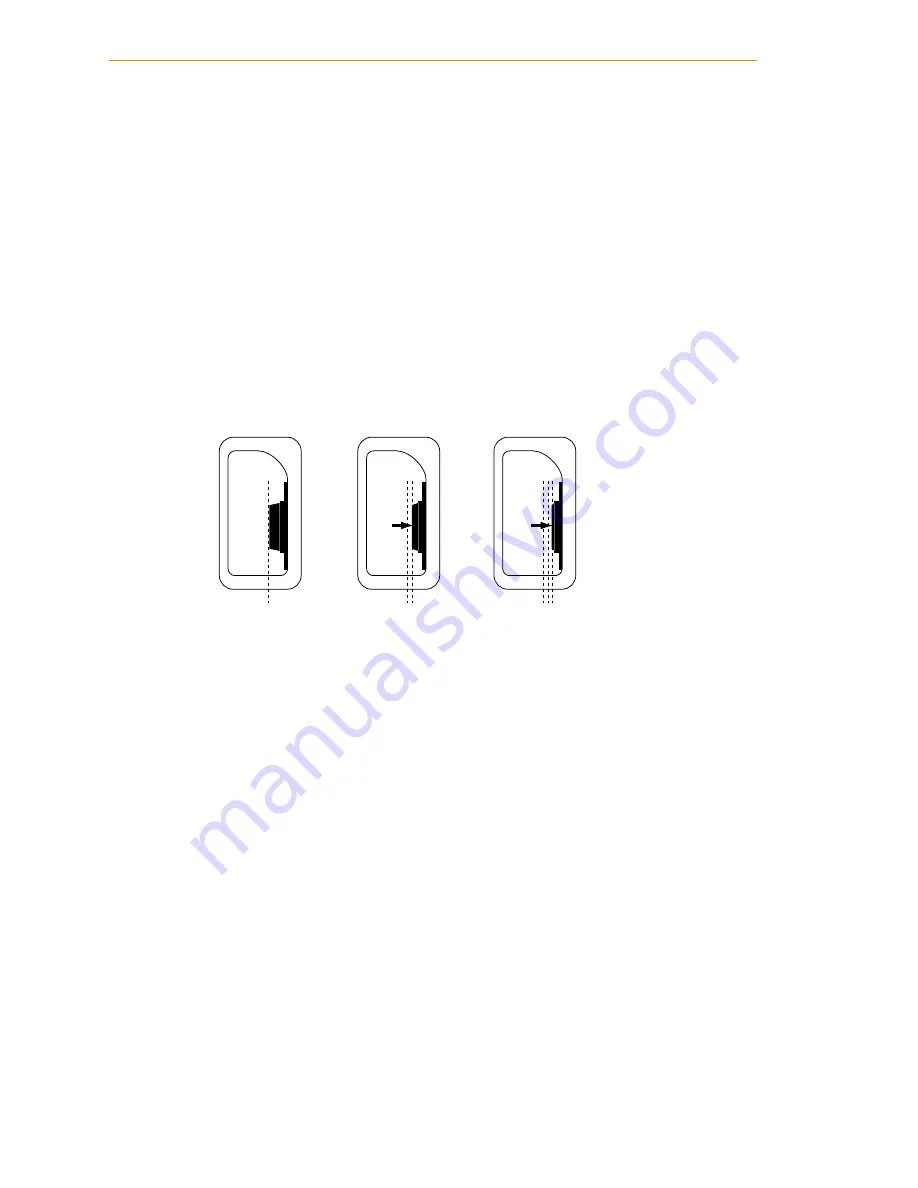
Appendix C - Using the Manual Control Pendant (MCP)
126
Adept SmartController User’s Guide, Rev. E
MCP-4
The MCP-4 has the same functionality as the MCP III, except that it has a 3-position enable
switch and a dual channel E-Stop circuit. The 3-position enable switch provides additional
safety for the operator. See the next section for a description of the enable switch.
3-Position Enable Switch
The 3-position enable switch on the MCP-4 works as follows (see
Figure C-1
):
Position 1
- switch is not pressed, high power cannot be enabled. (Switch is open.)
Position 2
- switch is pressed in to the middle position, high power can be enabled.
(Switch is closed.)
Position 3
- switch is pressed in past the middle position, high power is removed. (Switch
is open.)
Figure C-1. 3-Position Enable Switch on MCP-4
Position 1:
switch is not
pressed
Position 2:
switch is pressed in
to the middle position
Position 3:
switch is pressed in
past the middle position
Summary of Contents for SmartController CS
Page 2: ......
Page 36: ...Chapter 2 SmartController Installation 36 Adept SmartController User s Guide Rev E...
Page 84: ...Chapter 4 AdeptVision sAVI Option 84 Adept SmartController User s Guide Rev E...
Page 155: ......
Page 156: ...3011 Triad Drive Livermore CA 94551 925 245 3400 P N 00356 00100 Rev E...