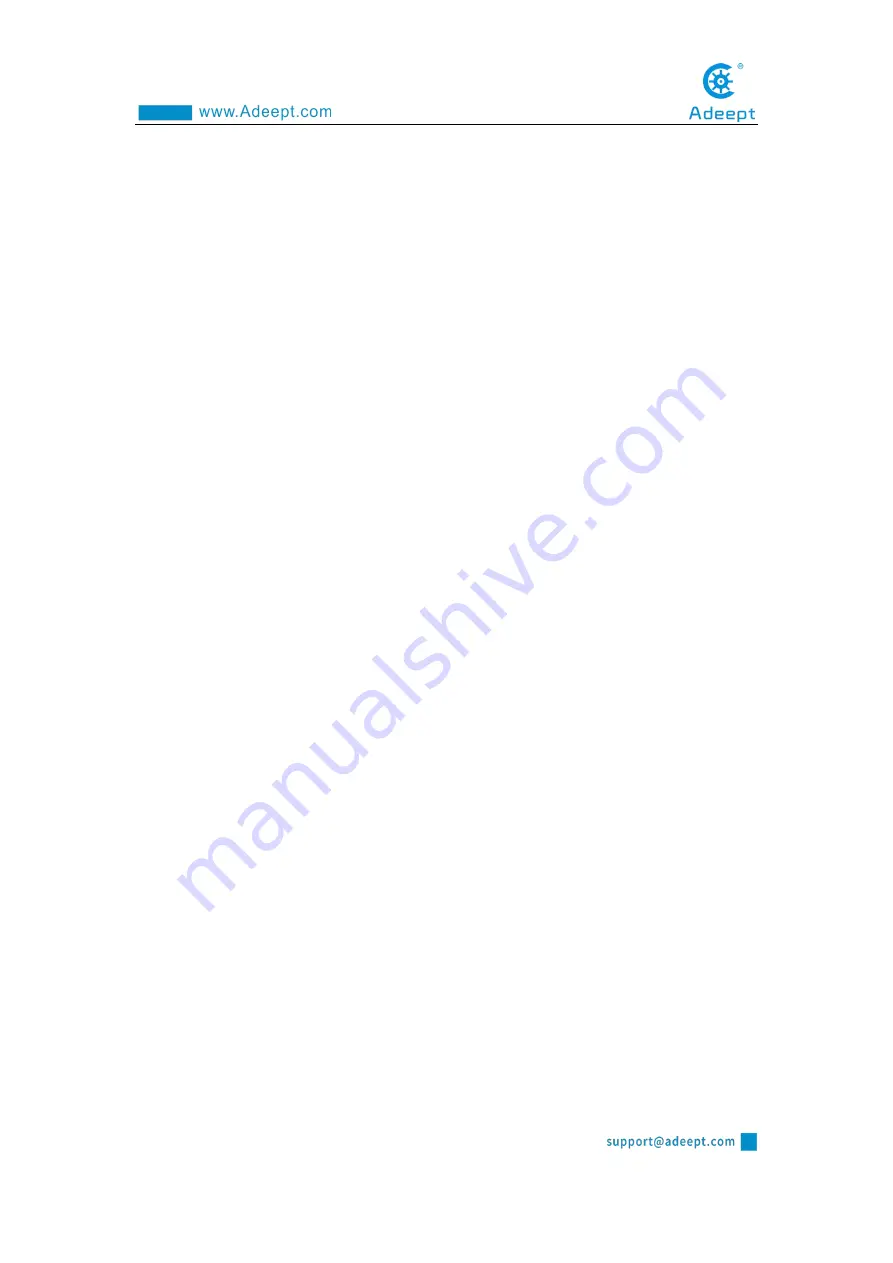
16
normally. When you use the power adapter to power the Raspberry Pi, you can check
the specifications on your power adapter.
When the Robot HAT is connected to a load, such as a motor or multiple servos,
you need to use a high-current power supply to connect to the Vin on the Robot HAT.
You can use two 18650 batteries that support high-current to power the Robot HAT.
For power supply, our product will provide a dual 18650 battery box with a 2pin
interface. You can directly connect it to the Robot HAT.
When the USB interface on the Robot HAT is used for power supply, the switch
of the Robot HAT does not control whether to supply power. The switch of the Robot
HAT can only control the power supply of Vin.
Do not use the USB port on the Robot HAT and Vin to supply power at the same
time. If you need to debug the program for a long time and don’t want to remove the
battery, you can set the switch on the Robot HAT to OFF, so that when the USB cable
is used to connect the Robot HAT, the Robot HAT is powered by USB.
If your robot restarts automatically after it is turned on, or after it is turned on
normally, it is disconnected and restarted at the moment when the robot starts to move,
it is likely that your power supply does not output enough current. The robot will
automatically restart when it is turned on. Run the program to place all the servos in
the neutral position. The voltage drop generated during this process causes the
Raspberry Pi to restart.
We have tested that the peak current of the robot is around 3.75A when powered
by 7.4V, so you need to use a battery that supports 4A output.
You can also use the power lithium battery to power the Robot HAT. Robot HAT
supports power supply below 15V.
When assembling and installing the servo rocker arm, you can use a USB cable to
power the Robot HAT. After the Raspberry Pi with the robot software is installed, it
will control the Robot HAT to set all the servo ports to output neutral signals. You can
connect the servo to any port. The gear of the servo will rotate to the neutral position,
Summary of Contents for PiCar-Pro
Page 1: ......
Page 13: ...10 2 Introduction of GPIO pins 1 GPIO pin comparison table...
Page 16: ...13 Raspberry Pi through a computer or directly to control the Arduino...
Page 26: ...23 3 Then click Finish 4 The software interface after opening is as shown below...
Page 30: ...27 6 Click CHOOSE SD 7 Then select the SD card we need to burn...
Page 41: ...38 Click CONTINUE WITHOUT PERMISSION...
Page 62: ...59 Controlling the switches of Port1 Port2 Port3 on the development board...
Page 67: ...64...
Page 99: ...96 x1 x1 x1 x1 x1 A set of acrylic...
Page 108: ...105 Prepare the acrylic panel and acrylic gasket as shown in the picture above...
Page 112: ...109...
Page 114: ...111 Use M2 5 12 screws and M1 7 6 6 self tapping screws to fix...
Page 116: ...113...
Page 117: ...114...
Page 118: ...115...
Page 121: ...118...
Page 123: ...120...
Page 127: ...124 Use M3 4 screws to fix two L shaped aluminum alloys...
Page 128: ...125 Use M3 4 screws to pass through the aluminum alloy and L aluminum alloy to fix the servo...
Page 130: ...127...
Page 135: ...132 shown below Use M3 10 screws to fix aluminum alloy and aluminum alloy sheet...
Page 136: ...133 Install the tire and fix it with M4 locknut...
Page 137: ...134 Install small LED lights...
Page 139: ...136...
Page 141: ...138...
Page 142: ...139...
Page 145: ...142...
Page 147: ...144 Install the inner 4mm coupling and fix it with screws...
Page 153: ...150...
Page 154: ...151 The installation is complete 9 5 Circuit Wiring Diagram Robot HAT board interface diagram...
Page 168: ...165 Execution function 1 if __name__ __main__ 2 radar_scan 3 GPIO cleanup...
Page 177: ...174 Adeept is the name of the WIFI hotspot 12345678 is the password of the WIFI hotspot...
Page 178: ...175...