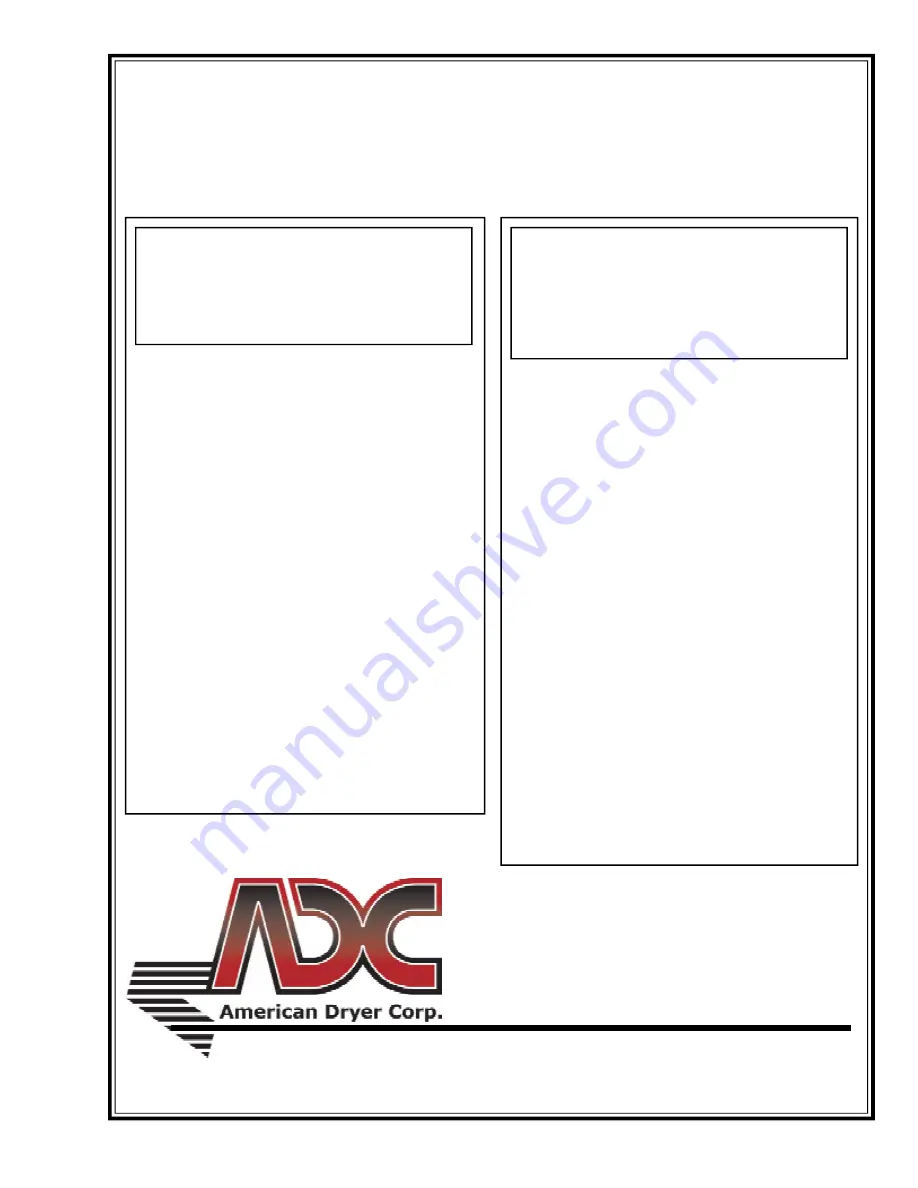
American Dryer Corporation
88 Currant Road
Fall River MA 02720-4781 USA
Telephone: +1 (508) 678-9000 / Fax: +1 (508) 678-9447
e-mail: [email protected]
www.adclaundry.com
AD-330/AD-320 Installation Manual
Phase 5 / Dual Microprocessor Controller (DMC)
Gas – Electric – Steam
(for models mfd. as of February 1992)
ADC Part No. 112144 -46
AVERTISSEMENT: Assurez-vous de
bien suivre les instructions données dans
cette notice pour réduire au minimum le
risque d’incendie ou d’explosion ou pour
éviter tout dommage matériel, toute
blessure ou la mort.
—Ne pas entreposer ni utiliser d’essence
ni d’autres vapeurs ou liquides
inflammables à proximité de cet
appareil ou de tout autre appareil.
—QUE FAIRE SI VOUS SENTEZ UNE
ODEUR DE GAZ:
●
Ne pas tenter d’allumer d’appareils.
●
Ne touchez à aucun interrupteur. Ne
pas vous servir des téléphones se
trouvant dans le bâtiment.
●
Évacuez la pièce, le bâtiment ou la
zone.
●
Appelez immédiatement votre
fournisseur de gaz depuis un voisin.
Suivez les instructions du fournisseur.
●
Si vous ne pouvez rejoindre le
fournisseur de gaz, appelez le service
des incendies.
—L’installation et l’entretien doivent être
assurés par un installateur ou un
service d’entretien qualifié ou par le
fournisseur de gaz.
WARNING: For your safety the
information in this manual must be
followed to minimize the risk of fire or
explosion and to prevent property
damage, personal injury or death.
— Do not store or use gasoline or other
flammable vapors and liquids in the
vicinity of this or any other appliance.
— WHAT TO DO IF YOU SMELL GAS:
●
Do not try to light any appliance.
●
Do not touch any electrical switch;
do not use any phone in your
building.
●
Clear the room, building or area of
all occupants.
●
Immediately call your gas supplier
from a neighbor’s phone. Follow
the gas supplier’s instructions.
●
If you cannot reach your gas
supplier, call the fire department.
— Installation and service must be
performed by a qualified installer,
service agency or the gas supplier.
Summary of Contents for AD-320
Page 20: ...16 American Dryer Corp 112144 46 ...
Page 21: ...112144 46 www adclaundry com 17 ...
Page 22: ...18 American Dryer Corp 112144 46 ...