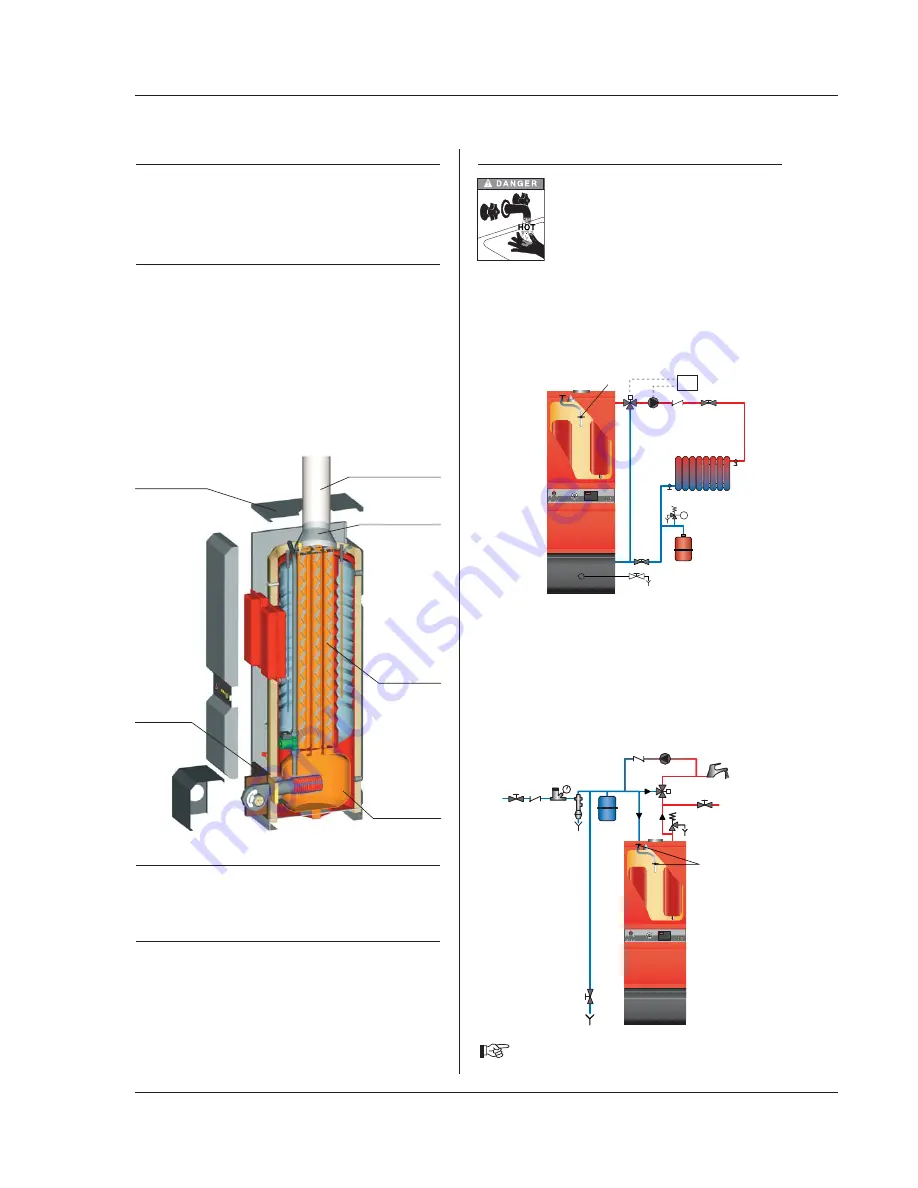
14
DRAINING THE BOILER
Water flowing out of the drain cock may be
extremely hot and could cause severe scalding.
Keep people away from discharges of hot
water.
Draining the heating circuit
1.
Turn OFF the on/off switch on the boiler control panel, isolate
external electrical supply, and turn off the gas supply to the boiler.
2.
Close the isolating valves (4).
3.
Connect a hose to the drain cock (7).
4.
Open the drain cock to drain the primary circuit.
Draining the hot water circuit
1.
Turn OFF the on/off switch on the boiler control panel, isolate
external electrical supply, and turn off the gas supply to the boiler.
2.
Release the pressure in the heating circuit until the pressure
gauge indicates zero bar.
3.
Close stop cock (1) and turn off tap (8).
4.
Open valve (9) then valve (10).
5.
Let the water empty into the drain
For the tank to be emptied, valve (9) must be situated
at ground level.
MAINTENANCE
SERVICE INTERVALS
ACV recommends that boilers should be serviced at least once a year.
The burner must be serviced and tested by a competent engineer.
If a boiler is subject to heavy use, it may require servicing more than
once a year - consult ACV for advice.
SERVICING THE BOILER
1.
Turn OFF the on/off switch on the boiler control panel and isolate
external electrical supply.
2.
Turn off the gas supply to the boiler.
3.
Remove the flue to gain access to the top of the boiler.
4.
Remove the casing top panel and lift off the flue reduction collar
by undoing the fastening bolts.
5.
Remove the turbulators from the flue pipes for cleaning.
6.
Unscrew the burner chamber plate and remove the burner.
7.
Brush the flue pipes .
8.
Clean the burner chamber and the burner.
9.
Re-assemble turbulators, flue reduction collar and flue, checking
that the gasket on the flue reduction collar is in good condition.
Replace gasket if necessary.
SERVICING THE SAFETY DEVICES
- Check that all thermostats and safety devices are working properly.
- Test the safety valves on the central heating and hot water circuits.
SERVICING THE BURNER
- Check that the insulation and gasket on the burner chamber plate
are in good condition - replace if necessary.
- Check and clean the burner and electrodes. Replace electrodes if
necessary
(under normal use once a year)
.
- Check that the safety components are working properly.
- Check the combustion (CO
2
, CO and gas pressure) and record
the values and any remarks in the Service Record on page 18.
1
2
3
4
5
2
6
7
8
9
10
12
11
1
4
2
6
4
3
5
9
8
7
Casing top panel
Chimney flue
Flue reduction collar
Burner chamber
Burner
chamber plate
Flue pipe and
turbulators