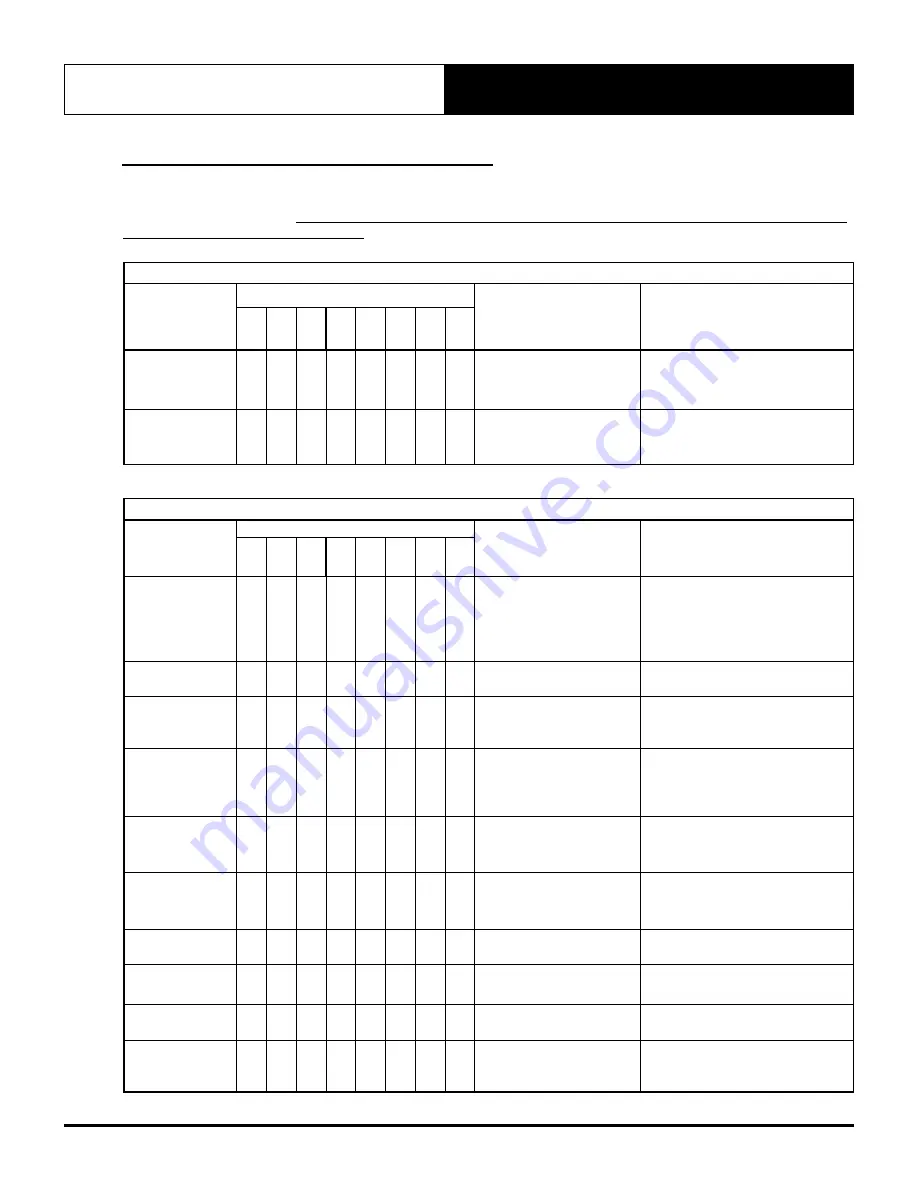
Installation and Commissioning Guide
Variable Capacity Commercial
21
Installation and Commissioning Guide - Split Ducted Variable Capacity Commercial Indoor Unit
Doc. No. 0525 - 068
Ver. 3 201104
14. Maintenance Frequency Checklist
Regular servicing of equipment by a qualified technician is recommended every 12 months for residential applications
and every quarter for commercial applications. Regular servicing of your unit helps in maintaining its optimum
performance and reliability.
The following checklist and service periods are provided as a guide only, as some sites
may require more frequent servicing.
ELECTRICAL
Parts
Service Period
Detail of Service Check
Service Methods
1
Mth
3
Mth
6
Mth
1
Yr
2
Yrs
3
Yrs
4
Yrs
5
Yrs
Isolators /
Printed Circuit
Boards
Visual Inspection
Tighten Terminals as necessary on
isolators and printed circuit boards
Electrical
Connections
Check all electrical
terminals, mains,
communications, etc
Re-tighten if loose.
INDOOR SECTION
Parts
Service Period
Detail of Service Check
Service Methods
1
Mth
3
Mth
6
Mth
1
Yr
2
Yrs
3
Yrs
4
Yrs
5
Yrs
Casing / Panels
and Frames
Visual check for
damage, rust and dust
accumulation.
For highly corrosive environment,
wash panels quarterly with water
and neutral detergent solution.
Wax panels. Repair / re-paint
where required.
Insulation
Visual check for insulation
conditions.
Repair / replace insulation material.
Fan
Visual check for run out of
balance and dust attached
Clean off dust as necessary to
negate possibility of fan running
out of balance
Motor
Ω
Visual check on wiring.
Insulation resistance check
to be carried out annually
Measure insulation resistance
to earth with insulation tester.
Insulation resistance should be
more than 1MΩ.
Heat
Exchanger
Check for clogging by
dust. Check for leaks /
damage.
Clean air inlet side as necessary.
Straighten any bent fins using fins
comb.
Drain Pan/
Condensation
line
Check for obstructions and
free flow of water
Clean to eliminate obstructions/
sludge and check condition of pan.
Pour water to ensure flow
Filter *
Check for clogging
by dust.
Clean Filter
Temperature
Readings
Measure air on
and air off
Place temperature probe in return
and supply air of unit.
Ducting
Inspect duct works for air
gaps
Re-tape any loose ducts.
Damper Motors
(If fitted)
Visual inspection of motors
open/closing. Ensure no
obstructions
Drive motors opened and closed.
Ensure correct operation.
*Service period for filter cleaning may vary depending on operating time and surrounding environment.