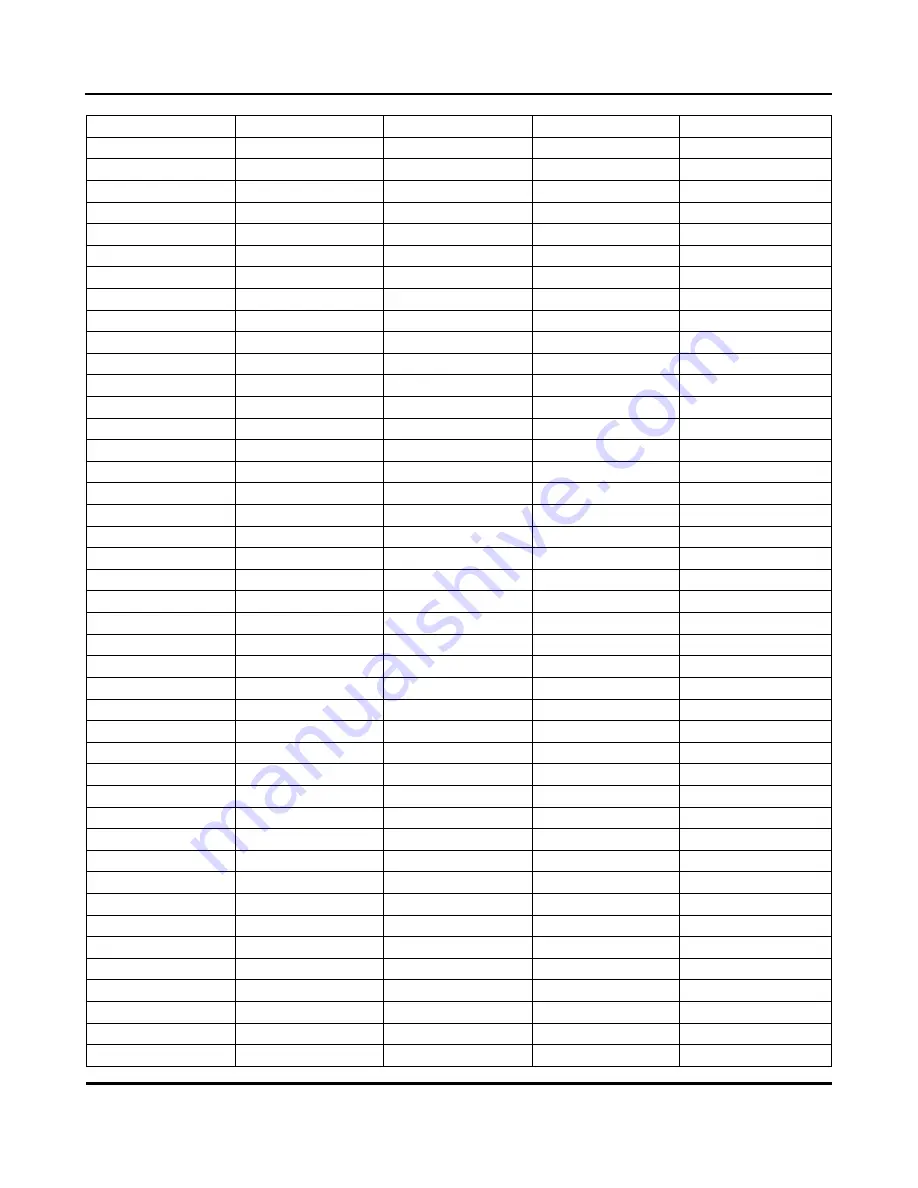
SERIES AP220 / AP231 ACROPACK
USER
’S MANUAL
Acromag, Inc. Tel: 248-295-0310
- 12 -
http://www.acromag.com
- 12 -
https://www.acromag.com
41
32
14
25
Signal Return
28
Reserved/isolation
27
Reserved/isolation
8
8
15
30
CH7+
42
33
16
29
Signal Return
32
Reserved/isolation
31
Reserved/isolation
9
9
17
34
CH8+
43
34
18
33
Signal Return
36
Reserved/isolation
35
Reserved/isolation
10
10
19
38
CH9+
44
35
20
37
Signal Return
40
Reserved/isolation
39
Reserved/isolation
11
11
21
42
CH10+
45
36
22
41
Signal Return
44
Reserved/isolation
43
Reserved/isolation
12
12
23
46
CH11+
46
37
24
45
Signal Return
48
Reserved/isolation
47
Reserved/isolation
13
13
25
50
CH12+
47
38
26
49
Signal Return
52
Reserved/isolation
51
Reserved/isolation
14
14
27
54
CH13+
48
39
28
53
Signal Return
56
Reserved/isolation
55
Reserved/isolation
15
15
29
58
CH14+
49
40
30
57
Signal Return
60
Reserved/isolation
59
Reserved/isolation
16
16
31
62
CH15+
50
41
32
61
Signal Return
64
Reserved/isolation
63
Reserved/isolation
17
17
33
66
51
42
34
65
68
Reserved/isolation
67
Reserved/isolation
18
18
35
70