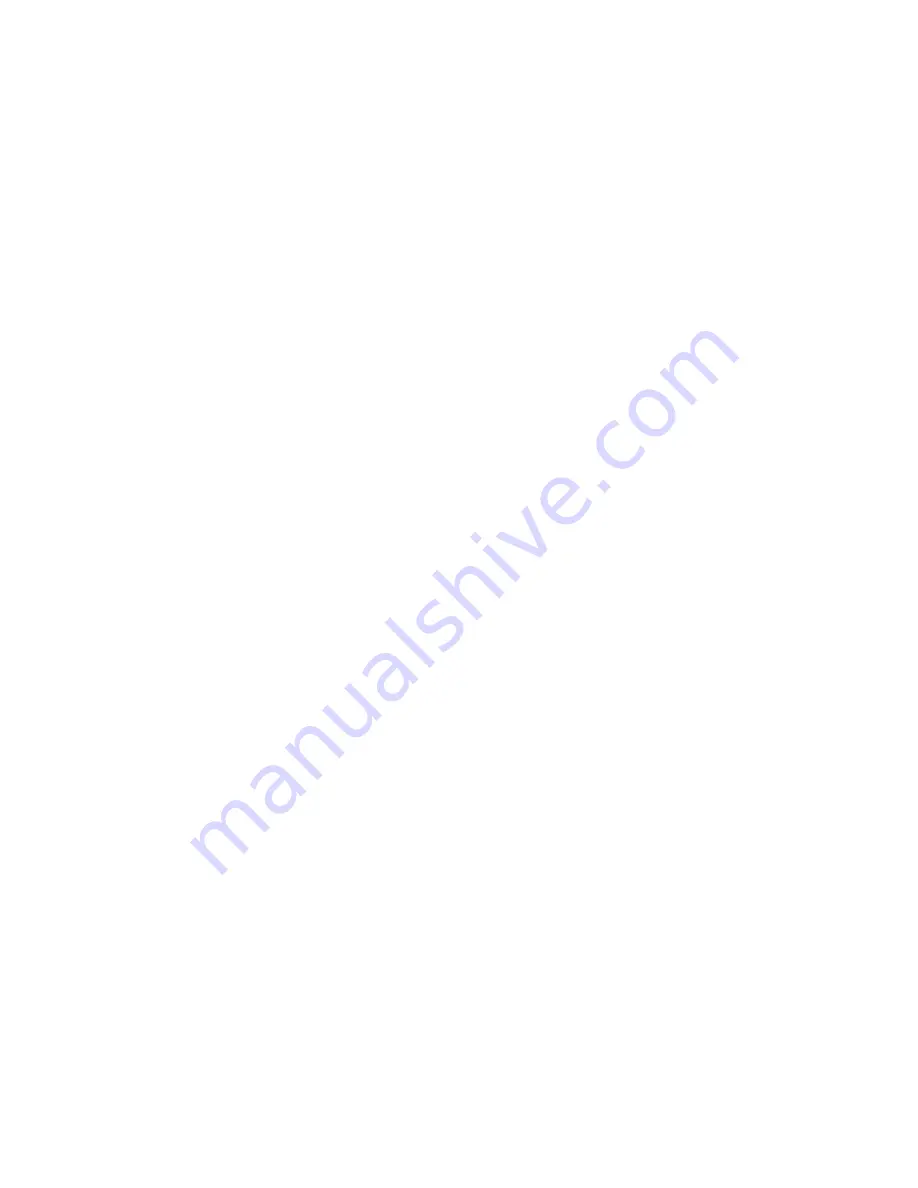
MP5032-2104
XLR8 HEATED PLATEN
19
3.5 CAST ELEMENT ELEMENT
1. Follow typical safety protocol for electrical and work space and tools. Lock out tag out.
2. Disconnect from power source.
3. Lower handle assembly.
4. Remove the controller cover
5. Disconnect Element wires from Control board and snip any wire ties that are binding the wires
together.
6. Loosely install controller cover assembly.
7. With one hand on the handle to prevent the arm assembly from rapidly lifting up, remove the
element cover 8-32 X 3/8” Truss head screws doing the ends first then finish in the center of
the element cover.
8. Slowly raise the arm assembly to its max height, leaving the lower half of the element assembly
laying on the griddle surface.
9. Carefully move the insulation away from the element.
10. Use a 1/4” socket wrench to remove the 6 nuts holding the element in place and lift the
element out.
11. Lay the replacement cast element on a table with the smooth shiny side up. Wipe the surface
clean and apply 1.5 - 2.0 ounces of heat transfer compound to the smooth side of the casting
using a putty knife.
12. Use the putty knife to spread the thermal compound across the entire surface of the cast
element.
13. When the surface is covered, hold the fine tooth comb (included with the kit) vertical and
draw it along the length of the element in several passes to obtain an even, uniform thickness
coating across the entire surface. After each pass, remove excess compound with the putty
knife. When finished it should look like an even surface containing fine lines of the compound.
If the lines of compound do not cover, add additional compound in those areas and repeat.
14. Set the element in place on the platen with the heat transfer paste in contact with the platen
bottom. Refer to drawing DEV002214-1 in the parts section of manual for orientation
guidance. Try not to get paste on the studs when putting the element in place. Center the
holes in the casting on the studs.
15. Place the large fender washers over the center studs.
16. Place a spring washer over each stud. Spring washers are conical shapedwashers that flatten
out as the nuts are tightened against them. The springwashers should point up like a miniature
volcano.
17. Install new nuts on the studs and hand tighten. Use an inch pound torquewrench and tighten
each nut to 37 inch pounds starting in the center, working first to the sides and then to the end.
Tighten twice in this manner. Do not over-tighten the nuts.
18. Reinstall overtemp switch on new element following instructions in 3.3.
19. Reverse procedure from step 7 to complete repair.
20.Use permanent lock-tite on the #8-32 element cover screws when reinstalling.