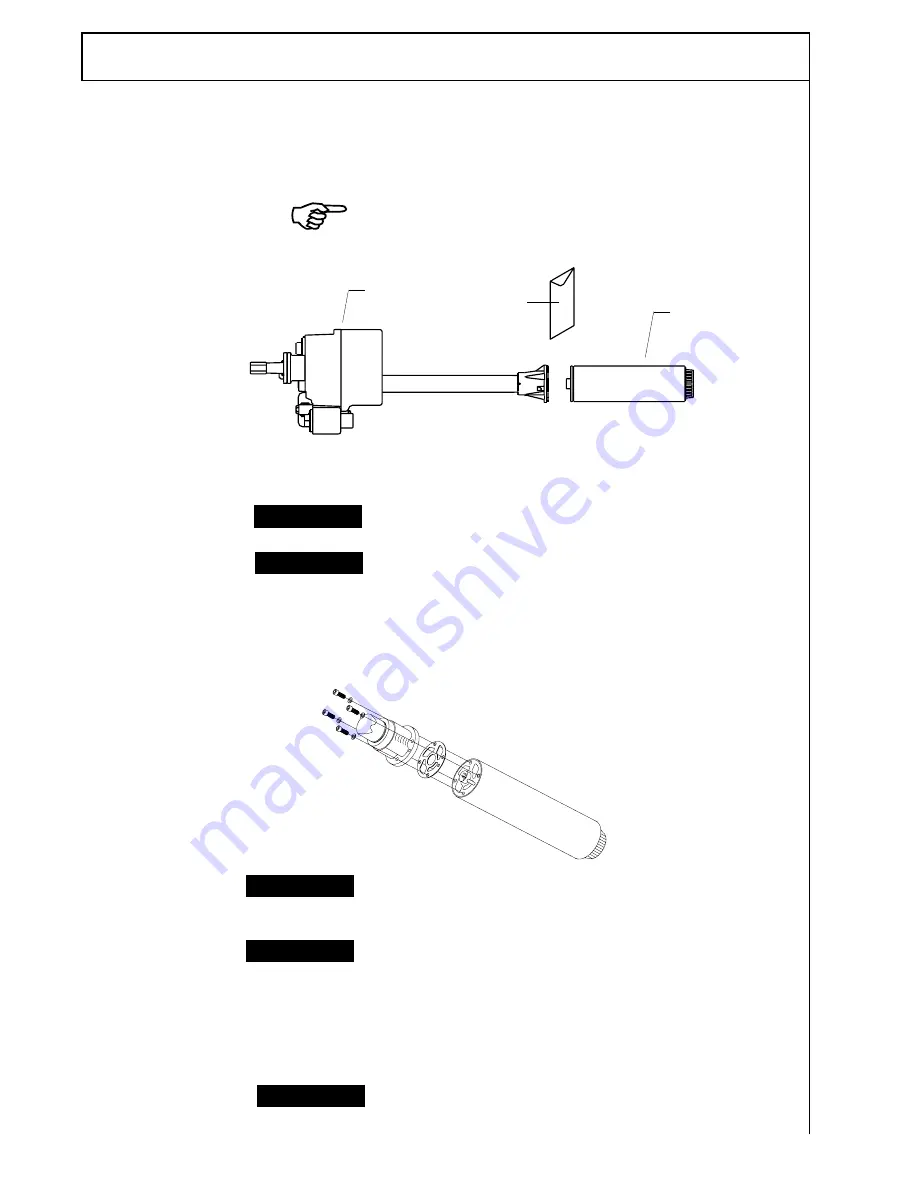
Figure 2.2 Aligning the gasket
PACKER/MANIFOLD
WITH PIPING
UMP
KIT (144-328-4)
Figure 2.1 Attaching the UMP
The attachment hardware kit to be used to connect the UMP to the Packer/Manifold
assembly piping consists of four Grade 8 5/16-18 socket head cap screws, four 5/16
spring lock washers, and one discharge head gasket. It is identified by the kit number
144-328-4 marked on the bag.
Suggested tools (non-sparking): 3/4” wrench, pipe wrench,
1/4” allen wrench, 9/16” wrench, screw driver, wire cutter and
wire stripper.
1:
Place the new gasket on the new UMP so that all the holes align.
Gaskets from competitive UMPS will not seal properly and
performance will be reduced.
Visually inspect the pigtail connector in the discharge head.
Replace if damaged. Be certain the indexing tab of the pigtail
is seated in the notch of the discharge head.
2:
Lubricate the o-ring and pigtail with petroleum based jelly.
3:
Align the UMP positioning dowel and boss with the proper holes in the discharge
head and push the UMP into position using hand force only. The UMP should be
snug against the discharge head prior to installing the UMP retaining bolts.
Use hand force to put the UMP on the discharge head. If the
UMP does not seat properly, snug against the discharge head,
remove the UMP and correct the problem.
Do not use the bolts to pull the UMP into position. Use the
cross pattern to snug and torque bolts. Do not over torque the
bolts. Not following these instructions may cause parts to fail.
4:
Install the UMP retaining bolts and lock washers. Snug and then torque the bolts
using a cross pattern. Torque to 7 ft-lb. (11 N•m).
I
NSTALLING THE
P
UMP
Red Jacket petroleum pumps are designed to operate in
Class 1, Group D locations.
NOTICE
NOTICE
NOTICE
— 10 —
4” Petroleum & AG
CAUTION
NOTICE
Summary of Contents for Red Jacket AGUMP33R1
Page 14: ...8 4 Petroleum AG...