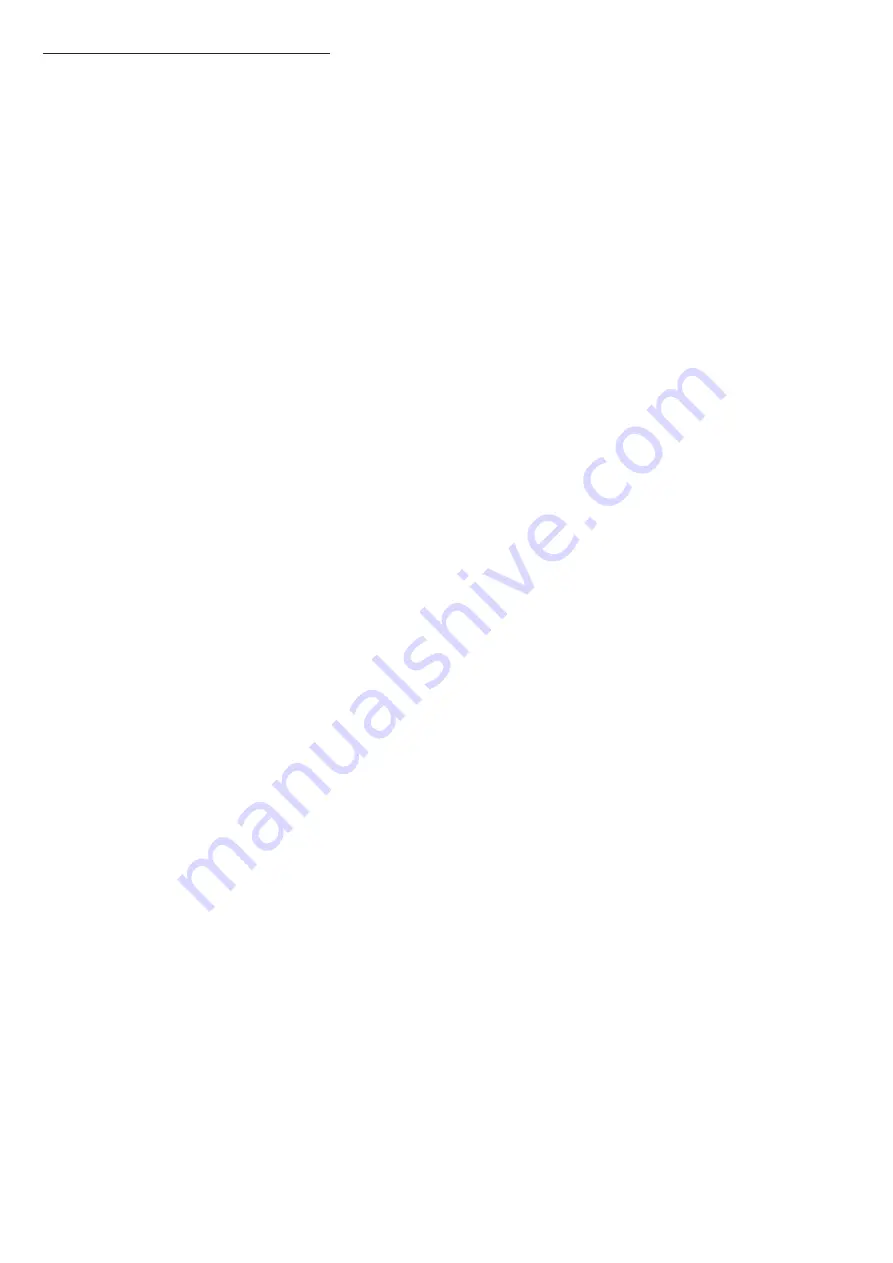
35
14. REPAIR - COMPONENTS REPLACEMENT
Specific technical expertise is required to work on the components
listed below and / or to replace them, so it is recommended that
you always contact an authorized Technical Assistance Center.
For safety and quality purposes it is recommended to use original
components and spare parts for replacements.
Always operate in conditions of maximum safety, in compliance
with current regulations on the subject. Before any intervention
on the appliance, disconnect the power supply by acting on the
main switch and then on the disconnector on the machine.
For any operations of emptying and charging of refrigerant gas,
it is recommended to use specific equipment for the recovery of
the refrigerant, in order to protect the environment.
14.1 REFRIGERANT CIRCUIT
For any reason it is necessary to repair the refrigerant circuit,
with consequent contamination, as in the case of burning of the
electrical windings of the compressor or failure of the circuit with
complete emptying, the following must always be carried out:
- circuit cleaning;
- drying and high vacuum;
- leak test and charge recovery.
14.2 DRYING AND VACUUM OF THE SYSTEM
Drying and high vacuum are necessary to evacuate the
air, humidity, and all gases that may be in solution with the
compressor oil.
If there is water in the liquid phase in the system, it is necessary
to slightly heat the parts in which it is deposited, in order to favor
evaporation.
The capacity of the high vacuum pump must be adequate for the
system in which it is to be operated; the use of a pump with a flow
rate of at least 90 liters / minute is recommended.
The degree of vacuum must be checked with a suitable vacuum
gauge for medium vacuum, possibly electronic, with resolution in
microns of the scale.
- Carrying out a high vacuum:
- connect the pump to the system by means of pipes,
connections from 1/4 SAE female swivel, to the pressure
points shown on the suction and delivery connections in the
compressor;
- connect a vacuum gauge
- vacuum up to a value of at least 350, 500 microns for a
minimum time of at least 30 minutes.
14.3 CLEANING THE CIRCUIT
ATTENTION!
If the motor burns, with perforation of the windings,
it is necessary to carefully clean the refrigerant circuit to avoid
subsequent burns or breakdowns.
Cleaning operations have the purpose of eliminating all carbon or
other solid state deposits and, according to the method used, all
contaminants that have been introduced for cleaning the circuit
or as a result of the operations performed must be eliminated.
ATTENTION!
Do not inhale refrigerant vapors from burnt
compressors, as toxic products may be present. Completely
avoid contact with the skin of the residual oil from the burnt
compressor.
14.4 REFRIGERANT CHARGE
ATTENTION!
The refrigerant gas in the liquid state must not be
charged in suction on the compressor as this condition causes
damage to the compressor.
The operations to be carried out are as follows:
- connect the cylinder (or the charging cylinder) to the system
by means of pipes and 1/4 SAE female swiveling connections
to the pressure point on the liquid side of the air / gas
exchangers refrigerant;
- insert refrigerant in the liquid state:
a) until the necessary office is reached;
b) until the balance of pressures between cylinder and
refrigerant circuit;
- start the appliance and, if necessary, insert the refrigerant
remaining until the prescribed values are reached.
The charge setup operation must be done using the suction
socket of the compressor, by inserting the liquid refrigerant
gradually;
- check the refrigerant charge.
ATTENTION!
Make sure that the instruments used are in good
condition and properly calibrated.
14.5 CHECK OF OVERHEATING
- start the appliance;
- insert into the pressure point, positioned in the large tube
near the compressor, the low pressure gauge for the
pressure measurement;
- wait for the values to stabilize for about 20 minutes;
- measure the temperature value on the large tube (phase
steam), near the pressure point using
a special contact probe;
- read the temperature value in the pressure gauge, in
correspondence with the detected pressure value.
The temperature read on the thermometer must be greater
than the temperature read on the pressure gauge by a value
between 3 °C and 8 °C for operation in cooling mode, between
1 °C and 5 °C for operation in heating mode.
Summary of Contents for HUB RADIATOR MINI 11.0
Page 27: ...27 7 2 WIRING DIAGRAM HUB RADIATOR MINI XL 6 0...
Page 28: ...28 7 3 WIRING DIAGRAM HUB RADIATOR MINI XL 8 0...
Page 29: ...29 7 4 WIRING DIAGRAM HUB RADIATOR MINI XL 11 0...
Page 30: ...30 7 5 WIRING DIAGRAM HUB RADIATOR MINI XL 16 0...
Page 31: ...31 Marrone Nero Blu 7 6 WIRING DIAGRAM HUB RADIATOR MINI XL 24 0...
Page 46: ...46...