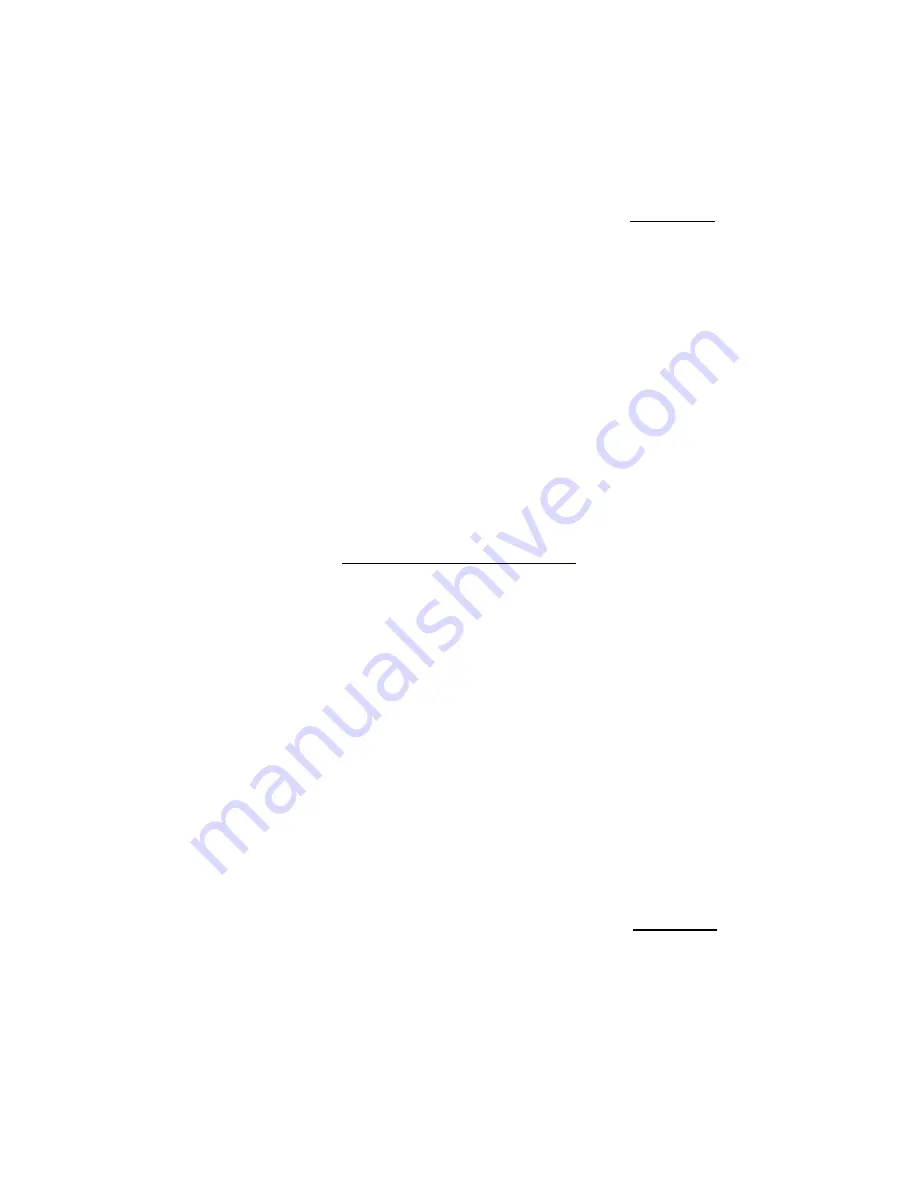
- 9 -
PRE-OPERATION CHECKS (Mechanical)
A - Gear reducer lubricant level.
B - Lubricant on gear reducer drive chain.
C - Final check all bolted or assembled components.
PRELIMINARY TEST
Prior to final wiring connection of Radio Decoder, Timer or
Telephone Relays and with power connected to the starter
controls, a check for proper motor rotation MUST be made.
1.
Have one person observe the open siren air intake.
2.
Momentarily energize the motor through the magnetic
starter contacts. Siren motor rotation should be
counterclockwise. If rotation is not correct, interchange line
one and line three on a three-phase siren.
FINAL WIRING AND TESTING (See Figures 11 through 14
and refer to wiring diagrams)
Connect the signal source wires to the magnetic starter control cabinet
terminal block. Proceed to test the entire operation of the siren using
the radio controls, timer or telephone system.
CAUTION
WEAR EAR PROTECTION. With the installation complete, the
siren SHOULD NOT BE ALLOWED TO SOUND FOR ANY
PROLONGED PERIOD (more than 30 seconds) while any person is
on the same level as the horn. Ear guards must be worn by personnel
on the same level as the horn as a precaution at all times during testing
or possible remote starting.
OPERATION
Actuation and control may be by means of remote direct-wired lines,
telephone lines and relays or special radio controls. The activating
and timing equipment, to be provided at time of installation, must be
specified when ordering the siren. This manual will not attempt to
define the exact operational procedure of the siren.
MAINTENANCE INSTRUCTIONS
LUBRICATION (See Figures 10 and 11)
NOTE
DISCONNECT POWER FIRST.
1.
A self-aligning ball bearing is installed above the collector ring
assembly. This bearing is sealed for lifetime use and no additional
lubrication is necessary.
2.
Another self-aligning ball bearing is installed under the base in the
center of the assembly. This bearing has an external grease fitting and
has been lubricated at the factory so no additional lubricant is necessary
for one year. When greased, one shot of the grease gun is sufficient. If
excess flows from the seals, remove it from inside the base with a rag.
Use Molub Alloy #171 graphite grease manufactured by the Imperial
Oil and Grease Co. or equivalent.
3.
Oil in the gear reducer should be changed each year. Use high quality
SAE IOW-30 Motor oil and fill to oil level hole.
4.
Before operating, check drive chain under circular base for protective
grease coating. If needed, grease with Molub Alloy #171 graphite
grease or equivalent. Do not over-grease. Check the setscrews in the
sprockets, collars and couplings when greasing the chain.
ADJUSTING DRIVE CHAIN TENSION
The rotation drive assembly is factory adjusted to provide slippage as a
precaution against possible component damage if a physical force prevents the
siren assembly from rotating. A torque adjustment is provided. (See Figure
11.) A quick torque check may be made by grasping the upper siren assembly
with both hands and attempting to rotate. Considerable force should be
required to rotate manually. If adjustment is necessary, turn the torque
adjustment nut to increase compression of spring.
CLEANING COLLECTOR RINGS
If the siren is inoperative and all electrical connections such as fuses,
overloads in the magnetic starter and circuits have been checked, inspect the
collector rings in the rotation assembly by removing the fiberglass hood. (See
Figure 11.)
CAUTION
Make certain the electrical power is off.
If the collector rings are discolored or have a dirt or oil film coating, polish
each ring with a fine crocus cloth. This can be accomplished by polishing the
portion of the ring near the opening, and then rotating the assembly by hand
far enough to expose another portion of the collector ring. Also check the
triggers on the brush holders to see if there is sufficient pressure on each brush
to maintain contact.