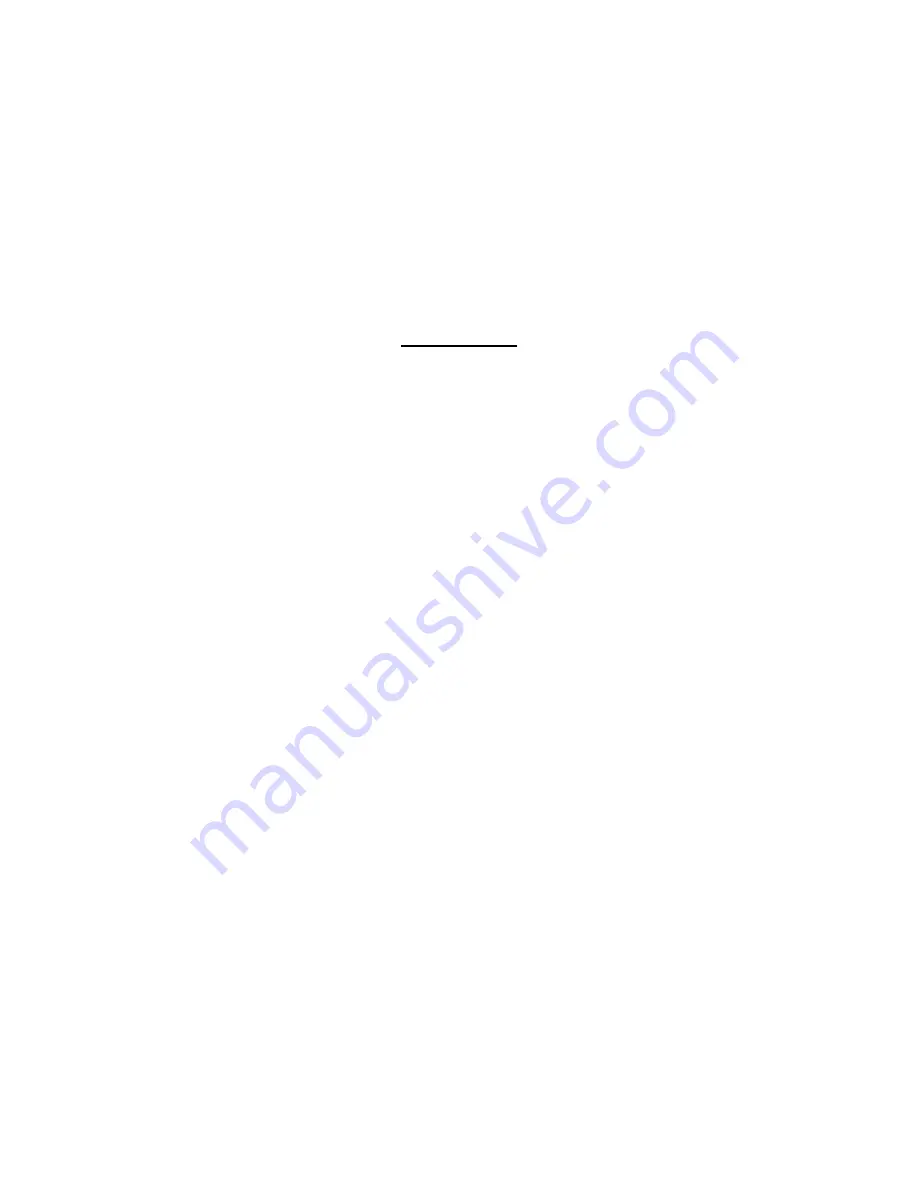
- 4 -
TOOLS AND TEST EQUIPMENT
Ordinary mechanics' tools and electrical tools are suitable for
installation of the siren assembly.
No test equipment is required for installation, except that it may be
desirable to have available an AC voltmeter or voltage indicating
device.
WARRANTY AND SERVICE
See separate warranty statement.
SAFETY PRECAUTIONS
LIFTING THE SIREN - Use a lifting device of adequate capacity.
Do not use the eyebolt for lifting if a pole or other mount is attached
to the siren. (See other information on lifting under heading
INSTALLATION.)
ELECTRICAL - During installation, prewire completely before
connecting to power source. Always disconnect from power source
before beginning any service or maintenance procedures. Only
qualified personnel should open the electrical control panel cabinet.
Refer to wiring diagrams and observe proper wiring procedures
during installation.
TESTING - CAUTION: Wear ear protectors! Anyone on the same
level- as or very close to the siren should wear ear protection during
operational tests. Prolonged exposure can cause ear damage.
INSTALLATION
GENERAL
To insure satisfactory operation, careful consideration must be given to
each of these factors:
1 - Site selection for optimum signal coverage
2 - Type of mounting
3 - Power supply requirements
4 - Provision for servicing
SITE SELECTION AND TYPES OF MOUNTING
Careful consideration must be given in selecting a site or sites for
installation. Locations should be plotted on local area maps to provide
the desired coverage. Generally, the highest possible site in the
selected area is the best location. This might be a building, tower or a
hill. Do not mount siren too high so that the sound goes over the top of
the area.
In lieu of a suitable existing structure for mounting, a cedar pole
approximately 40-50 feet long and sunk 8 feet deep is a generally
recommended mount. Refer to the illustrated mounting layouts for
details. Any tall building, trees, hills or other obstructions will tend to
create a barrier, which will produce a deadened area behind the
obstruction.
Figures I through 4 and 7 illustrate typical siren mounting
arrangements, which have been used successfully. These are Roof
Mount, Parapet Mount, Chimney Mount, Tower or Tank Mount and
Pole Mount. Figures 5, 6 and 8 show details of suggested supports and
platforms as well as erecting details.
Another general mounting recommendation that may be helpful is the
following: Determine the height of any building or obstruction within
150 feet of the siren. Keep the siren horn at least 5 feet higher than the
obstruction for best sound coverage. Remember that a siren
mounted too high will beam the sound over the top of the
required area.
ELECTRICAL POWER REQUIREMENTS
Adequate electrical power must be available at each siren site
(see
SPECIFICATIONS
for requirements). Local power
companies will charge extra if the siren is located more than 75
feet from the transformer.
NOTE
Line voltage fluctuations must not exceed ±10 percent
for specified performance (NEMA standard).
PROVISION FOR SERVICING
A convenient means of working on the siren for periodic
servicing must be provided at time of installation. When using a
pole mount, a platform should be constructed at the proper work
level. Refer to Figures 6 and 7 for platform suggestions.
If rungs or steps are provided for climbing up to a platform, it is
advisable to locate the lowest step at least 10 feet above the
ground to minimize the opportunity for vandalism.