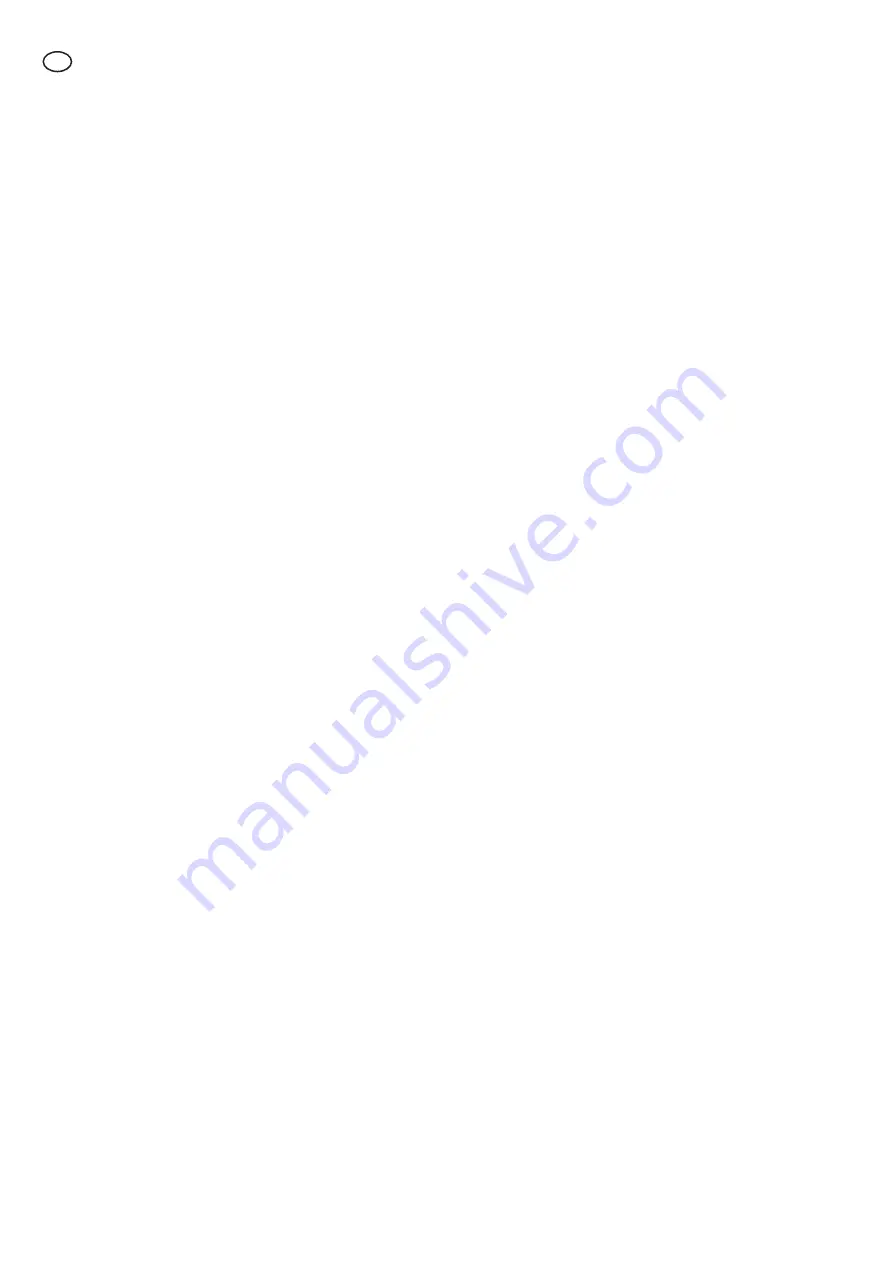
SD20PHL-A / SD26PHL-A
WARNING -
safe usage instructions
1.
The jacking beam is only to be mounted on lifts
approved by the lift manufacturer for mounting of jacking
beams - be aware that not all lifts are approved. Rated
beam capacity shall be max. 2/3 of vehicle lift capacity.
2.
Mount the jacking beam with adequate support arms on
horizontal, parallel and solid rails and secure it against
crashing before use. See paragraph “Assembly Instruc-
tions for Support Arms”.
3.
Study, understand and follow all instructions before
operating this jack.
4.
Check before each lift, that the support arms are
correctly placed on lift rail or pit edge.
5.
Lifting device only. Do not move or transport the vehicle
with jacking beam.
6.
Immediately after lifting, support the vehicle with support
stands.
7.
Do not exceed rated capacity.
8.
Lift only on points as specified by automaker, and only
centrally on lifting saddles. Be attentive that the saddles
cannot slide
9.
If lifting the complete vehicle on 2 jacking beams they
shall be placed minimum 0,85 m from each other.
10.
Gravity of load must always be placed centrally. When
lifting on one point only, always lift on the centre of the
beam. Never lift on one extension arm only.
11.
It is recommended to brake and chock the vehicle.
12.
No person shall remain in, on, or get bodily under a load
that is being jacked or is supported only by a jacking
beam.
13.
The operator must observe, that beam can be operated
without any danger to himself or others. Only operate
the beam when beam and vehicle can be fully observed.
14.
Only use original accessories and spare parts.
15.
This beam - including the safety valve - is not to be
altered.
16.
Maximum air-pressure: 12 bar. Full capacity from 8,5
bar.
17.
Failure to follow these warnings may result in personal
injury and/or property damage.
Assembly
Please refer to paragraph “Assembly Instructions for Support
Arms” on previous pages.
Mount box for remote control where both jacking beam and
vehicle can be fully observed. On a 4-post lift we recommend
to mount the box next to the lift controls.
Connect air-supply to box for remote control, ¼” WRG: 8,5
- 12 bar, min. 500 l/min.
The two air hoses coming from the box are to be installed
inside the lift, protected against pinching and wear. Connect
the hoses to the rear side of jacking beam by the attached
quick couplungs: Air for controls through right Ø6 fitting (30),
air supply for air-motor through left Ø8 fitting (23).
GB
Use
Positioning of extension arms:
Each extension arm is
controlled by a joystick. The speed can be adjusted by the 4
valves 0200047: First valve for right in, then right out, left in
and last left out.
Lifting:
Turn left handle clockwise.
Remote controlled lowering:
Observe jacking beam and
vehicle and make sure that there is no danger for anyone
– then push the knob. The unloaded extension arms are
automatically retracted, when the beam reaches the level,
where valve (6) is activated. Please notice that the “return-
level” can be changed by adjusting valve position.
Manual lowering:
Turn both handles counter clockwise. The
unloaded extension arms returns automatically.
Noise emision:
The A-weighted sound pressure level is
max. 85 dB(A).
Maintenance
Maintenance and repairs must always be carried out by
qualified personnel. The air-hydraulic pump needs oil for lub
-
rication of the mechanical parts. It is recommended to install
water separator/filter and oil lubricator close to the jacking
beam.
Daily:
Inspect jacking beam and supports for damages, and
that the supports are safely positioned on the lift. Clean the
extension arms in order not to hinder the automatic retrac-
tion.
Monthly:
Lubricate all mechanical parts with oil. On the air-
supply empty the water separator/filter and refill the oil-lubri
-
cator with a thin oil.
Oil refill:
Lift to maximum height without load and remove
filler plug (24). Correct oil level is up to lower edge of filling
hole.
Warning:
Do not operate the beam without filler plug
(the oil reservoir will be pressurized).
Oil quantity:
0,6 l.
Any good hydraulic oil of viscosity ISO VG 15 can be used.
Never use brake fluid!
Safety Inspection
According to national legislation - minimum once a year
though - the beam must be inspected by a professional:
Supports/support arms and their suspension on the lift;
safety against crashing; damages; wear and tear; hydraulic
unit for leakages.
Possible faults and how to overcome them
1.
The jacking beam cannot lift to maximum height: Refill
with oil (see “Maintenance”).
2.
The beam does not lift full capacity: Check that release
handle is on “neutral” and can move freely. Also check
the air supply: minimum 8,5 bar and 500 l/min.
3.
The beam does not lower to minimum position: Check for
damages and items in the bottom of the beam; lubricate
all moving parts.
4.
The beam continues to lower after letting go of the
release handle: Ventilate the hydraulic cylinder by screw
(10).
Warning:
The beam must be unloaded!
5.
The load is dropping: Leaking pump valves in the pump.
Change valve cores and seals.
6.
The cylinder is leaking: Exchange worn seals.
Spare parts
Replace worn or broken parts with genuine jack manufactu-
rer supplied parts only. All major parts may not be provided
after discontinuation of a model.
Destruction
Oil must be drained off and legally disposed of.
(Translation of original text)