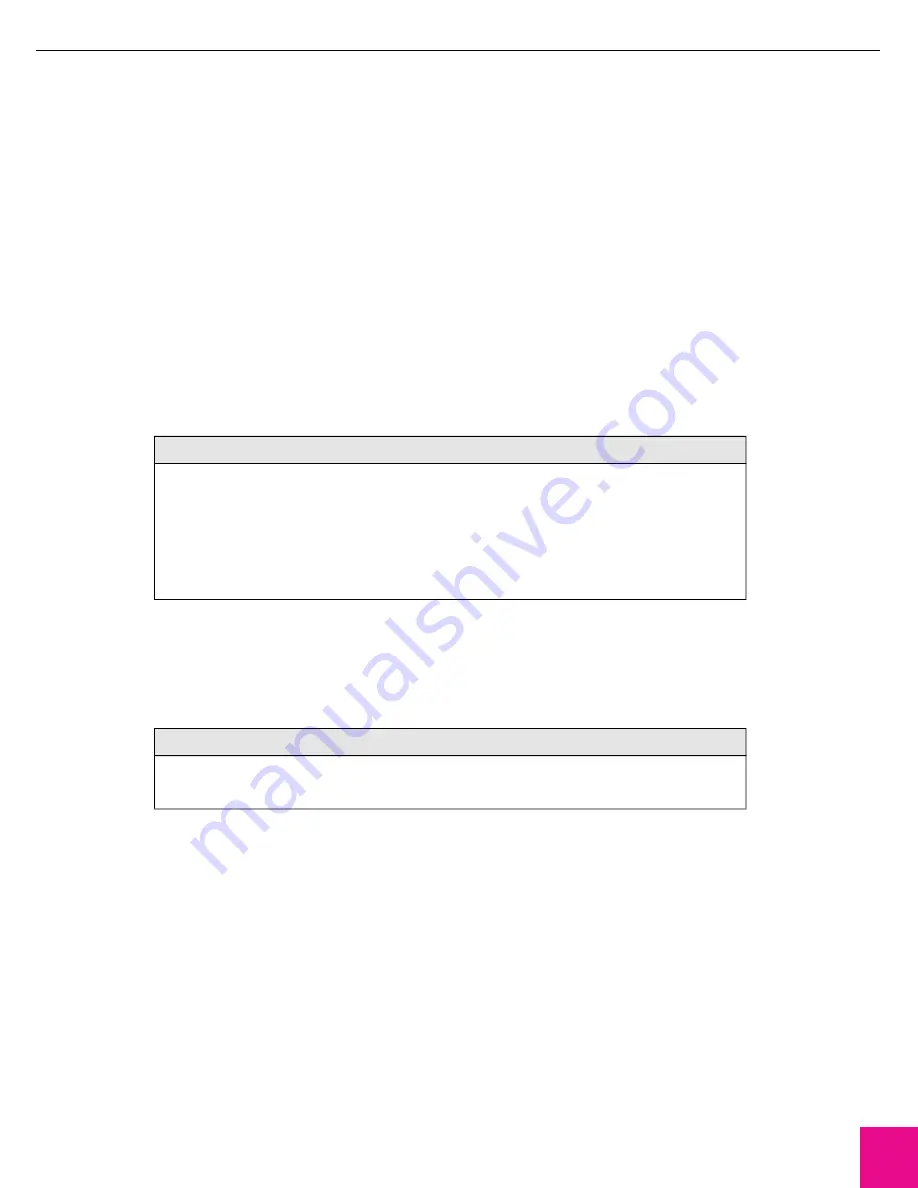
6
Putting into operation
6.
4 Setting the shielding gas volume
Fig. 5
Setting up the cable assembly on page
EN
-
1
3
Check once again whether the wire guide has been fitted correctly.
Join the
power pin
(
6
)
to
the wire feeder
.
6.3 Attaching the machine-side connector
1
Connect the shielding gas cylinder to the wire feeder.
2
Set the gas quantity on the shielding gas cylinder’s pressure reducer.
6.
5
Introducing the wire
1
Insert the wire in the wire feeder as specified by the manufacturer.
2
Press the
‘zero-current wire feed’ button on the wire feeder.
NOTICE
• The type and amount of shielding gas used depend on the welding task and the gas
nozzle geometry.
• To prevent the shielding gas supply from becoming clogged by impurities, briefly open
the cylinder valve
before connecting the cylinder. This will expel any impurities that may
be present.
• Make all shielding gas connections gas-tight.
NOTICE
• Each time the wire is replaced, ensure that the start of the wire is free of burrs and not
bent.
EN
14
xFUME
®
ABIROB
®
A
F500