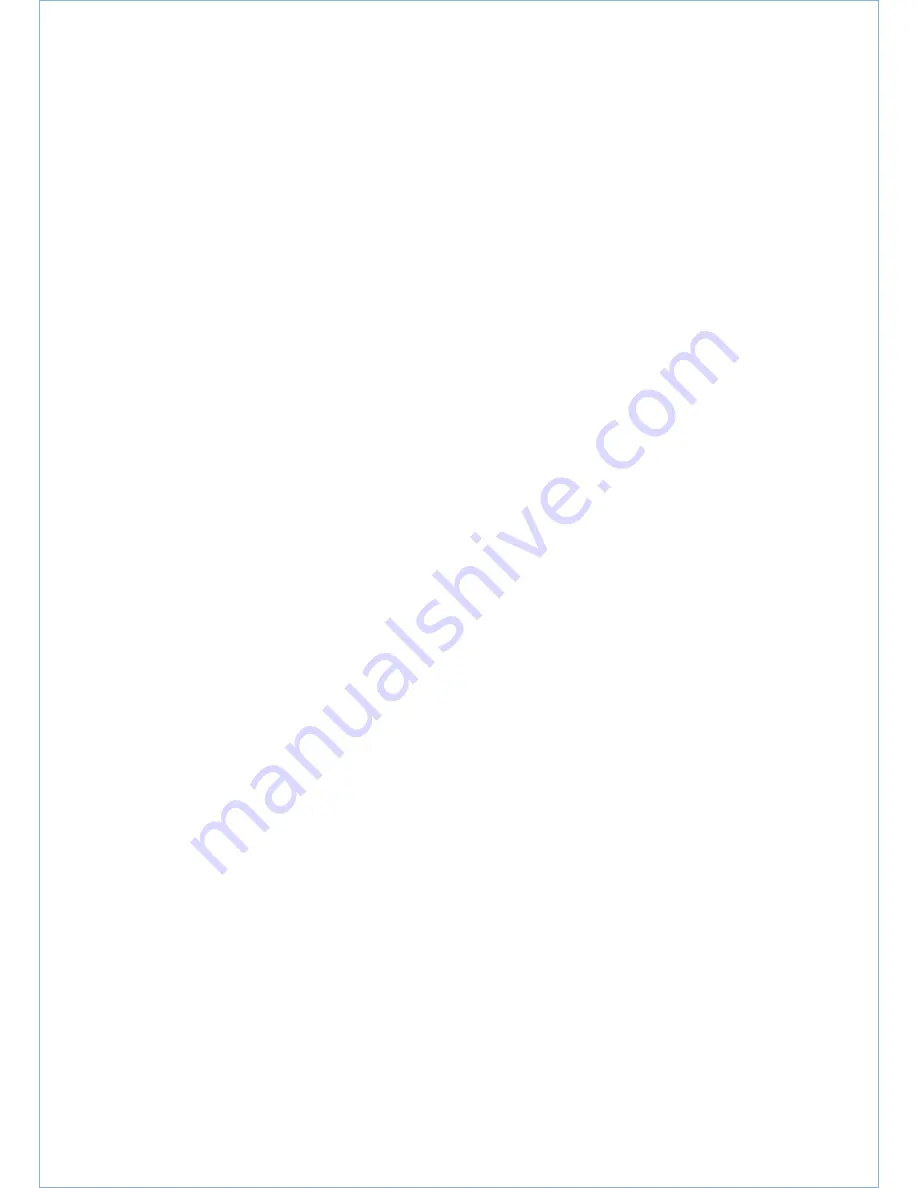
8
UniGear ZS3.2
I N S T R U C T I O N M A N U A L
—
3 Switchgear panel structure and
equipment installed
3.1 Basic structure and variants
(Figures 3/1 to 3/6)
The basic structure of the switchgear panels
comprises the panel itself, which is fixed in
position, and the movable, withdrawable part
with vacuum circuit-breaker. Figures 3/1 to 3/6
show the structure of a panel and the electrical
equipment fitted. The whole panel is constructed
by bolting up the double folded components
manufactured from high quality Al-Zn sheet steel,
precisely folded and exactly fitted surface from
and extremely rigid construction. Illustration
shows the structure of a panel and the electrical
equipment fitted. Together with the basic panel
version for use as an incoming or outgoing
feeder panel, variants, for example for busbar
sectionalizing (in conjunction with a bus riser
panel) or metering, are available. Further details
on the structure and equipment configuration
of the switchgears can be taken from the order
documents for the particular case.
The panel consists of the following components
•
Circuit-breaker compartment
•
Busbar compartment
•
Cable connection compartment
•
Low voltage compartment
The compartments are seperated from each other
by earthed sheet steel partitions.
3.2 Enclosure and partitions
(Figures 3/1 to 3/6)
The enclosure and internal partitions of the
switchgear panels consist of high quality
aluminium zink coated sheet steel. The three
high-voltage compart-ments are fitted with
secured pressure relief plates located at the
top. These open upward if internal arc faults
result in overpressure. The front and rear of the
panels is closed off by flameproof doors which
open to an angle of almost 180°. Neighbouring
switchgear panels are partitioned from one
another by the side walls of each panel and the
air cushion which remains between these walls
as a result of the design when the panels are
joined together. This method of construction
prevents them from melting through if an arc
fault should occur. All heads of the structure
bolts do not stick up the fitting surface on the
side walls as result of embossing processing used.
Thanks to that, it is possible to remove the middle
panel of the switchgear without removing the
adjacent panels. The separately fitted low-voltage
compartment B is designed as a self-supporting
shockproof and flameproof sheet steel enclosure,
separate from the high-voltage area. Even with
the withdrawable part 50 removed (hinged
shutters 35.1/ 35.2 in the closed position), there
is protection against contact with live parts in
busbar compartment C and cable connection
compartment D.
The necessary safety measures to counteract the
effects of an internal arc fault must be ensured
in connection with the ceiling height. This may in
individual cases possibly necessitate additional
operator protection measures on the switchgear
panels.
The front and rear doors of the switchgear panels
and the cover plates of the end panels are
thoroughly cleaned, treated to prevent corrosion,
and then painted with a high-quality twocoat
stoved enamel system in colour RAL7035 (or
special colours as agreed) which are notable
after stoving for their particular insensitivity to
impacts and corrosion.
3.3 Compartments in the switchgear panels
Circuit-breaker compartment
(Figures 3/6, 3/9 to 3/13)
The circuit-breaker compartment A fitted with
the necessary guide rails accommodates the
withdrawable part 50, which can be moved
between the service position and the test/
disconnected position.
If the withdrawable part is moved from the
service position into the test/disconnected
position, the fixed contacts 25.1 located in the
connection block 20.1/20.2 in busbar compartment
C and cable connection compartment D are
automatically covered by metal plates which will
be interlocked mechanically or can be locked by
a padlock when the withdrawable part is moved
away. In the test/ disconnected position, the
withdrawable part is still completely inside the
panel with the door closed.
The switching operations (including manual
operation) are carried out with the doors closed.
Withdrawable part
(Figures 3/1, 3/2, 3/14, 3/15, 3/16, 3/17, 6/1 to 6/7)
The manually moved withdrawable part consists
of a robust sheet steel structure on which the
circuit-breaker poles are mounted and the breaker
mechanism with anciallary components are
installed.
Contact arms 57.1/57.2 with spring-loaded contact
systems are fitted to the circuit-breaker poles.
These create the electrical connection to the
switchgear panel when the withdrawable part
is inserted into the service position. Detail
information on the vacuum circuit-breaker can
be found in the corresponding instruction manual.
The signalling, protection and control wiring
between the switchgear panel and the
withdrawable part is coupled by a multiple pin
control wiring plug connector 10.
As soon as withdrawable part 50 has been slid
into the switchgear panel and its interlock yoke
51 has engaged in the test/disconnected position,
it is positively connected to the switchgear panel.
At the same time, it is earthed by earthing
contacts 50.1 and earthing rail 19/19.1. The
position of the withdrawable part can be checked
on the electrical position indicator or through
the sight glass in the door at any time. The stored-
energy spring mechanism of the circuit-breaker
including controls and indicators is accessible at
the front of the withdrawable part. Apart from the
version with a fitted circuit-breaker, withdrawable
parts with other equipment, e.g. for metering,
are available.
Busbar compartment
(Figures 3/6, 5/7 to 5/17)
Busbars 3 are laid in sections from panel to panel,
and are held in place by the tee-off conductors
3.1 and by busbar bushings 29. The conductor
material used is tubing with a D-shaped
cross-section, in either single or double
configuration depending on the current rating,
or rectangle copper bar. The connection to the
flat tee-off conductors is made without any
special connecting clamps. The busbars and
tee-off conductors are covered with shrink-on
sleeves. The bolt connections in the busbar
system are normally covered by insulating covers
58. In conjunction with bushings 29, panel by panel
partitioning is realised.
Cable connection compartment
(Figures 3/6, 5/5, 5/6, 6/10 to 6/12)
Current transformers and an earthing switch (with
manual operating mechanisms) are located here.
Installation of surge arrestors is possible. Multiple
parallel power cables can also be entered without
difficulty. The cable sealing ends 16 can be fitted
in particularly favourable conditions. A removeable
plate for cable glands is located in the cable
entry area.
Installation of voltage transformers at cable
side of the panel is in preparation and will have
influence on the depth of the panel.
The earthing switch is designed with a making
capacity of 80 kA.
The detailed information on the earthing switch
can be found in the corresponding instruction
manual.
Low-voltage compartment
(Figures 3/6)
The low-voltage compartment, together with
its front door, accommodates the secondary
equipment of the switchgear panel required for
the particular application.
The control wiring in the switchgear panel area
is led through generously dimensioned and metal
covered ducts. The lefthand duct is reserved for
the incoming and outgoing control wires, and
the internal wiring in the panel is located on the
righthand side.
At the top of the left hand duct, an entry for
control cables is reserved with the free-cut rubber
sealing which will keep the protection class IP4X
for the whole encloser of the switchgear panel.
3.4 Interlocks/protection against maloperation
(Figures 3/6, 3/10 to 3/12, 6/1 to 6/8)
A series of interlocks are provided to prevent
fundamentally hazardous situations and
maloperation, thus protecting both personnel
and the switchgear itself. The interlocks which
are normally individually effective are as follows:
•
The withdrawable part can only be moved from
the test/disconnected position into the service
position (and back) with the circuit-breaker
open and the earthing switch open (between
positions, the circuit-breaker is mechanically
interlocked, and also electrically interlocked in
the case of circuit-breakers with electrical
releases)
•
The circuit-breaker can only be closed when the
withdrawable part is precisely in the defined
test position or service position. Between these
positions, the circuit-breaker is mechanically
interlocked, and also electrically interlocked in
the case of circuit-breakers with electrical
releases
•
The circuit-breaker can only be opened manually
in the service or test position when no control
voltage is applied, and cannot be closed
(electro-mechanical interlock)
•
Low-voltage plug 10.2 can only be inserted or
removed when the withdrawable part is in the
test/disconnected position
•
Earthing switch 6 can only be closed when the
withdrawable part is in the test/disconnected
position or the removed position (mechanical
interlock)
•
The withdrawable part cannot be moved from
the test/disconnected position into the service
position when the earthing switch is closed
(mechanical interlock)
•
Details of any additional interlocks, e.g. in
connection with a blocking magnet on the
withdrawable part and/or earthing switch
operating mechanism, can be found in the
order documents for each individual case (see
also section 7.4)
•
The hinged shutters can be secured with padlocks
in the closed position when the withdrawable
part has been removed (Figure 3/9)
3.5 Main apparatuses
3.5.1 Circuit breaker
Vacuum circuit breaker VD4
The vacuum circuit breaker of type VD4 on
withdrawable parts for 36/40.5 kV rated voltage
are intended for indoor installation in air-insulated
switchgear systems. Their switching capacity is
sufficient to handle any conditions arising from
switching of equipment and system components
under normal operating and fault conditions,
particularly short-circuits,within the parameters
of their technical data.
Vacuum circuit breakers have particular
ad-switching frequency in the working current
range and/or where a certain number of short-
circuit breaking operations are expected. Type
VD4 vacuum circuit breakers are suitable for
autoreclosing, and have exceptionally high
operating reliability and long life.
The vacuum circuit breakers designed in column
form, are supplied as withdrawable modules.
SF
6
circuit breaker HD4
HD4 medium voltage circuit-breakers use sulphur
hexafluoride gas (SF
6
) to extinguish the electric
arc and as the insulating medium.
SF
6
has smooth breaking characteristics, therefore
breaking in SF
6
gas takes place without any arc
chopping and without generation of overvoltages.
These characteristics ensure long electrical life
of the circuit breaker and limited dynamic,
dielectric and thermal stresses on the installation.
The circuit-breaker poles, which make up the
breaking part, are systems with lifelong sealed
pressure and are maintenance-free.
The ESH type mechanical operating mechanism
of HD4, with stored energy has free release and
allows opening and closing operations
independently of the operator’s actions.
The operating mechanism and the poles are
fixed to the metal structure which also acts as a
support for the kinetics for operating the moving
contacts.
Circuit-breakers in the withdrawable version are
fitted with a truck to allow racking in and racking
out of the switchboard or enclosure.
The light and compact structure of the circuit-
breaker ensures great sturdiness and excellent
mechanical reliability.
Summary of Contents for UniGear ZS3.2
Page 2: ......
Page 12: ...12 UniGear ZS3 2 INSTRUCTION MANUAL 3 5 UniGear ZS3 2 front view 3 5 ...
Page 45: ......
Page 46: ......
Page 47: ......