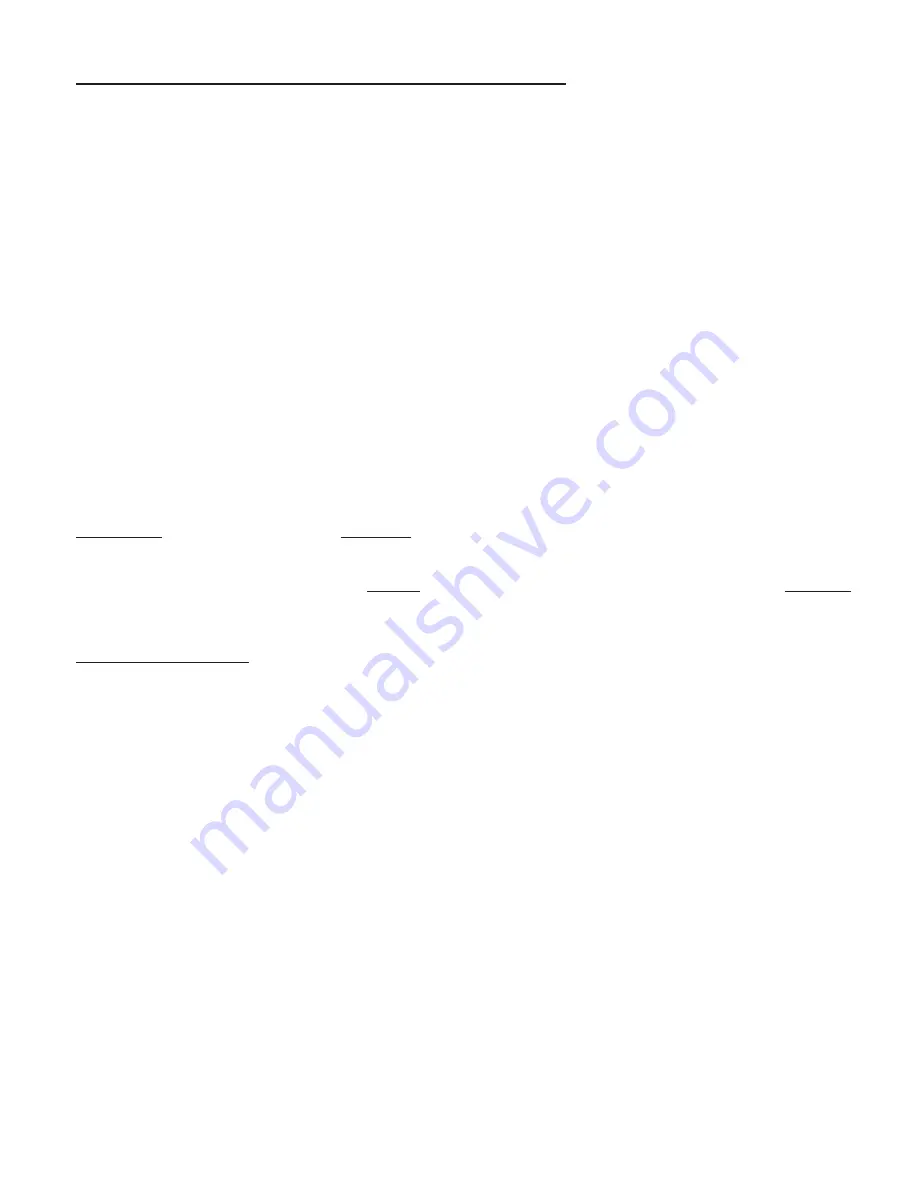
Operating instruction manual
| TX Thermal Disperson Level Switches 5
3.0 CALIBRATION / SET POINT PROCEDURE
Determining High and Low Thermal Conductivity Process conditions
I. It is usually easy to recognize the high and low thermal conductivity conditions when the switch is applied to
liquid and vapor conditions (high and low level detection). The higher TC is almost always when the sensors are
in the liquid phase.
II. There are interface applications where the high and low TC process conditions may not be so obvious.
III. The TX switch itself can be used to identify the high and low TC conditions.
A. Remove power from the TX.
B. Make connections to pins 1 and 3 of P2 (Pin 1 is nearest the green LED).
1. Temporarily insert small pieces of solid wire in P1 or P2; or,
2. Use ABB TX service plug connected to P1 on:
a. Main board (using gender changer adapter) for (single relay output); or,
b. Piggy-back board (dual set point/output, without gender changer adaptor).
c. Pin 1 is green wire; pin 3 is yellow wire on TX service plug.
C. Connect a mV meter to Pin 1 (-) and pin 3 (+)
D. Apply power to the TX. The mV read will be due to the difference in temperature between the Active
Sensor and the Reference Sensor.
E. Change the process conditions at the TX sensors from Normal to Alarm, allowing time to stabilize (5
minutes) and log these mV values.
1. Higher mV value indicates LOW Thermal Conductivity at the sensors (heat is not being
conducted away as well from the Active sensor allowing the temperature of that sensor to
increase).
2. Lower mV value indicates HIGH Thermal Conductivity at the sensors (heat is being conducted
away from the Active sensor, keeping the temperature at lower values.
3.1 Calibrate from HIGH TC (Thermal Conductivity) process conditions as follows:
JP3 State A
- Green LED, output relay
energized
at
NORMAL
condition (High Thermal Conductivity (low differential
temperature) conditions at the sensors); high level (level above sensor), flow above setpoint (see table page 6)
Notes:
1. If the TX switch is operated in
State A
, the TX switch should be adjusted (calibrated) in the
NORMAL
condition; Highest Thermal Conductivity conditions on the sensors (wet sensor, high flow); Green LED and
output relay will be energized during and after calibration.
2. CW rotation of R18 turns LED ON.
Calibration Adjustments
1. Provide the
NORMAL
condition (
HIGH
Thermal Conductivity process condition (high level (level above the
sensors), high flow)) at the sensor. Green LED and output relay
will be
energized after calibration.
2. Allow 5 minutes (minimum time) for switch temperature to stabilize.
3. Adjust R18 (drawing page 5) as follows:
a. If LED is On – slowly turn R18 counter clockwise (CCW) to OFF. Then turn CW until ON.
b. If LED is Off – slowly turn R18 clockwise (CW) until green LED turns ON
4. Turn R18 CW as follows for stable operation (no false alarms) (LED will be On):
a. Air – 1 full turn
b. Organics/Hydrocarbons – 2 full turns
c. Water – 3 full turns
Trimming the TX settings for optimum alarm return to normal time balance if required:
When the LED just turns ON, (3.b. above), the TX “alarm/recovery (return to normal) window” is positioned nearest
to the process’s energized LED Normal (high TC; Low mV) value. This provides the shortest possible time to recog
-
nize (enter) the de-energized alarm condition, but the longest possible recovery time back to the energized (normal)
state.
Step 4 is an attempt to provide closer equal response times (time to enter alarm vs. time to recognize normal condi
-
tions and exit the alarm condition) as well as stability from false alarms.