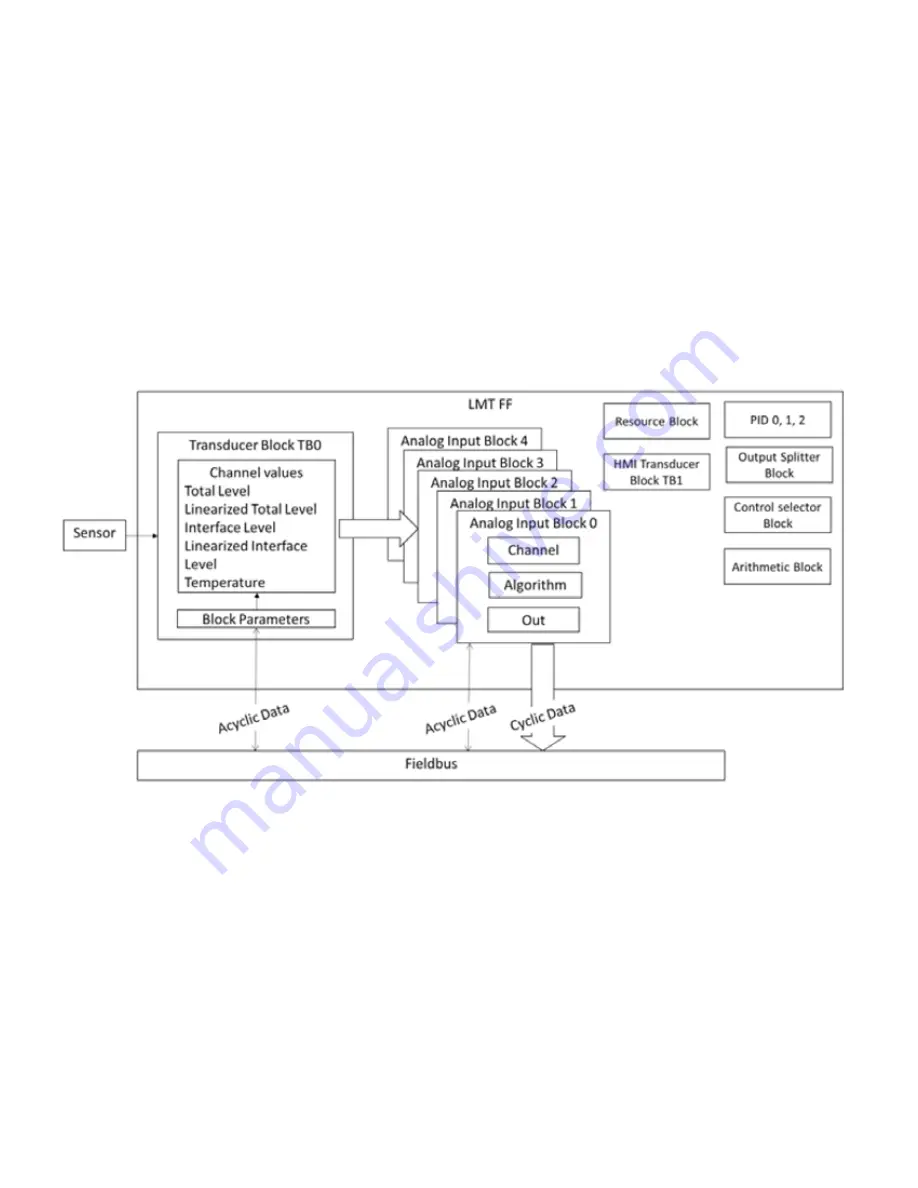
LMT10 0 A N D LMT 20 0 |
M AG N E TOS T R I C T I V E L E V EL T R A N SM I T T ER S | FF O I/L M T 10 0/ 2 0 0/FF - EN R E V. A
65
9 Fieldbus installation considerations
Important Further information on FOUNDATION Fieldbus can
be found from the Fieldbus Foundation organization website
www fieldbus org
Feature overview
The LMT100/200 Foundation Fieldbus are compliant to the
communication Protocol FOUNDATION™ Fieldbus specification
ITK6 3 0
FF Manufacturer ID = 0x000320 (ABB)
FF Device type ID = 0x0096 (LMT Magnetostrictive)
Device Type = Link Master
LMT100/200 FF are implementing the following Blocks:
– 1 Standard Resource Block
– 5 Analog Input Function Blocks
– 3 PID Function Block
– 1 Arithmetic Function Block
– 1 Control Selector Function Block
– 1 Transducer Block with Linearization Table
– 1 HMI Transducer Block
Registration details
All the Registration details are available from the Fieldbus
Foundation webpage
Fieldbus device structure
The Foundation Fieldbus devices can be divided into two parts
under the point of view of technical competence who must take
care of its configuration and use
– The Device Application Process (DAP) is device specific and
stays with the device wherever it is used
– The Control Application Process (CAP) is configured for the
specific plant location and may be spread over multiple
devices
Communication between the DAP and CAP takes place using
channels Each I/O function block in the CAP has exclusive use
of exactly one channel A channel may be bi-directional and it
may have multiple values
Device Application Process (DAP)
The DAP is used primarily by the instrumentation technician or
maintenance personnel for configuring I/O when the
instrument is going to be installed in the plant and/or during
maintenance operations and for this reason mainly focused on
the Resource Block and Transducer Blocks of the device