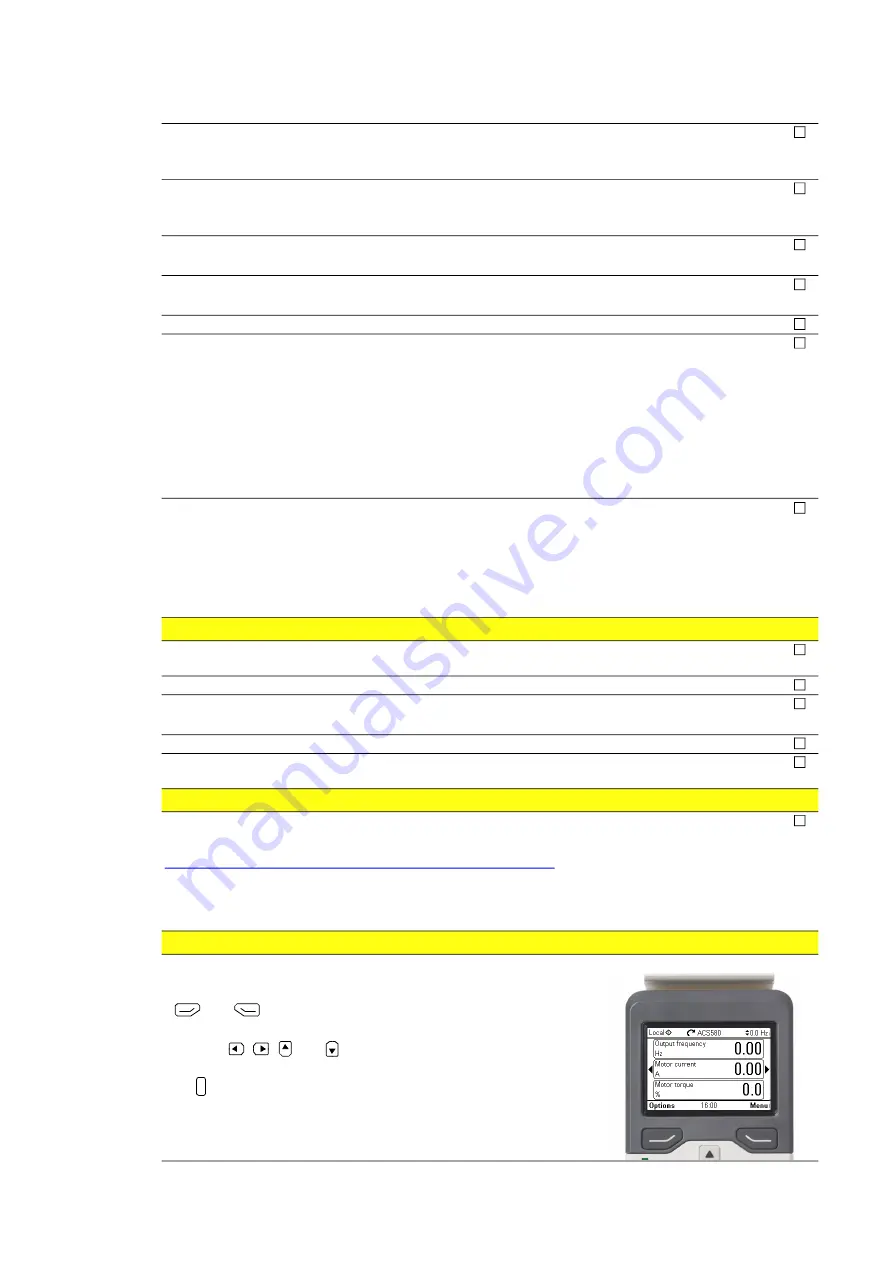
Start-up and operation 19
Units with functional grounding (negative as standard, positive as an F283): Force grounding
from parameter 210.01. Verify the grounding current from parameter 210.14.
If faults or warnings occur, refer to the
Firmware manual
.
Set the grounding mode to “Automated” from parameter 210.01 and configure the grounding to suit the
local requirements.
Refer to the
Firmware manual
.
Set the grid code according to the local requirements.
Refer to the
Firmware manual
.
Adjust parameter 174.01 and 174.02 “M1-2 connected DC inputs” according to the actual
input connection configuration
Verify that no faults or warnings are active. If faults or warnings occur, refer to the
Firmware manual
.
Turn the Start/Stop switch to “start”, set parameter 189.01 to “Enable”, and start the inverter.
A normal starting procedure:
After the start command, the inverter goes from the “Initialize” to the “Disconnected” state (refer to
parameter 173.02). If there is sufficient DC voltage, and the ground impedance is within range, the
inverter goes to the “Connecting” state after the delay set in parameter 213.10.
In this state inverter charges the DC capacitors from the AC output and synchronizes to the grid. The DC
contactor closes. The inverter goes to the MPPT state and starts to produce active power to the AC
output. When there is not enough DC voltage or power available, the inverter goes to the “Disconnecting”
state after the delay set in parameter 213.13.
Make sure that the inverter operates properly from the following actual value parameters:
• 101.01 DC Voltage
• 101.12 Power
• 174.31 to 174.94 where the active input parameters depend on the DC input options (+G417).
The DC voltage should decrease from the open circuit voltage and the active power should match the
line current and the AC voltage.
Set up fieldbus control
Connect the external communications, for example, for the data logger, plant controller or SCADA
system. Obey the safety rules as instructed in the PVS980-58 manuals when doing this.
Configure network interface to match with the local network (refer to the
Firmware manual
).
Set the fieldbus parameters according to the external controller.
Refer to the
Firmware manual
and the fieldbus adapter module manual.
Make sure that the inverter can be seen from the external controller.
Verify that the plant controller receives the correct values from the inverter and sends the correct values
to the inverter.
Register the inverter
Fill in a commissioning report to register the inverter.
The report is on the InstalledBase web page:
https://businessapps.abb.com/sites/DrivesIB4/Pages/default.aspx
If you cannot access the InstalledBase, submit a Membership Request on the Installed Base main page.
Note that InstalledBase is only for ABB internal or ABB partner use.
It is required to attach the parameter lists and back-up files of the inverter. to the report.
Hints on using the assistant control panel
The two commands at the bottom of the display (in the figure on the right,
Options and Menu), show the functions of the two softkeys
and
located below the display.
The commands assigned to the softkeys vary depending on the context.
Use keys , , and to move the cursor and/or change values
depending on the active view.
Key shows a context-sensitive help page.
For more information, refer to
ACS-AP-x assistant control panels user’s
manual
(3AUA0000085685 [English]).
?
Summary of Contents for Fimer PVS980-58-1818kVA-I
Page 1: ...Central inverter PVS980 58 From 1818 to 2091 kVA Commissioning and maintenance manual ...
Page 4: ...2 ...
Page 14: ...12 Safety instructions ...
Page 18: ...16 Introduction to the manual ...
Page 28: ...26 Electrical commissioning ...
Page 60: ...58 Maintenance ...