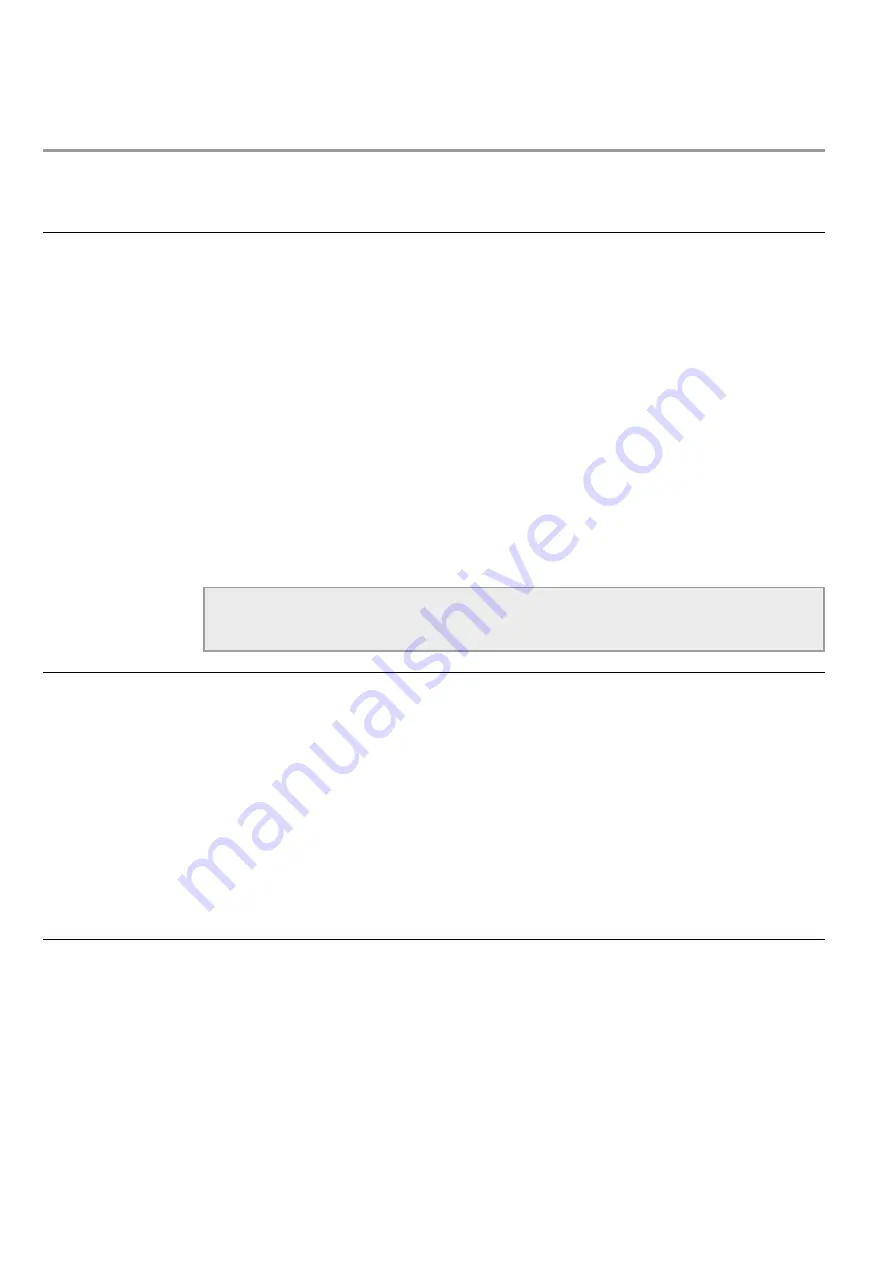
General
Cleaning
The windings must be dried after a wash
or if they have become damp in use or during
a standstill. Drying in an oven with good
ventilation is the most effective technique.
Unfortunately, this is not usually possible at the
motor’s operating site. Therefore, either
hot-air-blow or heating element should be used.
Adequate fresh-air exchange is essential,
whatever heating method is used.
A washed or a very wet motor should be
dismantled and the windings dried in an oven.
When drying in the oven, the temperature rise
and the maximum temperature should be
monitored carefully. The oven temperature
The most important factor in preventive main-
tenance is that everything is clean. The ma-
chine itself and the surroundings must be kept
free from dust, oil and other matter which can
come from the driven object or which can enter
through ventilation openings, etc.
Accumulated dirt on open insulated surfaces
should be removed. This is especially important
when revarnishing the windings because a new
varnish coat will trap any existing dirt beneath
the new coat.
Blowing and vaccuming are used if the dirt
is dry and can be removed easily. Vacuuming
is recommended, since blowing tends to
redistribute the dirt or move it deeper between
the insulation layers.
Wiping is used when spray-wash is not
possible. Surfaces easily reached are wiped
clean with a cloth dampened with detergent.
In cramped areas of windings, a special brush
may be more effective. Low insulation resist-
ance is often caused by dirt on insulated
surfaces, which should be carefully cleaned.
A spray wash is done with an airless high-pres-
sure spray or a conventional spray. The high-
pressure spray is more effective in removing
dirt. The detergent used should remove the dirt
without softening or damaging the insulation.
Avoid using excessive amounts of the cleaning
agent.
A dip wash can be used if the detergent does
not soften or damage the insulation. Since the
dirt is not removed mechanically in this method,
a very effective cleaning and scouring agent is
needed. A long dipping time may be required.
A water wash involves rinsing with water to
prevent the detergents from penetrating into
places where it cannot be removed. A water
wash is done if needed following the instruc-
tions given above for wiping, spray wash or dip
wash. After washing, the windings are rinsed
with clean water several times. Distilled or de-
ionised water is recommended for the final
rinse.
Cleaning of
windings
Drying of
windings
should be 90 °C for 12-16 hours and then 105 °C
for 6-8 hours. The rate of temperature rise of the
windings should not exceed 5 K per hour, and
the final temperature should not exceed 105 °C.
Good ventilation must be ensured to remove the
moisture completely.
The drying of the windings should be followed
by insulation resistance tests. At the beginning
of the drying treatment, the insulation resist-
ance decreases due to the temperature rise. As
the drying continues, however, the insulation
resistance increases until it reaches a maximum
value. Minimum insulation resistance value is
given in chapter “Insulation resistance”.
Caution
Use only detergents specially made for cleaning windings in electrical machines and which do not dam-
age the winding surface or insulation.